1. Grid division
In the AWB platform, the patch independent method is used to divide the tetrahedral mesh. At the same time, the Min size limit is 0.2mm, the max element size is 2mm, and the advanced size function (proximity and curvature) is enabled. The grid number is about 1.9 million, and the maximum skewness is about 0.65.
2. Calculation conditions
The valve body material is QT500-7, the density is 7270 kg / m3, Young’s modulus is 1.835 × 1011pa, Poisson’s ratio is 0.27, the tensile strength limit is 500MPa, the yield limit is 320MPa, the fatigue strength weakening coefficient KF = 0.8, and the design life of the valve body is 106 cycles.
3. Constraints and loads
Adopt fixed support constraint. In the static strength analysis, pressure is applied to the two cavities of the valve body and the inlet and outlet oil passages; in the fatigue analysis, considering the cyclic process of the pressure change in the valve cavity from 0 to working pressure and then from working pressure to 0 due to the operation of the hydraulic valve, the fluctuating cyclic load of R = 0 is selected to simulate the alternating load in the valve cavity.
4. Result analysis
Figure 1 is the ideal valve body stress cloud chart when the pressure is 30MPa. It can be seen from the figure that the maximum stress of the ideal valve body is 125.86mpa, which is distributed on the edge of the inlet of the valve body’s large groove, close to the side of the small groove. This is because the edge of this part is obvious, which is easy to cause stress concentration.
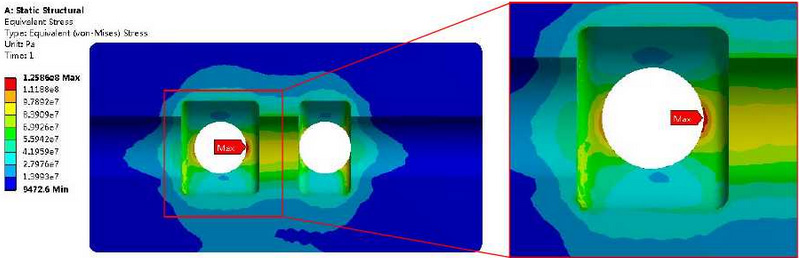
Fig. 2 is a cloud chart of the distribution of the fatigue safety factor of the ideal valve body when the pressure is 30MPa. It can be seen from the figure that the minimum fatigue safety factor distribution of the ideal valve body is the same as the maximum stress distribution of the valve body, and the minimum fatigue safety factor is 2.0244.
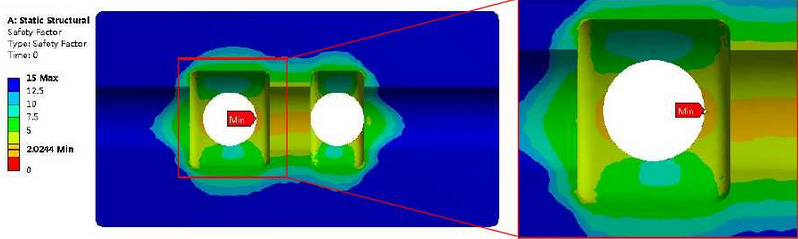