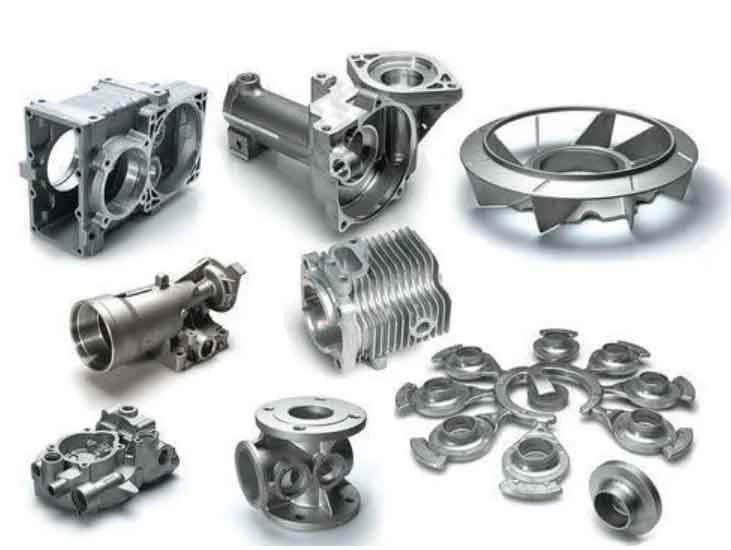
Grey cast iron, also known as gray iron, has a rich history of evolution, innovations, and advancements. Over the years, various developments have enhanced the properties and expanded the applications of grey cast iron in numerous industries. Let’s explore the key stages of its evolution and notable advancements:
- Early Development: Grey cast iron was first produced in ancient China around 600 BC. Its initial form had limited use due to its brittleness. However, the discovery of carbonizing iron in the 14th century led to the development of cast iron with improved strength and hardness.
- Introduction of Coke: In the 18th century, the widespread use of coke as a fuel in iron production revolutionized the industry. Coke reduced impurities and allowed for the production of higher-quality grey cast iron, which exhibited better strength and reduced brittleness.
- Graphite Formation: In the mid-19th century, researchers began to study the microstructure of grey cast iron more closely. They discovered that the presence of graphite in the iron matrix accounted for its unique properties. The formation and control of graphite flakes became a focal point of research to improve the material’s properties.
- Flake Control: During the late 19th and early 20th centuries, advancements in casting techniques and alloying elements facilitated better control over the formation of graphite flakes. By manipulating the cooling rate and introducing elements like silicon, the size, shape, and distribution of graphite flakes could be optimized, enhancing the material’s strength and machinability.
- Development of Nodular or Ductile Iron: In 1943, the development of nodular or ductile iron brought a significant breakthrough. This innovation involved the addition of small amounts of magnesium or cerium to molten iron, resulting in spherical graphite structures. Nodular iron exhibited improved ductility, toughness, and resistance to cracking, expanding its applications in demanding engineering sectors.
- Austempered Ductile Iron (ADI): In the 1970s, the austempering process was applied to ductile iron, leading to the creation of austempered ductile iron (ADI). Austempering involves quenching the iron at a specific temperature range, resulting in a material with exceptional strength, wear resistance, and fatigue properties. ADI found applications in automotive components, gears, and other high-strength applications.
- Compacted Graphite Iron (CGI): Compacted graphite iron, also known as vermicular graphite iron, emerged as another significant advancement in grey cast iron. By modifying the alloy composition and cooling rate during solidification, a microstructure with compacted graphite shapes was achieved. CGI combines the strength and stiffness of nodular iron with the thermal conductivity and damping properties of grey cast iron, making it suitable for engine blocks, cylinder heads, and other demanding applications.
- Improved Casting Techniques and Simulation: Advancements in casting techniques, such as advanced mold materials, improved gating systems, and computer simulations, have contributed to better control over the casting process. These developments have enhanced the quality, integrity, and dimensional accuracy of grey cast iron components, enabling their use in critical applications with higher performance requirements.
- Alloying and Surface Treatments: Ongoing research focuses on alloying grey cast iron with elements like nickel, copper, and molybdenum to improve specific properties such as corrosion resistance and high-temperature strength. Additionally, surface treatments like coatings and heat treatments provide further enhancements, enabling grey cast iron to be used in specialized applications.
- Sustainability and Recyclability: In recent years, there has been a growing emphasis on sustainability and the recyclability of materials. Grey cast iron is an inherently recyclable material, and advancements in processing technologies and foundry practices have made the recycling of grey cast iron more efficient. The use of recycled grey cast iron not only reduces the demand for raw materials but also minimizes waste and energy consumption.
- Digitalization and Industry 4.0: The integration of digitalization and Industry 4.0 concepts into the foundry industry has brought significant advancements to grey cast iron production. Technologies such as artificial intelligence, machine learning, automation, and real-time monitoring systems enable improved process control, quality assurance, and predictive maintenance. These advancements enhance productivity, optimize material usage, and further improve the properties of grey cast iron components.
- Application Expansion: Grey cast iron has seen a continuous expansion of applications due to its unique combination of properties, cost-effectiveness, and ease of manufacturing. While it has traditionally been used in applications like engine blocks, pipes, and automotive components, grey cast iron is now finding its way into emerging sectors such as renewable energy, construction, and aerospace, thanks to ongoing research and development efforts.
It is worth noting that the evolution and advancements in grey cast iron are ongoing processes, driven by the continuous pursuit of better materials, improved casting techniques, and the evolving needs of various industries. As research and technology progress, we can expect further innovations and refinements that will expand the capabilities and applications of grey cast iron.