1. Introduction
In the manufacturing process of grinders, hydraulic parts play a crucial role in ensuring the smooth operation of various functions. The most common types of hydraulic parts in grinder production, such as disc – cover, flat – plate, square, and short – cylinder ones, possess simple outer structures. However, they are characterized by large cross – sectional thicknesses, high – level technical requirements, and a relatively high foundry reject rate, which typically ranges from 30% to 40%. This high reject rate not only leads to significant economic losses for enterprises but also affects production efficiency and product quality. Therefore, it is of great importance to explore and optimize the foundry technology of these hydraulic parts. This article will delve into the specific foundry techniques for different types of hydraulic parts, as well as methods to ensure material properties and improve the overall quality of castings.
1.1 The Significance of Hydraulic Parts in Grinder Production
Hydraulic systems are the “muscles” of grinders, enabling precise control of movements like the reciprocating motion of the worktable, the transverse feed motion of the grinding wheel, and the automatic clamping of workpieces. Hydraulic parts, as the core components of these systems, directly determine the performance and reliability of the grinder. For example, in the internal – circular grinder produced by Zhengzhou No.2 Machine Tool Factory, a large number of hydraulic parts are used to achieve various actions. Any defect in these hydraulic parts can lead to abnormal operation of the grinder, affecting the machining accuracy and surface quality of the workpiece.
1.2 Challenges in the Foundry of Hydraulic Parts
The main challenges in the foundry of hydraulic parts are their thick cross – sections and strict quality requirements. The thick cross – sections make it difficult to ensure uniform cooling during the casting process, which may result in shrinkage cavities, porosity, and other defects. Moreover, the high – strength, high – density, and certain hardness requirements, along with the prohibition of any casting defects such as pores and slag inclusions, pose great difficulties to the foundry process. Traditional casting processes often cannot meet these requirements, leading to a high reject rate.
2. Foundry Technology for Disc – Cover – Type Hydraulic Parts
Disc – cover – type hydraulic parts include end covers of various hydraulic cylinders, end covers of valve bodies, and cover plates. These parts usually have a small outer size but a large thickness, and they are designed with numerous mechanical – processing surfaces, oil – passing holes, and installation holes. During the casting process, it is necessary to consider the feeding problem to ensure the integrity of the casting. Additionally, due to the small size of the parts, the metal liquid cools quickly after pouring, and slag is likely to be trapped in the casting, resulting in “slag eyes” and causing the casting to be scrapped.
2.1 Application of Centrifugal Slag – Collecting Ladle
To solve the problems of slag removal and feeding in the production of disc – cover – type hydraulic parts, the centrifugal slag – collecting ladle is applied in the casting system design. This ladle can not only effectively remove slag but also play a role in feeding, which greatly improves the yield and quality of castings.
2.1.1 Case Study: The Connecting Disc Casting
The connecting disc is a key component of the feed hydraulic cylinder of the M224 semi – automatic internal – circular grinder. The casting details are shown in Table 1.
Casting Name | Connecting Disc |
---|---|
Weight | 7.9 kg |
Outline Dimensions | φ180mm×45mm |
Material | HT200 |
Maximum Thickness | 42mm |
Quality Requirements | Dense structure, no pores, slag eyes, or shrinkage cavities |
The original casting process used the green sand wet – mold casting method, with the process features of “using pouring instead of risering”, two castings in one mold, and sharing a sprue (also serving as a riser). However, this process led to a high reject rate of 35% due to slag – eye defects.
The improved casting process is illustrated in Figure 1. Two castings share one pouring system. The original sprue is replaced by a centrifugal slag – collecting ladle. The parameters of the slag – collecting ladle are designed according to the hot – spot circle diameter of the casting, with a size of φ72mm×85mm. A sprue is added at an appropriate position on the upper mold and connected tangentially to the slag – collecting ladle through a runner. The sprue and the slag – collecting ladle have a center – to – center distance of 90mm. The internal gate, which also serves as a riser neck, has a minimum cross – section size that can ensure the feeding channel is not cut off prematurely. The internal gate is approximately tangentially connected to the slag – collecting ladle, but the rotation direction of the metal liquid in it is opposite to that in the slag – collecting ladle. A large – proportion gate is selected to quickly fill the slag – collecting ladle and reduce the risk of slag being sucked into the cavity. The area ratios of the gates are \(F_{直}:F_{板}:F_{内}=1.85:1.5:1\), with \(F_{内}=2.24 cm^{2}\), \(F_=6.72 cm^{2}\), and \(F_{在}=8.33 cm^{2}\) (φ32mm). After production verification, the improved process shows excellent performance, with a reject rate of less than 4%.
2.1.2 Case Study: The Clamping Hydraulic Cylinder Casting
The clamping hydraulic cylinder casting of the M224 internal – circular grinder is a composite casting with the functions of a pulley and a hydraulic cylinder. The casting details are presented in Table 2.
Casting Name | Clamping Hydraulic Cylinder |
---|---|
Outline Dimensions | φ186mm×120mm |
Weight | 11.5 kg |
Material | HT200 |
Maximum Hot – Spot Diameter | 50mm |
Quality Requirements | Dense structure, no pores, slag eyes, or shrinkage cavities |
The original process used the dry – sand mold casting method with a bead – edge gate, “using pouring instead of risering”, and two castings in one mold sharing a sprue (also serving as a riser). In this process, the metal liquid in the sprue flowed turbulently, and slag was easily rolled into the cavity, resulting in “slag eyes”. In addition, the metal liquid was prone to splashing and forming “iron beans”, with a high comprehensive reject rate of about 30%.
Based on the balanced solidification theory and combined with the design of the centrifugal slag – collecting ladle, the optimized process is shown in Figure 2. The castings are located in the lower mold, with two castings in one mold. A slag – collecting ladle (also serving as an insurance riser) with a size of φ65mm×90mm is set in the middle of the two castings. A sprue is added and connected tangentially to the slag – collecting ladle through a runner. A flash gate with a size of 65mm×6mm and a length of about 10mm is used to introduce the casting. The cross – sectional areas of the gates are \(F_{内}=3.9 cm^{2}\), \(F_{镇}=11.7 cm^{2}\), and \(F_{直}=14.4 cm^{2}\). After applying the optimized process, the metal liquid flows smoothly during pouring, the slag – collecting ladle has good slag – removing performance, and the comprehensive reject rate is reduced to 3%.
3. Foundry Technology for Flat – Plate – Type Hydraulic Parts
Flat – plate – type hydraulic parts include distribution plates and cover plates in the oil – supply and distribution systems of various internal – circular grinders. All surfaces of these parts are mechanical – processing surfaces, and the two large planes are the most critical, with many oil grooves, oil – passing holes, and installation holes. These parts require a dense structure and are not allowed to have any casting defects such as pores and slag eyes.
3.1 The “Horizontal Casting and Vertical Casting” Process
Previously, when the large planes were cast horizontally or obliquely, the reject rate was as high as 30% – 40%, mainly due to pores, slag eyes, or sand – inclusion defects. By adopting the “horizontal casting and vertical casting” dry – mold process, the two large planes are placed on the side of the casting position, which makes it easier to ensure their quality.
3.1.1 Case Study: The Distribution Plate of the M224 Semi – Automatic Internal – Circular Grinder
The distribution plate of the M224 semi – automatic internal – circular grinder is a key part of the oil – supply and distribution system. The casting details are shown in Table 3.
Casting Name | Distribution Plate |
---|---|
Material | HT200 |
Blank Weight | 48 kg |
Outline Dimensions | 596mm×312mm×34mm |
Quality Requirements | Dense structure, no pores, slag eyes, or shrinkage cavities. The surface roughness of the two large planes is \(R a = 0.8\mu m\) |
The casting process of the distribution plate is shown in Figure 3. It uses clay sand and dry – mold casting, with two castings in one mold and the “horizontal casting and vertical casting” process. The machining allowances for the side and bottom surfaces are 6mm, and for the top surface (casting position) is 10mm. The pouring system is set in the middle of the two castings, in the form of a stepped gate, with \(F_{内}=3.6cm\) and \(F_{衣}=8.6 cm^{2}\). A riser is set in the middle of the top surface of the cavity, with a size of 200mm×70mm×70mm, which is beneficial for feeding, exhaust, and slag collection. The chemical composition is \(w_{C}=3.35\%\), \(w_{Si}=1.7\%\), \(w_{Mn}=0.85\%\), \(w_{S}=0.1\%\), \(w_{P}=0.1\%\). Since the implementation of this process, the effect has been remarkable, and the reject rate is basically controlled within 3%.
4. Foundry Technology for Square and Short – Cylinder – Type Hydraulic Parts
Square and short – cylinder – type hydraulic parts are mainly various control – valve bodies in grinders, such as reciprocating control boxes, feed control boxes, dual – pressure relief valves, stroke valves, and switch valves. These parts have simple outer shapes, and all outer surfaces need to be machined. They are usually designed with valve holes, oil – passing holes, oil grooves, and installation holes. The processing of valve holes is complex and has high technical requirements.
4.1 The “One Billet and Many Pieces Continuous Casting” and “Horizontal Casting and Vertical Casting” Processes
When casting these parts one by one, there are many pore and slag – hole defects on the upper surface of the casting position, resulting in a high reject rate of about 35% – 40%. In addition, due to the large cross – section, it is necessary to set risers for feeding, which leads to a low process yield. By using the “one – billet – multiple – pieces continuous casting” and “horizontal casting and vertical casting” processes, significant results can be achieved.
4.1.1 Case Study: The Reciprocating Control Box Casting
The reciprocating control box casting is made of HT300. The casting details are presented in Table 4.
Casting Name | Reciprocating Control Box |
---|---|
Material | HT300 |
Number of Valve Holes | 5 |
Number of Oil – Passing Holes and Installation Holes | Dozens |
Surface Roughness of Valve Holes | \(R a=0.4\mu m\) |
Cylindricity Error of Valve Holes | 0.005mm |
Hardness Requirement | > 170HBW |
Blank Outline Dimensions | 148mm×150mm×108mm |
Weight | 19 kg |
Quality Requirements | No slag eyes, sand eyes, or pores |
The continuous – casting and vertical – casting process for the reciprocating control box is shown in Figure 4. Four castings are continuously cast from one billet, with a blank size of 108mm×810mm×150mm. The 604 – mm part is the casting, and the upper 206 – mm part is the riser. After the casting is formed, the 604 – mm part is cut into 4 pieces with a length of 148mm on a sawing machine, and the remaining part is used as the riser for remelting. The weight of a single billet is 99.7 kg (including the riser part). Two billets are cast in one mold, using the “horizontal casting and vertical casting” process. The mold is set up, dried, assembled, and tightened, and then the sand mold is stood up for pouring. A gate is set in the middle of the two cavities, in the form of a stepped gate, which can ensure smooth filling of the metal liquid and good feeding effect with the highest metal – liquid temperature in the riser part. At the same time, during vertical casting, the slag and pores in the metal liquid will float to the top of the cavity under the action of buoyancy. After the casting is formed, the top part (riser) is cut off, ensuring the quality of the casting. The vertical casting also makes the metal – liquid pressure in the cavity larger, resulting in a denser structure after solidification. The chemical composition of the iron liquid is \(w_{C}=3.10\%\), \(w_{Si}=1.4\%\), \(w_{Mn}=1.2\%\), \(w_{S}=0.1\%\), \(w_{P}=0.1\%\). The furnace – front control is carried out by using a triangular test piece, with a white – mouth of 10 – 12mm. The process has a good effect, with a process yield of 80.5% and a reject rate within 4%.
5. Ensuring the Material Properties of Hydraulic Parts
5.1 Chemical Composition Control
According to the performance requirements and wall – thickness conditions of the castings, it is necessary to select appropriate chemical compositions, accurately calculate the furnace – charge ratio, and strictly control the quality of raw materials to ensure the stability of the composition. Different materials have different performance requirements, and the chemical composition needs to be adjusted accordingly. For example, for HT200 and HT300 materials, the carbon, silicon, manganese, sulfur, and phosphorus contents need to be precisely controlled within a certain range to meet the requirements of strength, hardness, and density. Table 5 shows the typical chemical – composition ranges for some common casting materials.
Material | \(w_{C}\) | \(w_{Si}\) | \(w_{Mn}\) | \(w_{S}\) | \(w_{P}\) |
---|---|---|---|---|---|
HT200 | 3.1 – 3.4% | 1.5 – 2.0% | 0.6 – 0.9% | ≤0.12% | ≤0.15% |
HT300 | 2.9 – 3.2% | 1.2 – 1.7% | 0.8 – 1.2% | ≤0.10% | ≤0.12% |
5.2 Cooling – Rate Control
In the casting production process, it is necessary to strictly control the key factors and links that affect the cooling rate of castings. For small – sized hydraulic parts, when arranging multiple castings in one sand box or placing sand molds of the same – grade castings together for convenience of pouring, it is necessary to consider the cooling situation of the castings. Since it is not appropriate to directly compare the wall – thickness values of different geometric parts, the concept of modulus is introduced. By calculating and comparing the moduli of various geometric bodies, when the moduli of the same – grade castings are the same or similar, they can be arranged in the same sand box or their sand molds can be placed together. This not only facilitates production organization but also ensures the material – property requirements of the castings. Table 6 shows the modulus – calculation formulas for several common geometric bodies.
Geometric Body | Modulus Calculation Formula |
---|---|
Plate – like Part | \(M = T/2\) |
Rectangular – Section Rod – like Part | \(M=\frac{ab}{2(a + b)}\) |
Short Cylinder (\(h\leq2.5D\)) | \(M=\frac{rh}{2(r + h)}\) |
Long Cylinder (\(h>2.5D\)) | \(M = D/4\) |
Hollow Ring (\(b<5a\)) | \(M=\frac{ab}{2(a + b)}\) |
Hollow Tube (\(b>5a\)) | \(M = a/2\) |
6. Conclusion
The foundry technology of common hydraulic parts in grinder production is a complex and systematic project. By using specific casting techniques for different types of hydraulic parts, such as the centrifugal slag – collecting ladle for disc – cover – type parts, the “horizontal casting and vertical casting” process for flat – plate – type parts, and the combination of “one – billet – multiple – pieces continuous casting” and “horizontal casting and vertical casting” for square and short – cylinder – type parts, significant improvements in casting quality can be achieved. These techniques address the key issues in the casting process, like slag removal, feeding, and ensuring the quality of critical surfaces, effectively reducing the reject rate and increasing the process yield.
In addition, controlling the chemical composition and cooling rate of the castings is essential for ensuring the material properties of hydraulic parts. Precise control of chemical composition can meet the requirements for strength, hardness, and density, while the proper management of the cooling rate through the concept of modulus helps to avoid defects caused by uneven cooling.
In summary, the optimized foundry technologies for hydraulic parts not only contribute to the improvement of product quality and production efficiency in grinder manufacturing but also have economic and environmental benefits. By reducing waste and rework, enterprises can save costs and resources, making the production process more sustainable. Future research can focus on further optimizing these processes, exploring new materials and casting technologies, and integrating advanced control systems to achieve even higher – quality hydraulic parts for the development of the grinder industry.
7. Future Research Directions
7.1 Advanced Casting Materials
As technology advances, there is a growing interest in exploring new casting materials for hydraulic parts. For example, high – performance alloys with enhanced wear – resistance, corrosion – resistance, and mechanical properties could be investigated. These new materials might offer better performance in harsh working conditions, extending the service life of hydraulic parts and reducing maintenance costs. Research could focus on the casting behavior of these materials, including their fluidity, solidification characteristics, and compatibility with existing casting processes.
7.2 Integration of Simulation Technology
Casting process simulation can play a crucial role in optimizing the foundry technology. By using software to simulate the filling, solidification, and cooling processes of castings, potential defects can be predicted in advance. This allows for adjustments to the casting process parameters, such as gating system design, pouring temperature, and cooling rate, without the need for costly physical trials. Future research could aim to improve the accuracy of these simulations by considering more complex factors, like the interaction between the mold material and the molten metal, and integrating real – time monitoring data to further refine the simulation models.
7.3 Automation and Intelligent Control in Casting
Automation and intelligent control systems can enhance the consistency and quality of casting production. Robotic pouring systems can ensure accurate and repeatable pouring, reducing the impact of human error. Intelligent temperature – control systems can precisely regulate the cooling rate of castings based on real – time temperature data. Research in this area could involve the development of more advanced control algorithms, the integration of sensors for real – time monitoring, and the optimization of automated production lines for hydraulic part casting.
8. Comparison with Other Manufacturing Processes for Hydraulic Parts
8.1 Forging vs. Casting
Forging is another common manufacturing process for producing hydraulic parts. While forging can result in parts with high mechanical strength and a more refined grain structure, it is generally more expensive and less suitable for complex – shaped parts. Casting, on the other hand, can easily produce parts with complex geometries, as demonstrated by the various hydraulic parts discussed in this article. Table 7 provides a comparison of the characteristics of forging and casting for hydraulic part production.
Comparison Items | Forging | Casting |
---|---|---|
Mechanical Properties | High strength, refined grain structure | Varies depending on casting process and material, but can meet requirements for hydraulic parts |
Geometric Complexity | Limited to relatively simple shapes | Can produce complex geometries easily |
Cost | Higher, especially for small – batch production | Lower for large – batch production, but reject rate can increase costs |
Production Efficiency | Lower for complex parts | Higher for parts with complex shapes in large – batch production |
8.2 Machining – Based Manufacturing vs. Casting
Machining – based manufacturing processes, such as CNC machining, can achieve high – precision parts. However, they often require more machining time and material waste compared to casting. Casting can produce near – net – shape parts, reducing the amount of machining required. For hydraulic parts with many holes and grooves, casting can significantly reduce the manufacturing time and cost if the casting quality is well – controlled. Table 8 compares machining – based manufacturing and casting for hydraulic part production.
Comparison Items | Machining – Based Manufacturing | Casting |
---|---|---|
Precision | High, can achieve very tight tolerances | Depends on casting process, but can meet most hydraulic part requirements with proper control |
Machining Time | Long, especially for complex parts | Short for casting process, but may require additional finishing |
Material Waste | High, as material is removed during machining | Relatively low for near – net – shape casting |
Cost for High – Volume Production | Higher due to long machining time | Lower for large – batch production |
9. Case Studies of Successful Implementations in the Industry
9.1 Company A: Upgrading Casting Technology for Disc – Cover – Type Hydraulic Parts
Company A, a major grinder manufacturer, was facing a high reject rate of 30% for disc – cover – type hydraulic parts. After implementing the centrifugal slag – collecting ladle technology as described in this article, they saw a significant improvement. The reject rate dropped to less than 5%, and the process yield increased by 15%. This not only reduced production costs but also improved the overall quality of their grinders, leading to higher customer satisfaction.
9.2 Company B: Applying “Horizontal Casting and Vertical Casting” for Flat – Plate – Type Hydraulic Parts
Company B was struggling with the production of flat – plate – type hydraulic parts, with a reject rate of up to 40% due to defects in the large planes. By adopting the “horizontal casting and vertical casting” process, they were able to reduce the reject rate to within 3%. The improved quality of the flat – plate parts also enhanced the performance of their grinders’ oil – supply and distribution systems, resulting in more stable and efficient operation.
10. Impact of Casting Technology on the Grinder Industry
The optimized casting technologies for hydraulic parts have a far – reaching impact on the grinder industry. Firstly, the improvement in casting quality directly enhances the performance and reliability of grinders. Hydraulic parts with fewer defects ensure more precise control of movements, leading to better machining accuracy and surface finish of workpieces. This, in turn, improves the competitiveness of grinder manufacturers in the market.
Secondly, the reduction in the reject rate and increase in process yield contribute to cost – savings. Manufacturers can produce more high – quality parts with the same amount of raw materials and resources, reducing waste and production costs. This cost – effectiveness allows companies to invest more in research and development, further promoting the innovation and development of the grinder industry.
Finally, the development of advanced casting technologies for hydraulic parts also drives the progress of related industries, such as the foundry industry and the mold – making industry. It encourages the improvement of equipment, materials, and manufacturing processes in these industries, creating a positive cycle of development for the entire manufacturing ecosystem.
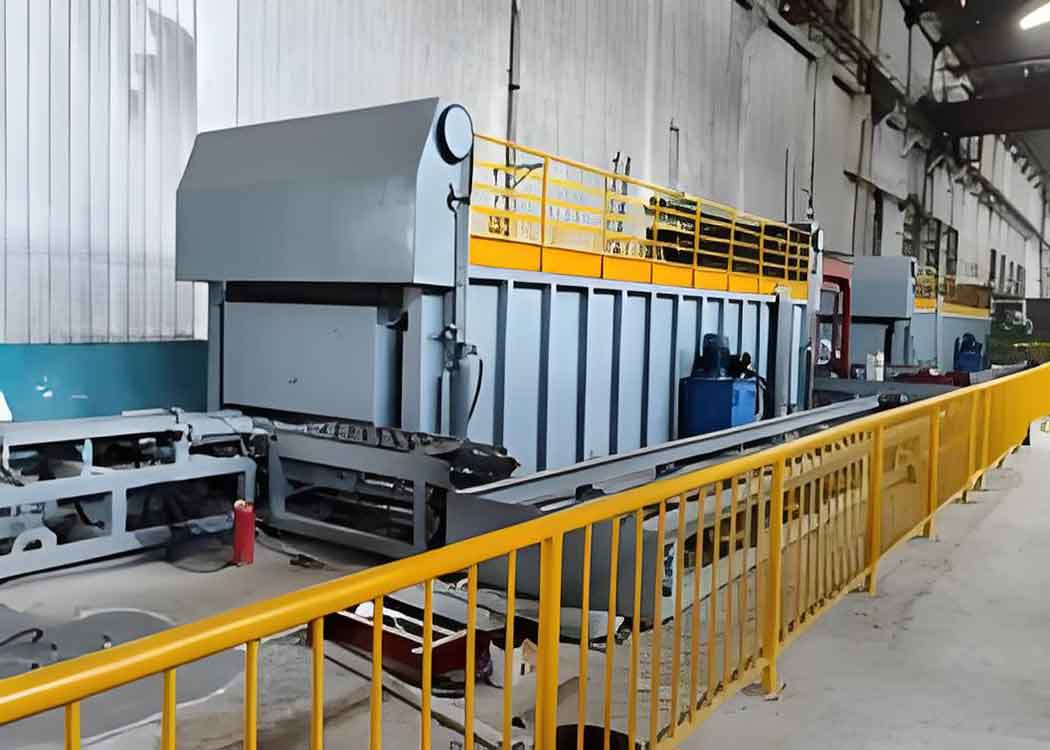