Lost Foam Casting has been steadily rising in popularity and is revolutionizing metal casting processes across various industries. This innovative casting technique offers numerous advantages over traditional methods, paving the way for improved efficiency, cost-effectiveness, and design flexibility.
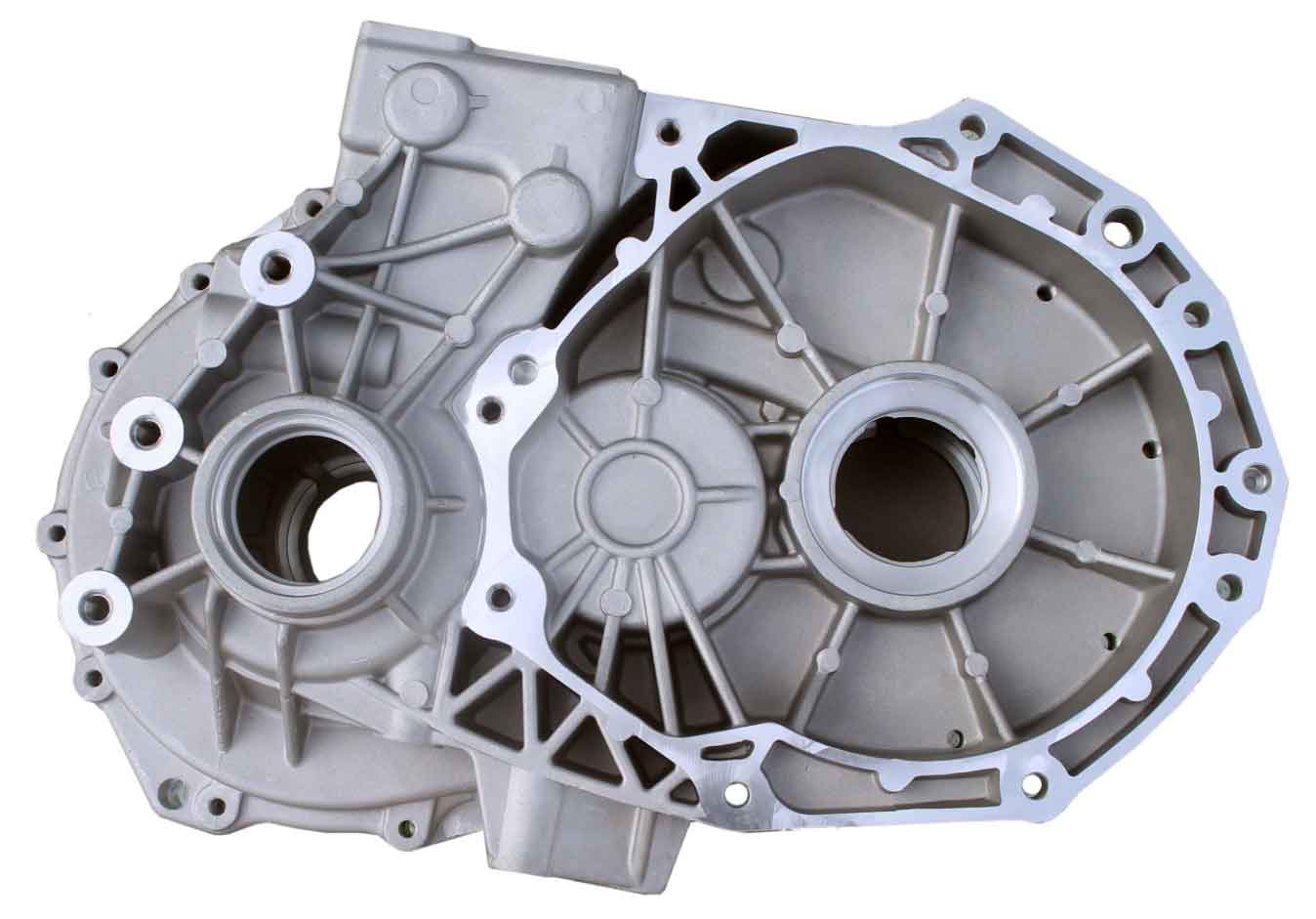
One of the key reasons behind the rise of Lost Foam Casting is its ability to produce complex and intricate metal components with exceptional precision. Traditional casting methods often struggle to achieve intricate designs and intricate internal structures, limiting the possibilities for product design. However, Lost Foam Casting overcomes these limitations by utilizing foam patterns that can be easily shaped and manipulated. This allows for the creation of intricate and delicate features that were once challenging to achieve.
Another significant advantage of Lost Foam Casting is its ability to eliminate the need for complex cores and parting lines. In traditional casting processes, cores and parting lines are often required to create complex shapes and internal cavities. These additional components add complexity, cost, and time to the casting process. However, Lost Foam Casting eliminates the need for cores and parting lines altogether. The foam pattern used in the process acts as both the pattern and the core, resulting in a seamless casting with a smooth surface finish.
Lost Foam Casting also offers substantial time and cost savings. The simplified process of using foam patterns reduces the time required for pattern-making and assembly. It eliminates the need for multiple patterns and cores, thereby reducing material costs and streamlining production. Additionally, the absence of parting lines and cores reduces the risk of casting defects, resulting in improved quality control.
Design flexibility is another area where Lost Foam Casting shines. With traditional casting methods, intricate designs and complex shapes often require multiple molds, cores, and assembly processes. Lost Foam Casting, on the other hand, allows for the creation of complex geometries and internal structures in a single mold. This opens up new possibilities for product design and innovation, enabling manufacturers to create unique and customized components with ease.
Furthermore, Lost Foam Casting is an environmentally friendly casting process. The foam patterns used in the process are made from recyclable materials, reducing waste and promoting sustainability. The evaporative nature of the foam patterns eliminates the need for pattern disposal, minimizing the environmental impact associated with traditional pattern-making processes.
As a result of these advantages, Lost Foam Casting is gaining traction in industries such as automotive, aerospace, and industrial manufacturing. It is revolutionizing metal casting processes by offering enhanced design capabilities, cost savings, and improved overall efficiency. Manufacturers are increasingly recognizing the potential of Lost Foam Casting to optimize their production processes and stay ahead in today’s competitive market.
In conclusion, the rise of Lost Foam Casting is transforming metal casting processes. With its ability to create complex designs, eliminate the need for cores and parting lines, reduce costs and production time, and provide design flexibility, Lost Foam Casting is revolutionizing the way metal components are manufactured. As the demand for intricate and customized metal parts continues to grow, Lost Foam Casting is poised to play a crucial role in the future of metal casting.