Investment casting, also known as lost-wax casting, offers several advantages in terms of precision and quality, making it a preferred choice in manufacturing. Let’s explore some key advantages of investment casting:
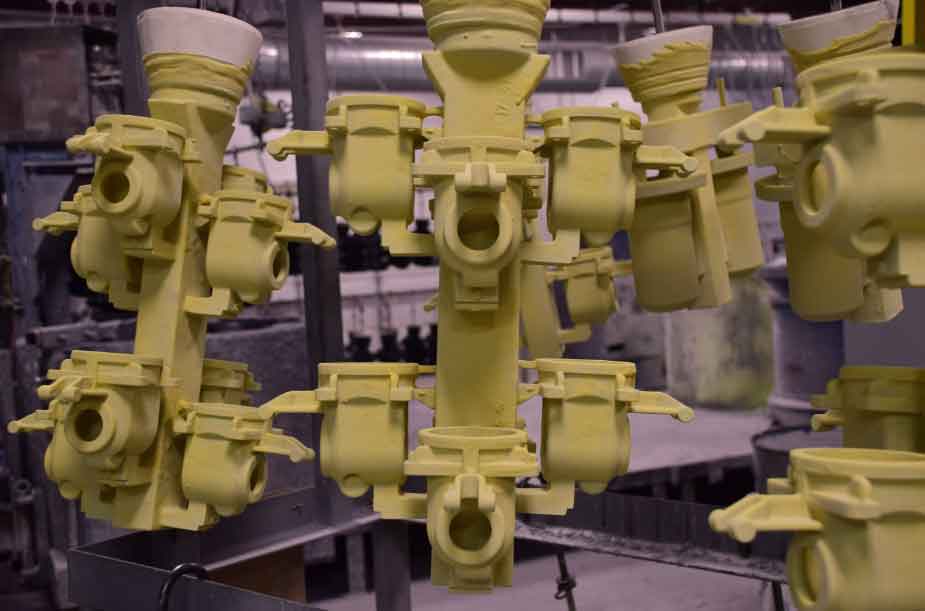
1. Dimensional Accuracy:
Investment casting produces components with excellent dimensional accuracy and tight tolerances. The process allows for the replication of intricate details and complex geometries, ensuring that the final castings match the design specifications precisely. This high level of dimensional accuracy reduces the need for extensive post-casting machining, saving time and cost.
2. Surface Finish:
Investment casting provides superior surface finish compared to other casting methods. The ceramic molds used in the process produce smooth and precise surfaces, minimizing the need for additional surface treatments or finishing operations. This results in castings with high-quality surface finishes that meet the desired aesthetic and functional requirements.
3. Complex Geometries:
Investment casting is well-suited for manufacturing components with complex geometries. The process can produce intricate shapes, thin walls, and internal features that may be challenging or impossible to achieve using other casting methods. This allows for the production of highly customized and intricate parts with minimal material wastage.
4. Design Flexibility:
Investment casting offers design flexibility, allowing engineers to create complex and innovative designs. The use of wax or resin patterns enables designers to modify and iterate on the design easily. This flexibility opens up possibilities for optimizing the design for better functionality, weight reduction, or cost savings.
5. Near-Net Shape Manufacturing:
Investment casting is a near-net shape manufacturing process, which means that the castings are produced very close to the final desired shape. This reduces the amount of material and machining required, minimizing material wastage and saving both time and cost in the overall production process.
6. Material Versatility:
Investment casting supports a wide range of materials, including various metals and alloys. This versatility allows manufacturers to choose the most suitable material for specific applications, considering factors such as mechanical properties, corrosion resistance, or temperature resistance. This ensures that the final castings meet the required performance and quality standards.
7. Consistency and Reproducibility:
Investment casting ensures consistent and reproducible results, even in high-volume production. The use of standardized processes, precise mold-making techniques, and strict quality control measures contribute to the production of castings with consistent quality characteristics. This is particularly important for industries where reliability and uniformity are critical.
8. Reduced Post-Casting Machining:
Investment casting minimizes the need for extensive post-casting machining. The high dimensional accuracy and near-net shape production reduce the amount of material to be removed, resulting in significant time and cost savings. This makes investment casting a cost-effective option for producing complex components that require high precision.
Investment casting’s advantages in precision and quality make it an ideal choice for manufacturing intricate, high-quality components. The process allows for the production of complex geometries, near-net shape castings, and components with excellent dimensional accuracy and surface finish. With its design flexibility, material versatility, and consistency, investment casting provides manufacturers with a reliable and efficient method to produce precise and high-quality castings for a variety of industries and applications.