1. Microstructure
The microstructure photos of titanium containing aluminum alloy ADC12-0.25Ti samples cast at different temperatures are shown in Figure 1. It can be seen from Figure 1 that with the pouring temperature increasing from 690 ℃ to 750 ℃, the grain size of the sample is basically unchanged at first and then increases sharply. When the pouring temperature is 690 ℃ and 720 ℃, the internal structure of the sample is fine and the structure distribution is uniform; When the pouring temperature is increased to 750 ℃, the grain of the sample is obviously coarsened and the uniformity of the microstructure distribution becomes worse.
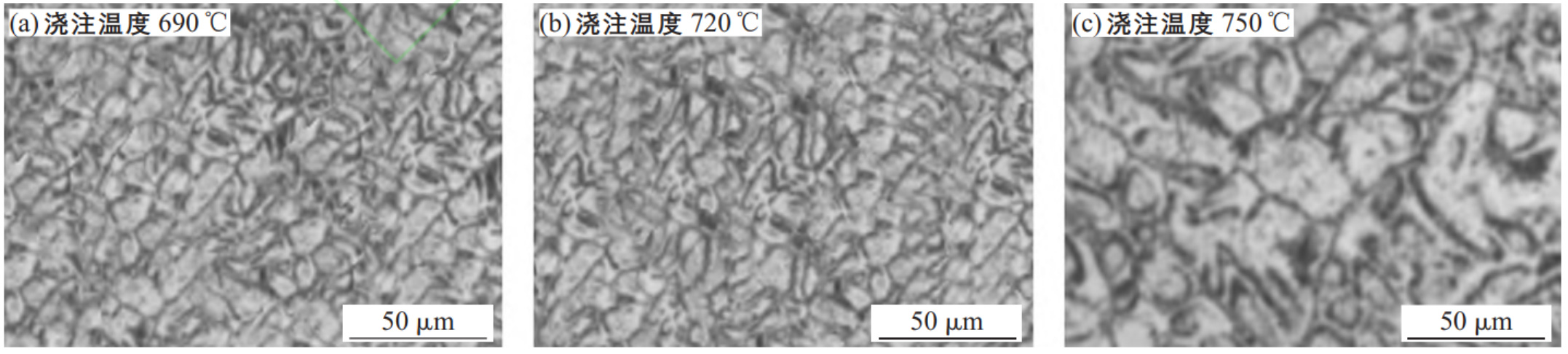
2. Liquidity
The fluidity test results of ADC12-0.25Ti samples cast at different temperatures are shown in Figure 2. It can be seen from Figure 2 that pouring temperature is an important factor affecting the fluidity of alloy samples. With the pouring temperature increasing from 690 ℃ to 750 ℃, the length of molten aluminum flow of the alloy sample increases gradually, and the fluidity of the alloy sample increases gradually. When the pouring temperature is 690 ℃, the length of molten aluminum flow is the shortest (516 mm); When the pouring temperature is 750 ℃, the length of molten aluminum flow is the longest (587mm), which is 71mm longer than that at 690 ℃. It can be seen that the increase of pouring temperature is beneficial to improve the fluidity of new titanium containing aluminum alloy for automotive castings.
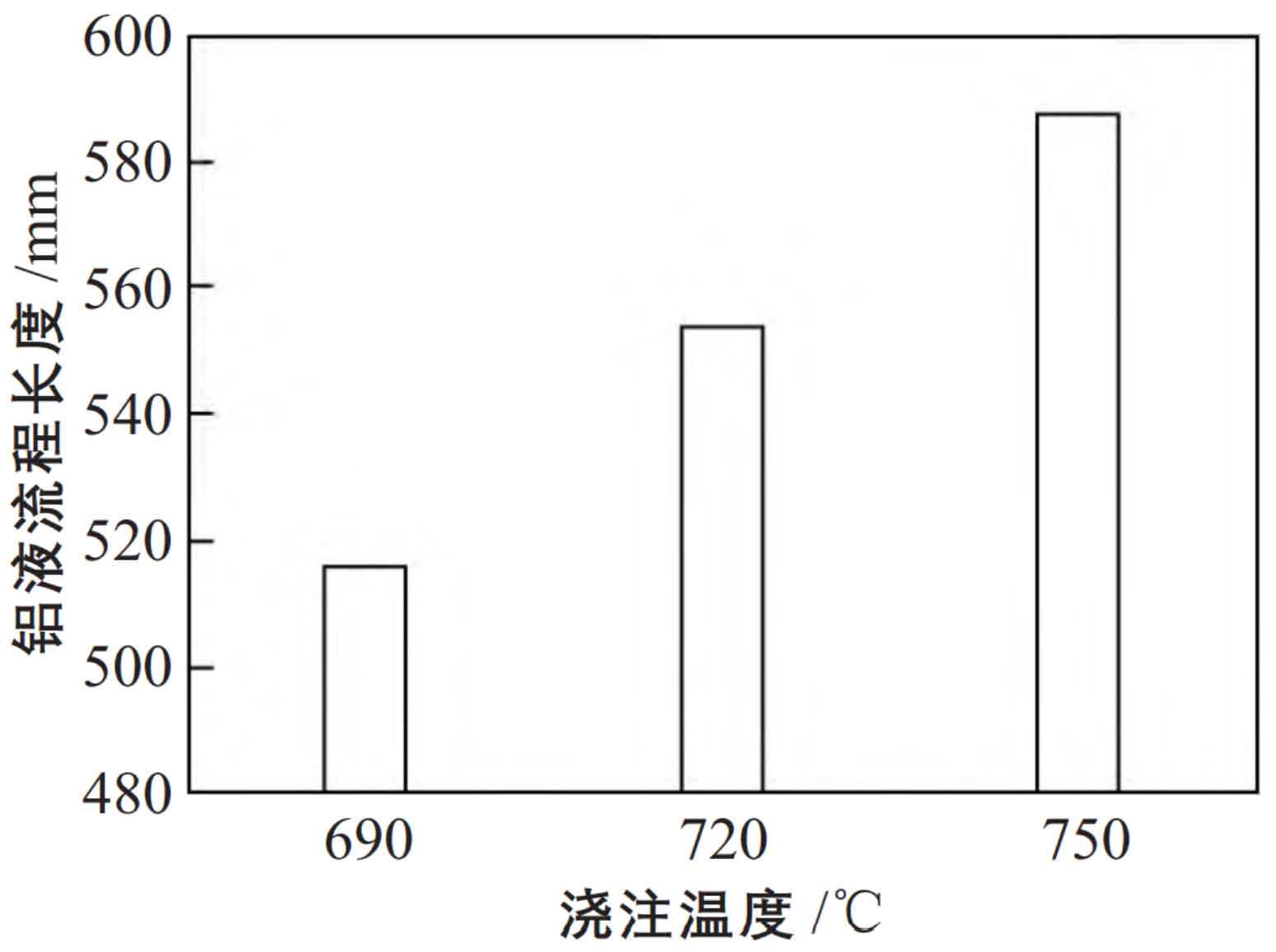
3. Thermal cracking resistance
The hot crack resistance test results of ADC12-0.25Ti aluminum alloy samples cast at different temperatures are shown in Figure 3. It can be seen from Figure 3 that pouring temperature is an important factor affecting the hot cracking resistance of alloy samples. With the pouring temperature increasing from 690 ℃ to 750 ℃, the crack length of the alloy sample shows a trend of first decreasing and then increasing, and the hot crack resistance of the alloy sample first increases and then decreases. When the pouring temperature is 690 ℃, the crack length is 3.2 mm; When the pouring temperature is 720 ℃, the crack length is 0.3 mm, which is 2.9mm less than that of 690 ℃; When the pouring temperature was 750 ℃, the crack length was 6.6 mm, which increased by 3.4 mm compared with 690 ℃. It can be seen that properly increasing the pouring temperature is helpful to improve the hot cracking resistance of the test aluminum alloy, but too high pouring temperature will deteriorate its hot cracking resistance.
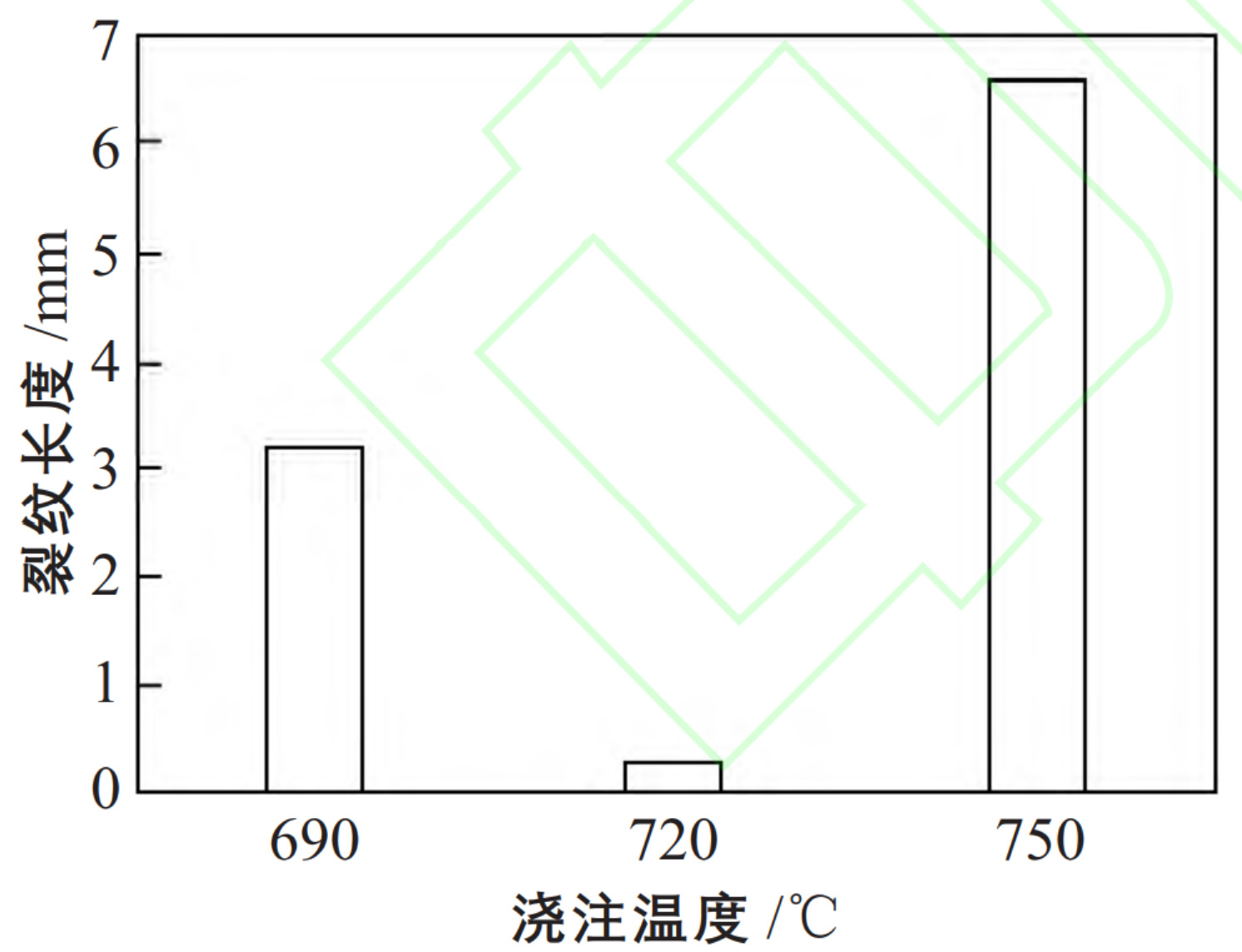
In the casting process of ADC12-0.25Ti aluminum alloy, pouring temperature is an extremely important process parameter. If the pouring temperature is too low, the viscosity of molten aluminum alloy liquid is too high, and the fluidity of molten aluminum is poor. During pouring, it is easy to produce cold shuts, which will block the feeding channel and easily produce shrinkage defects. In addition, too low pouring temperature is not conducive to the floating of slag inclusions, which will reduce the cleanliness of aluminum alloy and lead to poor hot cracking resistance of the alloy. Properly increasing the pouring temperature will help to reduce the viscosity of molten aluminum, improve the fluidity of molten aluminum, promote the floating of slag, improve the cleanliness of the alloy and improve the hot cracking resistance of the alloy. When the pouring temperature is too high, although it helps to float the slag and obtain aluminum alloy ingots with high cleanliness, the internal structure of aluminum alloy is coarsened, and shrinkage porosity and other defects may occur; In addition, it will increase energy consumption, extend production cycle and reduce production efficiency. Therefore, it is of great practical significance to select a reasonable pouring temperature in the casting process of titanium containing ADC12-0.25Ti aluminum alloy for automotive parts. The pouring temperature should not be too high or too low.