Quality control is a critical aspect of steel casting production, ensuring the consistency, integrity, and reliability of the final components. This article highlights the significance of quality control in steel casting processes, emphasizing its role in maintaining high standards, meeting specifications, and delivering superior products to various industries.
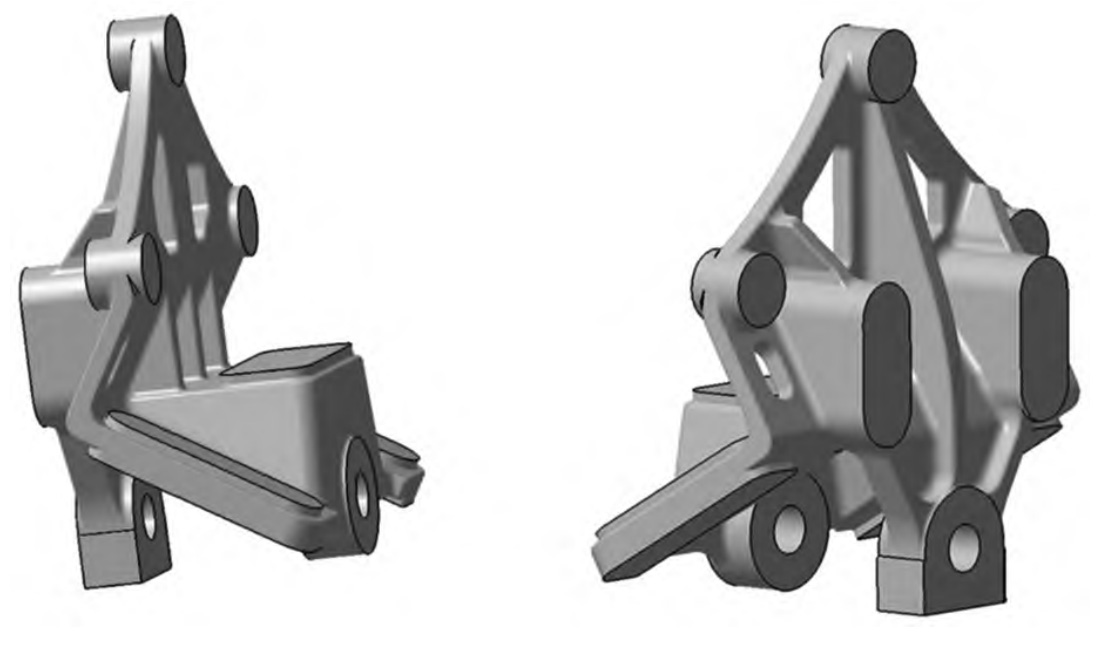
- Consistency and Uniformity: Quality control measures in steel casting help achieve consistent and uniform results throughout the production process. By implementing strict control procedures, manufacturers can ensure that each casting meets specified requirements in terms of dimensions, material properties, and surface finish. Consistency in casting quality leads to reliable and predictable performance of the final components.
- Metallurgical Analysis and Material Integrity: Quality control involves thorough metallurgical analysis of steel castings to assess the material’s integrity. Techniques such as chemical analysis, mechanical testing, and microstructural examination help verify the composition, mechanical properties, and overall quality of the casted steel. This analysis ensures that the material meets the specified standards and provides the desired performance characteristics.
- Non-Destructive Testing: Non-destructive testing (NDT) methods play a crucial role in quality control for steel castings. Techniques such as ultrasonic testing, magnetic particle inspection, and radiographic examination are employed to detect internal and surface defects without damaging the castings. NDT ensures the integrity of the castings, identifies potential flaws, and helps prevent component failures during service.
- Dimensional Inspection and Tolerance Control: Accurate dimensional inspection is essential in steel casting to ensure that the final components meet the required specifications. Precision measuring instruments and techniques, such as coordinate measuring machines (CMM) and optical measurement systems, are used to verify dimensional accuracy, tolerances, and geometrical features. Proper dimensional inspection ensures the proper fit and function of the cast components in their intended applications.
- Quality Management Systems: Implementing robust quality management systems (QMS) is vital in steel casting operations. Quality control processes, documentation, and standard operating procedures are established to ensure consistency, traceability, and continuous improvement. QMS frameworks such as ISO 9001 provide a structured approach to quality control, emphasizing process control, customer satisfaction, and adherence to international quality standards.
- Compliance with Industry Standards and Regulations: Steel castings must meet industry-specific standards and regulations to ensure safety, reliability, and compatibility with various applications. Quality control in steel casting ensures compliance with these standards, such as ASTM, ASME, or customer-specific requirements. Adhering to industry standards guarantees the performance and reliability of the castings in demanding environments.
Quality control is paramount in steel casting to ensure the consistency, integrity, and reliability of the final components. By implementing stringent control measures, conducting metallurgical analysis, performing non-destructive testing, and maintaining precise dimensional inspection, manufacturers can deliver high-quality castings that meet customer specifications and industry standards. Effective quality control processes instill confidence in the performance and durability of steel castings, enabling their successful application in industries such as automotive, aerospace, construction, and energy.