The production of Spheroidal Graphite Cast Iron (SGCI), also known as ductile iron, like any industrial manufacturing process, has environmental impacts and sustainability considerations. Understanding and addressing these aspects are essential for minimizing ecological footprints and promoting sustainable practices. Let’s explore the environmental impact and sustainability of Spheroidal Graphite Cast Iron production:
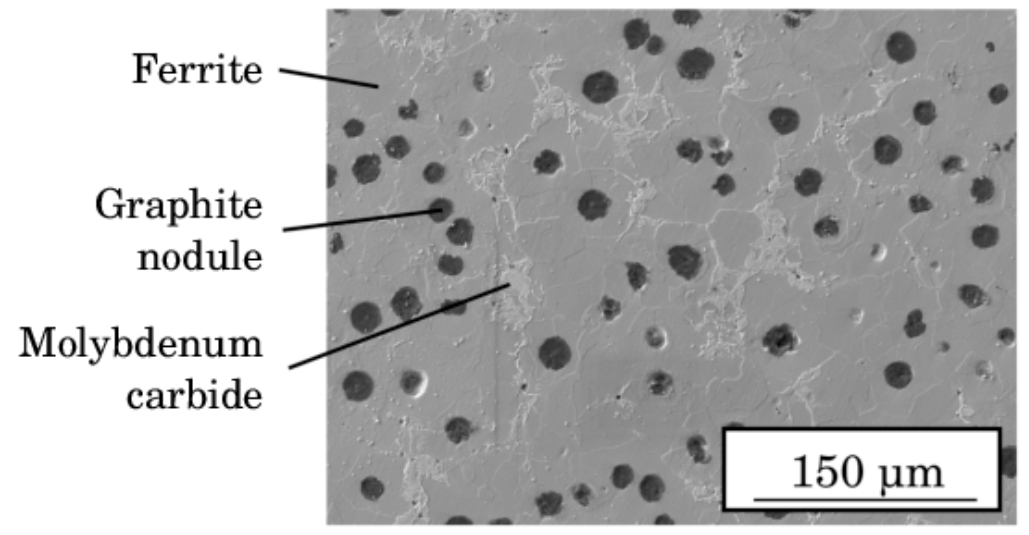
Environmental Impact
- Energy Consumption: The melting process in Spheroidal Graphite Cast Iron production is energy-intensive, primarily due to high temperatures required for melting iron. This contributes significantly to the overall energy consumption of the foundry.
- Emissions: Spheroidal Graphite Cast Iron production involves the emission of greenhouse gases (GHGs) and other pollutants. Carbon dioxide (CO2) is emitted during the melting process, and other gases like sulfur dioxide (SO2) and nitrogen oxides (NOx) can also be released.
- Use of Nodulizing Agents: The addition of magnesium or cerium to create the spheroidal graphite structure leads to the emission of fumes and particulates, which need to be properly managed to reduce air pollution.
- Waste Generation: The production process generates various forms of waste, including slag, used foundry sand, and particulate matter. Managing and disposing of these wastes pose environmental challenges.
Sustainability Practices
- Energy Efficiency: Implementing energy-efficient technologies in the melting and casting processes can significantly reduce the energy footprint of Spheroidal Graphite Cast Iron production. This includes using electric arc furnaces or induction furnaces that are more energy-efficient.
- Emission Control Systems: Employing advanced emission control systems in foundries, such as baghouses and scrubbers, can mitigate air pollution. These systems capture particulates and treat gases before they are released into the atmosphere.
- Recycling Practices: Spheroidal Graphite Cast Iron is highly recyclable, and utilizing recycled material (scrap iron) in the production process reduces the demand for virgin raw materials and conserves energy. Also, recycling of foundry sand and slag minimizes waste.
- Alternative Nodulizing Agents: Research into less polluting nodulizing agents can reduce the environmental impact associated with traditional magnesium or cerium-based processes.
- Life Cycle Analysis (LCA): Conducting LCA of Spheroidal Graphite Cast Iron products helps in understanding and minimizing the environmental impact throughout the product’s lifecycle, from raw material extraction to end-of-life recycling.
- Regulatory Compliance and Best Practices: Adhering to environmental regulations and implementing best practices in operation, such as proper waste management and reducing material wastage, enhances the sustainability of Spheroidal Graphite Cast Iron production.
Conclusion
While the production of Spheroidal Graphite Cast Iron is energy and resource-intensive and has associated environmental impacts, adopting sustainable practices and technologies can significantly mitigate these effects. The recyclability of Spheroidal Graphite Cast Iron adds to its sustainability profile, making it a viable material choice from an environmental perspective. As technology progresses, further advancements in sustainable manufacturing processes are likely to reduce the ecological impact of Spheroidal Graphite Cast Iron production even more.