Grey cast iron, also known as gray iron, is a type of cast iron known for its characteristic grey color, which it attains due to the presence of graphite flakes in its microstructure. This guide aims to delve into the metallurgy of grey cast iron, exploring its composition, microstructure, and phase transformations.
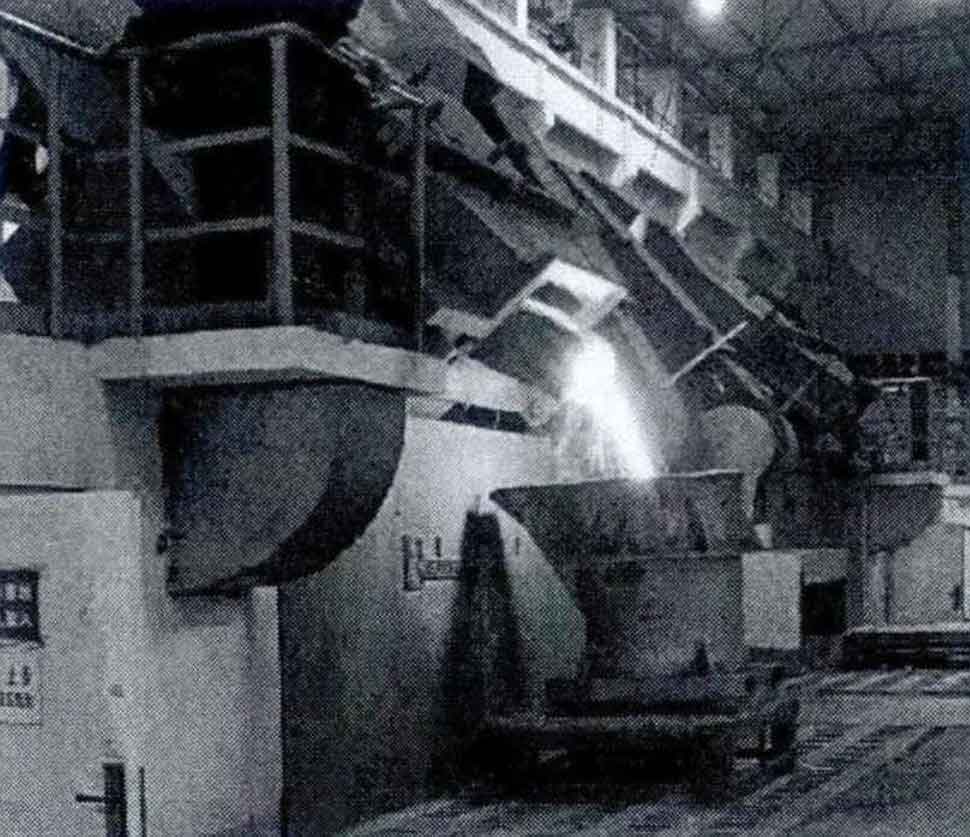
Composition and Microstructure
Grey cast iron, like other types of cast iron, has a carbon content of more than 2%. However, what sets it apart is the form in which this carbon exists. In grey cast iron, the carbon is present primarily as graphite flakes dispersed in a matrix that can be either ferritic or pearlitic.
The formation of these graphite flakes is a direct result of the cooling process following casting. As the molten iron alloy begins to cool, carbon comes out of the solution and precipitates as graphite. These flakes have sharp edges, giving them a look similar to fractured glass when the material is broken, leading to the grey appearance that gives this material its name.
Phase Transformations
The casting process and the subsequent cooling rate play a crucial role in determining the microstructure of the grey cast iron. Slower cooling rates favor the formation of graphite over carbide (iron carbide, also known as cementite), leading to the characteristic microstructure of grey cast iron.
The first phase transformation occurs when the molten iron alloy begins to cool, and the austenite (γ-Fe), a high-temperature phase of iron, starts to form. As the temperature continues to drop, the carbon in the austenite starts to form graphite flakes.
Upon further cooling, the austenite transforms into either ferrite (α-Fe) or pearlite, depending on the cooling rate and the exact composition of the alloy. Ferrite is a relatively soft form of iron, whereas pearlite is a mixture of ferrite and cementite that offers greater hardness and strength.
Effects of Alloying Elements
Like other ferrous materials, grey cast iron’s properties can be modified by adding different alloying elements. For instance:
- Silicon: An important element in grey cast iron, silicon promotes the formation of graphite, thereby ensuring the development of the grey cast iron structure. It also improves the oxidation resistance of the material.
- Manganese: This element ties up with sulfur and forms manganese sulfide, thus preventing the formation of iron sulfide, which can lead to hot shortness.
- Phosphorus and Sulfur: Generally considered impurities, these elements can lead to brittleness. They’re typically kept to a minimum in the alloy.
Understanding the metallurgy of grey cast iron allows for better control over its properties, ensuring that it can be tailored to meet the specific demands of various applications. This versatile material, with its unique combination of excellent castability, machinability, and vibration damping capacity, continues to find extensive use in industries ranging from automotive to construction.