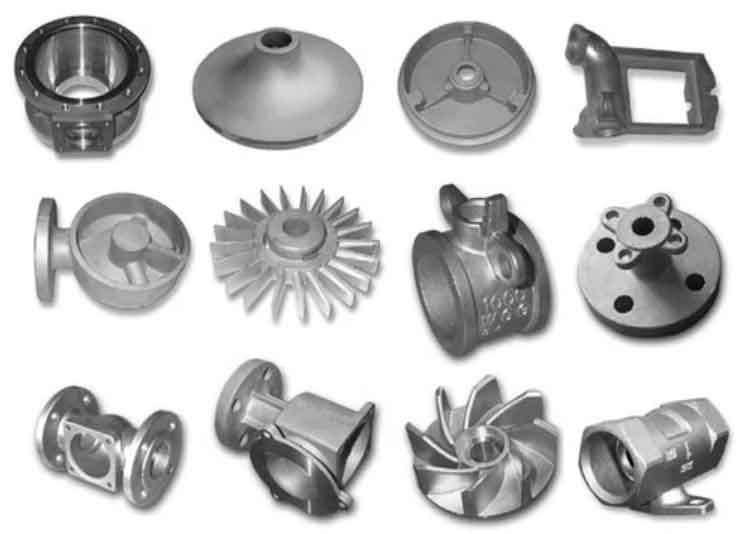
Steel castings offer several advantages that make them well-suited for critical engineering applications. These advantages include:
- Strength and Durability: Steel castings are known for their high strength and durability. They can withstand heavy loads, high temperatures, and extreme operating conditions without experiencing deformation or failure, making them ideal for critical components in demanding environments.
- Versatility: Steel castings can be produced in a wide range of shapes and sizes, allowing for customized designs to meet specific engineering requirements. This versatility makes them suitable for various applications in different industries.
- Complex Geometries: The casting process allows for the creation of intricate and complex shapes that might be challenging or expensive to produce using other manufacturing methods. This capability is particularly beneficial in critical engineering applications where precise geometries are essential.
- Cost-Effectiveness: Steel castings can offer cost advantages compared to other manufacturing methods, especially for large and complex components. The ability to create near-net-shape parts reduces the need for extensive machining, resulting in cost savings.
- Corrosion Resistance: Steel castings can be alloyed to provide excellent corrosion resistance, making them suitable for applications in harsh environments, such as marine, chemical, and oil and gas industries.
- Wear Resistance: Alloyed steel castings can exhibit excellent wear resistance, making them suitable for components subjected to abrasive or erosive forces, such as pump impellers and valve components.
- Machinability: Some steel castings are specifically designed for easy machinability, allowing for post-casting operations when precise tolerances are required.
- Temperature Resistance: Steel castings can maintain their mechanical properties at elevated temperatures, making them suitable for applications in high-temperature environments, such as power generation and aerospace.
- Consistency and Reproducibility: Steel casting processes can achieve high levels of consistency and reproducibility, ensuring that each casting meets the required quality standards, essential for critical engineering applications.
- Reduced Welding: In some cases, steel castings can eliminate the need for welding, reducing the risk of weld-related defects and improving the overall integrity of the component.
- Non-Destructive Testing (NDT): Steel castings can undergo non-destructive testing techniques, such as ultrasonic testing and radiography, to detect any internal defects or flaws, ensuring the reliability of the finished product.
Due to these advantages, steel castings are widely used in critical engineering applications such as aerospace components, power generation equipment, oil and gas industry components, heavy machinery, marine equipment, and more. Their exceptional properties and performance characteristics make them a reliable choice for ensuring the safety, efficiency, and longevity of critical systems and structures.