The casting industry, a cornerstone of manufacturing, is experiencing a significant transformation due to the adoption of automation. This technological shift is reshaping how products are designed, produced, and inspected, offering numerous benefits while also presenting unique challenges. This article explores the critical role of automation in modern casting products manufacturers, highlighting its impact on efficiency, quality, and sustainability.
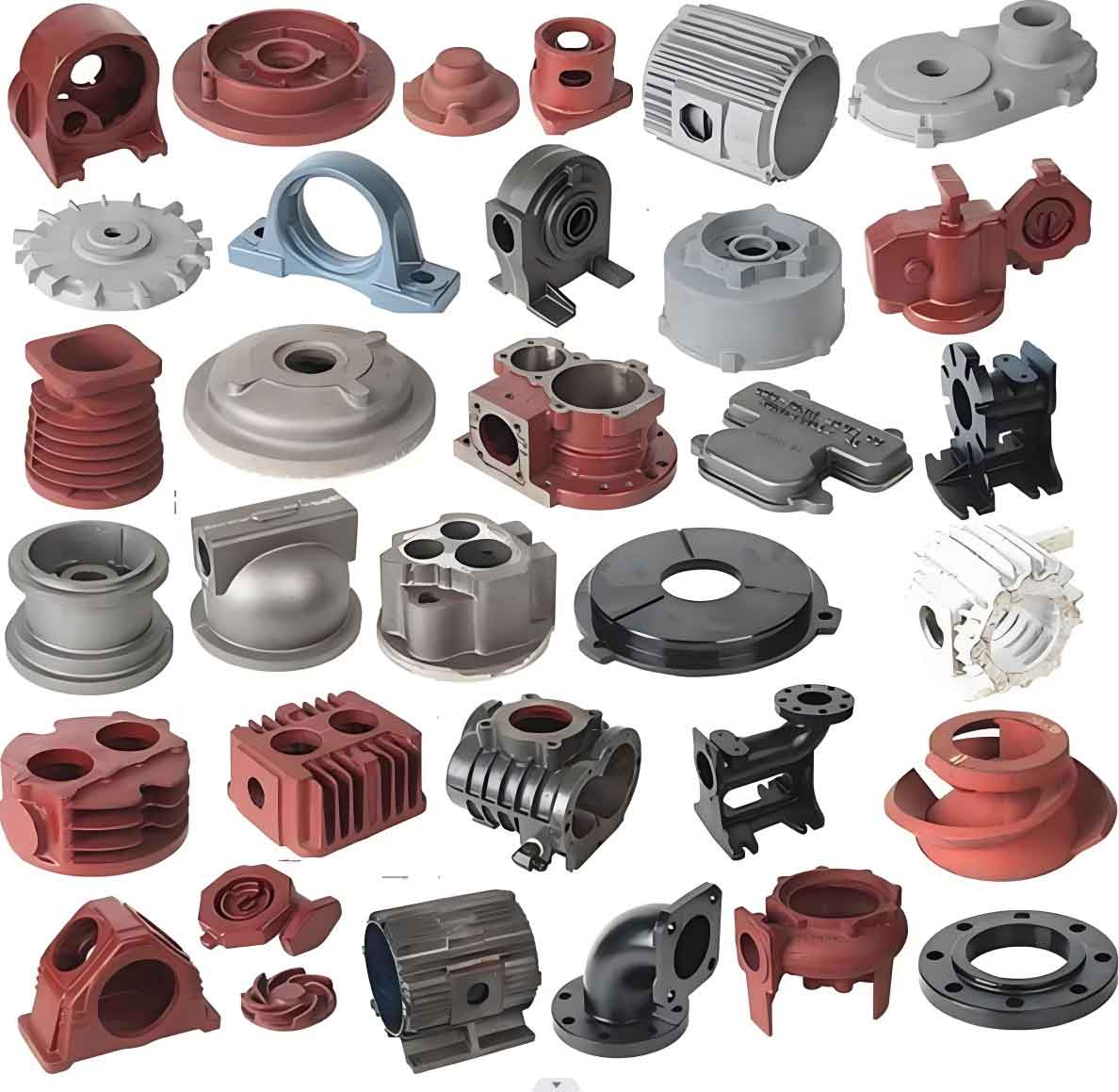
Introduction
Automation in casting products manufacturers involves the use of advanced technologies such as robotics, artificial intelligence (AI), and machine learning (ML) to streamline production processes. These technologies are not only enhancing productivity but also improving the precision and quality of cast components. As the industry evolves, automation is becoming indispensable for manufacturers striving to remain competitive in a global market.
Benefits of Automation in Casting Products Manufacturers
- Increased Efficiency:
- Reduced Cycle Times: Automation significantly reduces the time required to complete each casting cycle, allowing manufacturers to produce more parts in less time.
- Continuous Operation: Automated systems can operate 24/7, increasing overall production capacity and minimizing downtime.
- Enhanced Precision and Quality:
- Consistent Quality: Automated processes ensure that each component is produced to the same high standards, reducing variability and defects.
- Complex Geometries: Advanced automation allows for the production of parts with intricate designs and tight tolerances that would be challenging to achieve manually.
- Cost Savings:
- Labor Costs: By automating repetitive and labor-intensive tasks, manufacturers can reduce labor costs and allocate human resources to more strategic activities.
- Material Efficiency: Automation minimizes material waste by optimizing the use of raw materials and reducing scrap rates.
- Improved Safety:
- Hazardous Tasks: Robots and automated systems can perform dangerous tasks, reducing the risk of injury to workers and improving overall workplace safety.
- Ergonomics: Automation reduces the physical strain on workers by handling heavy lifting and repetitive motions.
- Data-Driven Decision Making:
- Real-Time Monitoring: Automated systems equipped with sensors and IoT devices provide real-time data on production processes, enabling quick adjustments and proactive maintenance.
- Predictive Analytics: AI and ML can analyze data to predict equipment failures and optimize maintenance schedules, reducing downtime and extending the lifespan of machinery.
Challenges of Implementing Automation
- High Initial Investment:
- Capital Costs: The upfront cost of purchasing and installing automated systems can be substantial, making it a significant investment for manufacturers.
- Training: Employees need to be trained to operate and maintain automated systems, which requires time and resources.
- Integration with Existing Systems:
- Compatibility: Integrating new automated systems with existing infrastructure can be complex and may require significant modifications.
- Downtime: The integration process can lead to temporary production stoppages, affecting overall output.
- Cybersecurity Risks:
- Data Security: As manufacturing processes become more digital, the risk of cyber-attacks increases. Protecting sensitive production data and ensuring system integrity are critical concerns.
- System Vulnerabilities: Automated systems must be safeguarded against potential cyber threats, requiring robust cybersecurity measures.
- Maintenance and Upkeep:
- Technical Expertise: Automated systems require regular maintenance and updates, necessitating a skilled technical workforce.
- Spare Parts: Ensuring the availability of spare parts and support services is essential for minimizing downtime due to system failures.
Table: Comparison of Manual vs. Automated Casting Processes
Aspect | Manual Casting Process | Automated Casting Process |
---|---|---|
Efficiency | Lower due to manual intervention | Higher with continuous operation |
Quality Consistency | Variable, dependent on human skill | Consistent, driven by precise control |
Production Speed | Slower, limited by human capacity | Faster, capable of 24/7 operation |
Labor Costs | Higher, due to intensive labor needs | Lower, with reduced manual labor |
Safety | Risk of injury from hazardous tasks | Improved, with robots handling dangerous jobs |
Complexity Handling | Limited by manual capabilities | Advanced, capable of intricate designs |
Material Waste | Higher, with potential for human error | Lower, optimized by automation |
Data Utilization | Minimal, limited to manual records | Extensive, with real-time monitoring and analytics |
Case Studies of Automation in Casting Manufacturing
- Company A: Robotics in Mold Handling:
- Process: Company A implemented robotic systems for handling molds, which significantly reduced the cycle time and improved the precision of mold placement.
- Outcome: This automation led to a 30% increase in production capacity and a 20% reduction in defects, enhancing overall efficiency and product quality.
- Company B: AI-Driven Quality Control:
- Process: Company B integrated AI-powered inspection systems to identify defects in real-time. The system uses machine learning algorithms to detect anomalies that are often missed by human inspectors.
- Outcome: The implementation resulted in a 40% reduction in defective products and a substantial improvement in customer satisfaction due to the consistent quality of the cast components.
- Company C: Automated Pouring Systems:
- Process: Company C adopted automated pouring systems to ensure precise control over the pouring process, reducing spillage and material waste.
- Outcome: The automated system improved material utilization by 15% and decreased the need for rework, leading to significant cost savings.
Future Trends in Automation for Casting Manufacturers
- Integration of IoT and Smart Manufacturing:
- Connected Systems: The use of IoT devices in casting operations will enhance connectivity and data sharing across the production floor, enabling smarter decision-making.
- Digital Twins: Creating digital twins of casting processes will allow manufacturers to simulate and optimize production workflows before implementation, reducing trial and error.
- Advancements in Robotics:
- Collaborative Robots (Cobots): Cobots will work alongside human operators, combining the precision of automation with the flexibility of manual labor, improving overall productivity.
- Mobile Robotics: Mobile robots will transport materials and components across the factory floor, streamlining logistics and reducing manual handling.
- AI and Machine Learning:
- Predictive Maintenance: AI-driven predictive maintenance will become more sophisticated, minimizing unexpected downtime and optimizing equipment performance.
- Process Optimization: Machine learning algorithms will continuously analyze production data to identify areas for improvement, driving efficiency and reducing waste.
- Sustainability and Green Manufacturing:
- Energy Management Systems: Automated systems will monitor and optimize energy usage, reducing the environmental footprint of casting operations.
- Recycling and Waste Reduction: Automation will enhance recycling processes, ensuring that materials are reused efficiently and waste is minimized.
Conclusion
The role of automation in modern casting product manufacturers is pivotal in enhancing efficiency, quality, and sustainability. While the adoption of automation presents challenges such as high initial investment and cybersecurity risks, the benefits far outweigh these obstacles. Increased production efficiency, improved product quality, cost savings, and enhanced safety are just a few of the advantages that automation brings to the casting industry.
As the industry continues to evolve, the integration of advanced technologies such as AI, robotics, and IoT will further revolutionize casting manufacturing. Embracing these advancements will enable manufacturers to stay competitive, meet the growing demand for high-quality cast components, and achieve sustainable production goals. The future of casting product manufacturing is undoubtedly intertwined with the continued advancement and adoption of automation technologies.