The core technology of investment casting of superalloy is the optimization and preparation process of core and shell material system. The investment casting of superalloy in China started from the wet molding process of paraffin – stearic acid mold material and water glass – quartz shell plus bauxite cement introduced from the Soviet Union in the 1950s. In 1965, the Beijing Institute of Aeronautical Materials successfully cast the WP – 6 engine superalloy turbine blade using this process. Subsequently, the Beijing Institute of Aeronautical Materials continuously developed and produced the high cooling efficiency single crystal laminate alloy turbine blade in the late 1990s. With the help of the casting technology, the ultra-gas-cooled single crystal blade was manufactured by one-time precise forming. With the help of soluble core technology and investment casting technology, the Russian Saturn Scientific Research and Production Consortium has realized the mass production of high-efficiency air-cooled single crystal hollow blades, which has been successfully applied to the AL – 31FN engine (see figure).
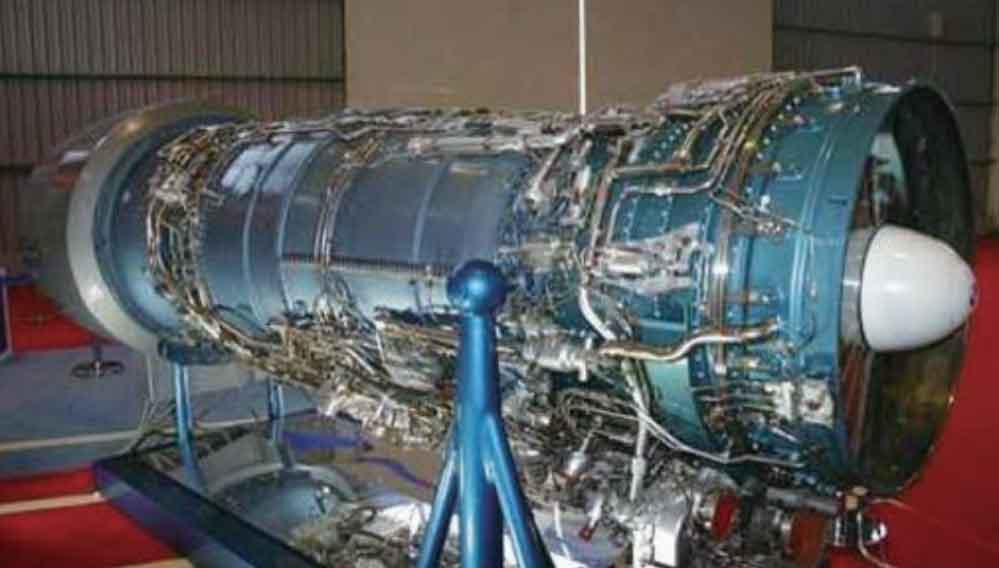
At the end of the 20th century, Carret and PCC broke through the “metallurgy – grain – structure” in-situ composite control technology of large thin-walled complex superalloy investment castings. The maximum forming size of the engine casing investment castings manufactured by this technology is 1027mm, the wall thickness can reach 0.8~1.2mm, the grain size can be controlled in 1.0~5.0mm, and the material utilization rate has increased by more than 50%. At present, foreign countries have formed new technologies for manufacturing super air-cooled hollow blades, such as porous laminates alloy parts, single crystal blades cast by porous laminates alloy, super air-cooled hollow blades, micro laminated composite blades, and corresponding divergent cooling, cast cooling, super cooling.