After the test verified that the fine grained molding sand is effective in preventing the sand adhesion of the cylinder block casting with the pulverized coal wet mold clay sand, the company also carried out the test of the pulverized coal free wet mold clay sand for the cylinder block casting, and the casting defects to be solved are the sand adhesion and air holes.
1. Experimental scheme
The sand mixing formula of wet clay sand: 1500 kg Zhangwu silica sand (100/200 mesh)+148 kg Jianping bentonite (9%)+(42~45) L water, the wet mixing time is 480 s, and the continuous mixing of three tanks of pulverized coal free sand and two tanks of pulverized coal containing sand is shown in Table 1. The casting used in the test is QF06YF cylinder block, and 10 sets of wet clay sand without pulverized coal and 5 sets of wet clay sand with pulverized coal are poured. See Table 2 for molding process parameters and casting pouring process parameters.
2. Test data of wet clay sand performance
Table 1 shows the comparison of performance test data of molding sand without pulverized coal and with pulverized coal.
Project | Pulverized coal free sand | Pulverized coal sand |
Compaction rate (%) | 44 49 38 | 31 |
Moisture (%) | 2.5 2.4 3.0 | 3.5 |
Air permeability | 70 78 83 | 115 |
Wet compressive strength/kPa | 134 137 158 | 176 |
Effective soil content (%) | 8.4 | 8.57 |
Loss on ignition (%) | 1.4 | 3.7 |
Mud content (%) | 8.18 | 11.38 |
Average fineness AFS | 89.18 | 65.83 |
3. Test data
Table 2 shows the comparison of process test data of pulverized coal free sand and pulverized coal containing sand.
Project | Pulverized coal free sand | Pulverized coal sand |
Sand mold hardness | 82 | 91 |
Sand mold strength/MPa | 0.106~0.148 | 0.138~0.165 |
Sand shooting pressure/bar | 2.3 | 2.3 |
Extrusion pressure/kPa · cm^-2 | 10.2 | 10.2 |
Composition of molten iron (%) | C:3.27; Si:1.73; Mn:0.52; S:0.104; P:0.044 | C:3.27; Si:1.73; Mn:0.52; S:0.104; P:0.044 |
Inoculant ratio | Once: 0.3%; Secondary: 0.2%; Follow flow: 4.5 g/s | Once: 0.3%; Secondary: 0.2%; Follow flow: 4.5 g/s |
Iron output/kg | 800 | 800 |
Pouring temperature/℃ | 1 421 | 1 418 |
Number of pouring boxes/piece | 10 | 5 |
Shot blasting time/min | 10 | 10 |
Molding and demoulding situation: due to the high compaction rate and low strength, the demoulding of the sand mold without pulverized coal is slightly with sand, and the sand mold around the casting silencing cavity is not compacted by sand blasting (Fig. 1), and the demoulding effect of the sand mold with pulverized coal is relatively good (Fig. 2). There are obvious blue flames and smoke in the sand containing pulverized coal (Fig. 3).
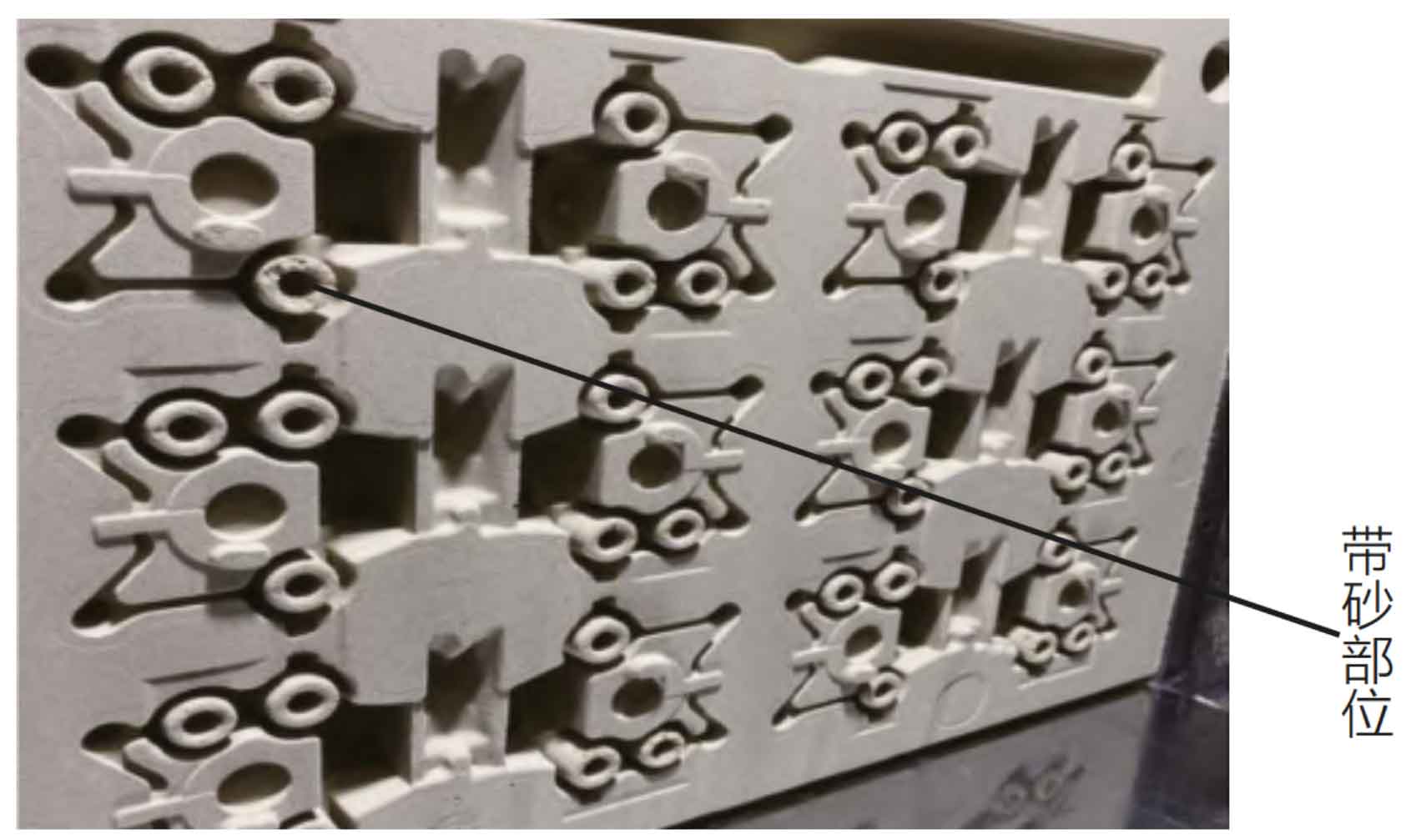
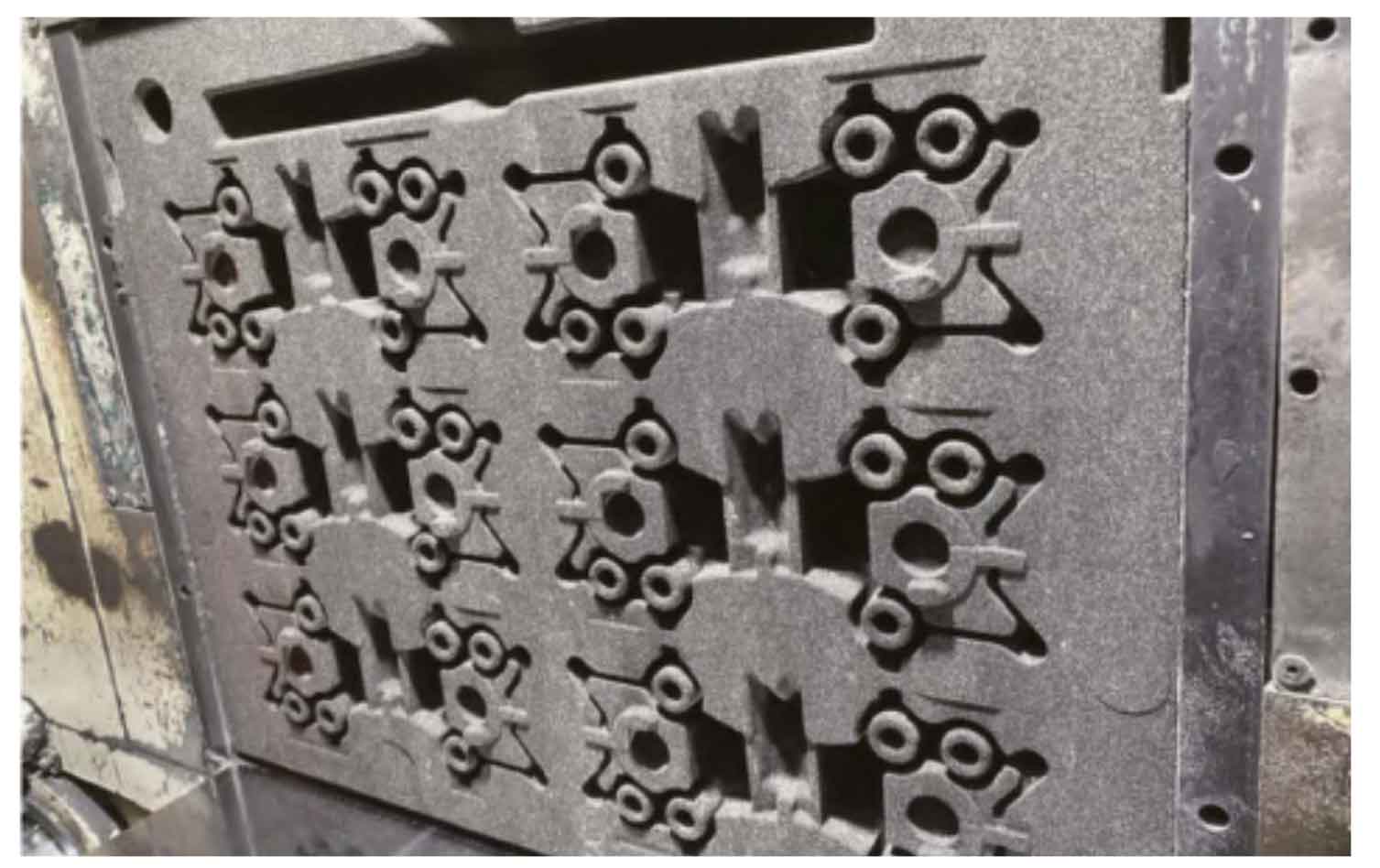
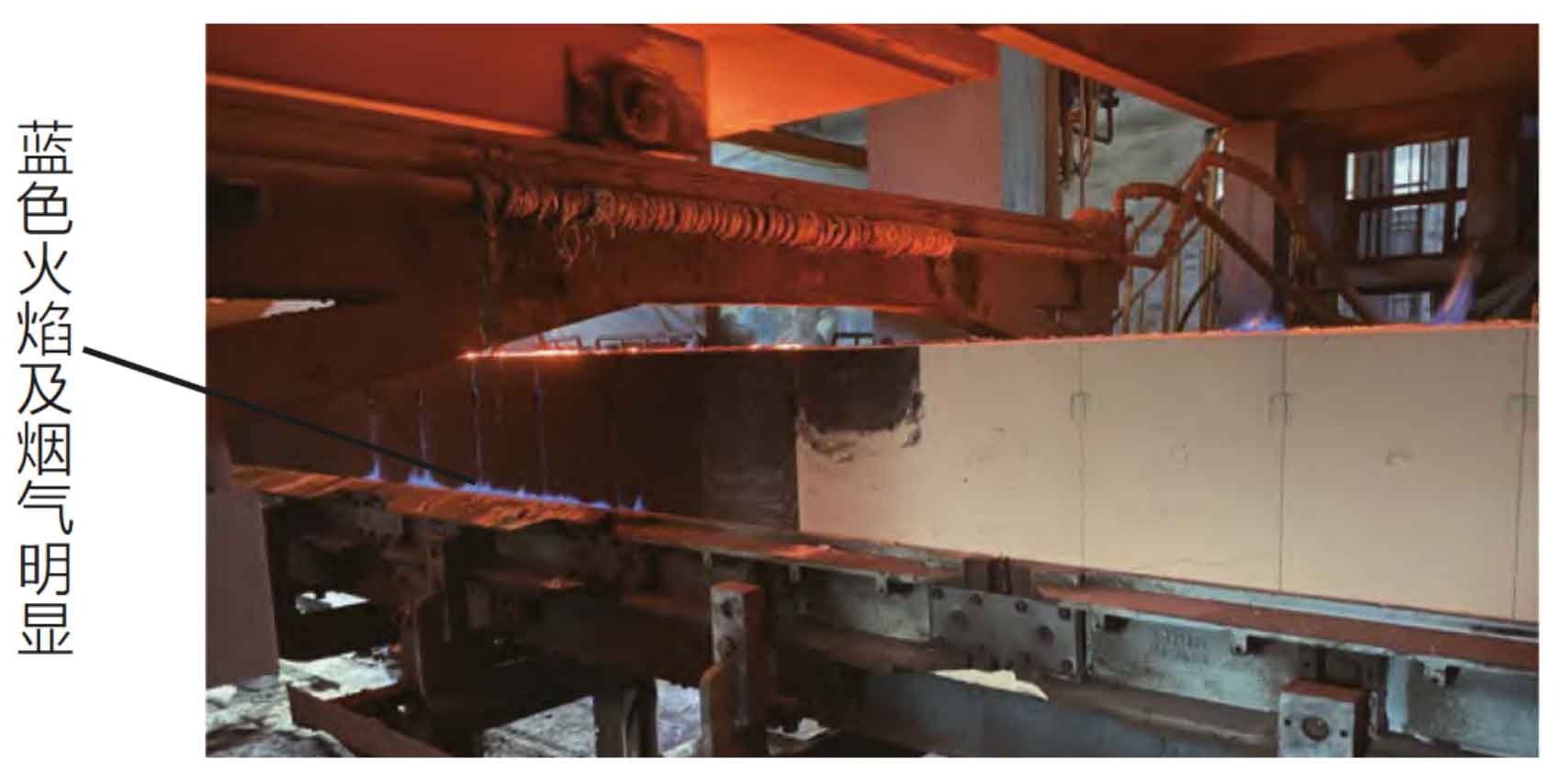
Compared with the surface quality of the castings, the surface roughness of the castings without pulverized coal sand is higher than that of the castings with pulverized coal sand, and there is no sand sticking defect in the silencing cavity of the castings without pulverized coal sand and with pulverized coal sand (Fig. 4).
4. Test results
Table 3 shows the comparison of performance data between pulverized coal free sand and pulverized coal containing sand.
Project | Pulverized coal free sand | Pulverized coal sand |
Internal flaw detection | No porosity and shrinkage | No porosity and shrinkage |
Cylinder head hardness (HBW) | 184;184;189 | 179;179;177 |
Foot hardness (HBW) | 193;207;234;235 | 185;191;218;226 |
Foot metallography | D-type graphite, edge 30% P, center 75%~85% P | A+D+E graphite, 35%~45% P at the edge, 85% P at the center |