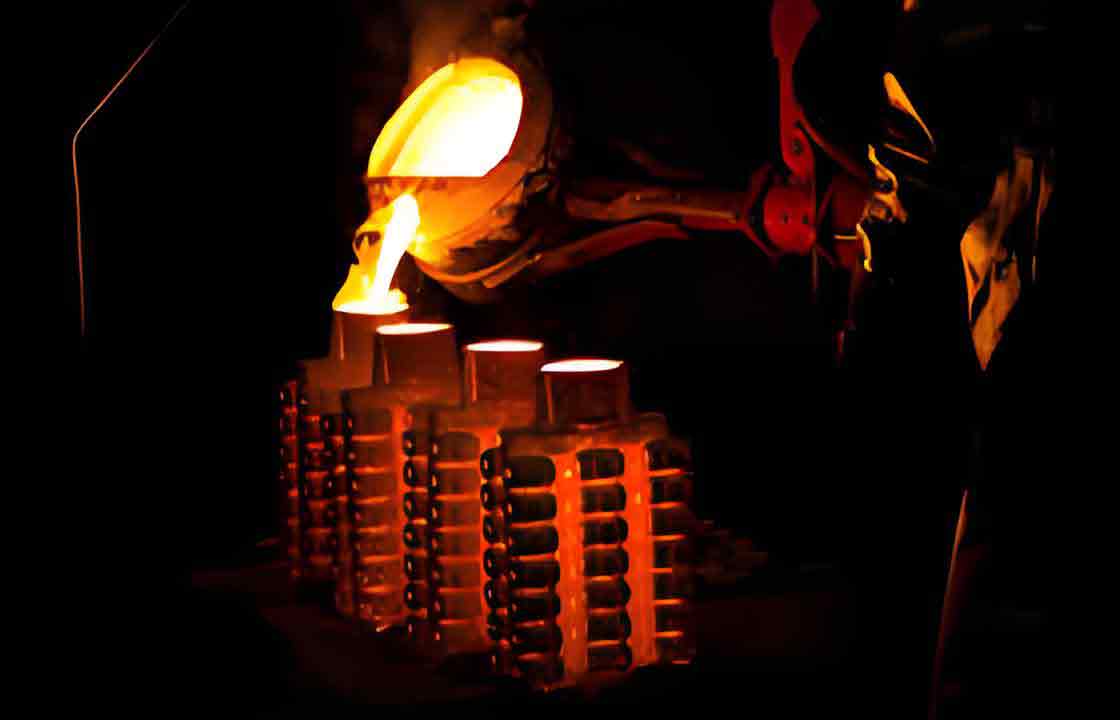
The Investment Casting Process is a manufacturing technique that involves creating detailed and precise metal components. This process is valued for its ability to produce intricate designs with excellent surface finishes and dimensional accuracy. This article provides a comprehensive overview of the Investment Casting Process, detailing its steps, advantages, limitations, and applications.
Introduction to Investment Casting Process
The Investment Casting Process has been used for thousands of years, tracing its origins back to ancient civilizations. It involves creating a wax pattern, which is then coated with a ceramic shell to form a mold. The wax is melted away, and molten metal is poured into the cavity left behind. The result is a highly detailed and accurate metal part.
Steps in the Investment Casting Process
The Investment Casting Process consists of several steps, each critical to achieving the final high-quality product. The following sections outline these steps in detail:
- Pattern Creation
- Assembly of Wax Patterns
- Shell Building
- Dewaxing
- Metal Pouring
- Shell Removal
- Finishing
Pattern Creation
The first step in the Investment Casting Process is the creation of the wax pattern. This pattern is an exact replica of the final metal part. The wax pattern is typically made using injection molding, where wax is injected into a metal mold. Wax patterns can be produced individually or as multiple patterns attached to a central wax sprue.
Assembly of Wax Patterns
Once the wax patterns are created, they are assembled into a tree-like structure called a wax assembly. The wax assembly consists of multiple wax patterns attached to a central wax sprue, which will eventually become the gating system for the molten metal.
Shell Building
The assembled wax patterns are then coated with a ceramic slurry to form a shell. The shell building process involves several steps:
- Dipping: The wax assembly is dipped into a ceramic slurry.
- Stuccoing: The dipped assembly is coated with fine sand or stucco while the slurry is still wet.
- Drying: The coated assembly is allowed to dry.
- Repeating: These steps are repeated multiple times to build up a thick ceramic shell.
Dewaxing
After the shell is built, the wax inside the shell is melted and removed in a process called dewaxing. This is typically done in an autoclave, where steam or hot water is used to melt the wax, leaving behind a hollow ceramic shell.
Metal Pouring
Once the wax is removed, the ceramic shell is preheated to remove any residual moisture and to prepare it for the molten metal. Molten metal is then poured into the shell, filling the cavity left by the wax pattern.
Shell Removal
After the metal has cooled and solidified, the ceramic shell is broken away to reveal the cast metal part. This is done using mechanical methods, such as hammering or water blasting.
Finishing
The final step in the Investment Casting Process is the finishing of the cast metal part. This involves removing the gating system, grinding, machining, and any other necessary finishing processes to achieve the desired dimensions and surface finish.
Summary of Investment Casting Process Steps
Step | Description |
---|---|
Pattern Creation | Creating a wax pattern replica of the final metal part |
Assembly of Wax Patterns | Assembling wax patterns into a tree-like structure |
Shell Building | Coating wax assembly with ceramic slurry to form a shell |
Dewaxing | Melting and removing the wax from the ceramic shell |
Metal Pouring | Pouring molten metal into the ceramic shell |
Shell Removal | Breaking away the ceramic shell to reveal the cast part |
Finishing | Removing gating system and finishing the cast part |
Advantages of Investment Casting Process
The Investment Casting Process offers several advantages, making it a popular choice for producing complex metal components:
- Intricate Designs: The process allows for the creation of highly detailed and complex shapes that would be difficult or impossible to achieve with other casting methods.
- Excellent Surface Finish: Investment casting produces parts with smooth surfaces, reducing the need for extensive finishing work.
- Dimensional Accuracy: The process provides excellent dimensional accuracy, often eliminating the need for machining.
- Material Versatility: A wide range of metals and alloys can be used, including stainless steel, aluminum, and titanium.
- Reduced Waste: The process minimizes material waste, as the gating system is designed to be as efficient as possible.
Advantages Summary
Advantage | Description |
---|---|
Intricate Designs | Allows for detailed and complex shapes |
Excellent Surface Finish | Produces parts with smooth surfaces |
Dimensional Accuracy | Provides high precision, reducing need for machining |
Material Versatility | Suitable for a wide range of metals and alloys |
Reduced Waste | Minimizes material waste through efficient gating system |
Limitations of Investment Casting Process
Despite its advantages, the Investment Casting Process has some limitations:
- High Initial Cost: The cost of creating molds and patterns can be high, especially for low-volume production.
- Size Limitations: The process is typically used for smaller parts; larger parts may be impractical or too expensive.
- Long Lead Times: The multiple steps involved can lead to longer production times compared to other casting methods.
- Complex Process: The Investment Casting Process is more complex than other casting methods, requiring skilled labor and precise control.
Limitations Summary
Limitation | Description |
---|---|
High Initial Cost | Expensive molds and patterns, especially for low volumes |
Size Limitations | Typically used for smaller parts |
Long Lead Times | Multiple steps result in longer production times |
Complex Process | Requires skilled labor and precise control |
Applications of Investment Casting Process
The Investment Casting Process is used across various industries due to its ability to produce precise and complex components. Some common applications include:
Aerospace Industry
In the aerospace industry, the Investment Casting Process is used to manufacture:
- Turbine Blades: Components for jet engines and gas turbines.
- Structural Components: Various structural parts used in aircraft.
Automotive Industry
In the automotive industry, the Investment Casting Process is used for:
- Engine Components: Parts such as manifolds, pistons, and cylinder heads.
- Transmission Parts: Gears, housings, and other transmission components.
Medical Industry
In the medical industry, the Investment Casting Process is used to create:
- Surgical Instruments: Precision instruments used in surgeries.
- Orthopedic Implants: Components for joint replacements and other implants.
Industrial Machinery
In industrial machinery, the Investment Casting Process is used for:
- Pump Components: Parts such as impellers, casings, and diffusers.
- Valves: Various types of valves for fluid handling systems.
Summary of Investment Casting Process Applications
Industry | Application |
---|---|
Aerospace | Turbine blades, structural components |
Automotive | Engine components, transmission parts |
Medical | Surgical instruments, orthopedic implants |
Industrial Machinery | Pump components, valves |
Conclusion
The Investment Casting Process is a highly versatile and precise manufacturing method that enables the production of intricate and detailed metal components. By understanding the detailed steps involved, the advantages and limitations, and the wide range of applications, manufacturers can effectively utilize this process to produce high-quality parts. From aerospace and automotive to medical and industrial machinery, the Investment Casting Process continues to be a critical technology in the world of manufacturing.