Gate valve bodies are integral components of fluid flow control systems. They are designed to regulate or isolate the flow of liquids and gases in various industrial applications, including water and wastewater treatment, power generation, chemical processing, and oil and gas production. This article discusses the principles of gate valve operation and their applications.
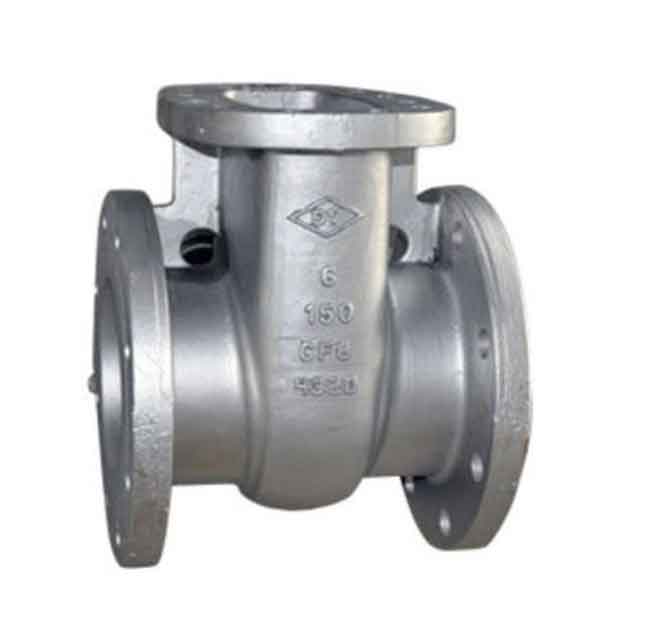
1.Principles of Gate Valve Operation
A gate valve operates by controlling the position of a wedge-shaped disk or gate within a body that has inlet and outlet ports. The disk is usually moved up and down through a linear motion, which can be guided by screws, gears, or hydraulic or pneumatic actuators. When the gate is fully open, it provides an unobstructed flow path with minimal pressure drop. When the gate is fully closed, it blocks the flow and provides a tight seal.
Gate valves can function as on-off valves for isolating sections of a pipeline or regulating valves for modulating fluid flow. They are classified into different types based on their disk or gate configuration, such as solid-wedge, flexible wedge, double-disk, and knife gate valves. Each type offers unique advantages and disadvantages in terms of sealing, flow control, pressure drop, and maintenance.
2.Applications of Gate Valve Bodies
Gate valves are used in various industrial and commercial applications that require fluid flow control. Some common applications include:
a. Water and wastewater treatment: Gate valves are commonly used for isolating or regulating the flow of water and other liquids in treatment plants, distribution systems, and storage reservoirs.
b. Power generation: Gate valves are essential for controlling the flow of steam, water, and coolant in power plants operating on fossil fuels, nuclear energy, or renewable sources like hydropower and geothermal energy.
c. Chemical processing: Gate valves are used for handling and controlling the flow of corrosive, toxic, or hazardous chemicals in various stages of chemical production, storage, and disposal. They must be made of materials resistant to chemical attack and suitable for high temperatures and pressures.
d. Oil and gas: Gate valves are vital components of pipelines, storage tanks, and processing facilities for transporting and refining crude oil and natural gas. They must withstand high pressures, temperatures, and corrosive environments caused by natural hydrocarbons and additives.
e. HVAC systems: Gate valves are used for regulating the flow of heating or cooling medium in commercial and industrial heating, ventilation, and air conditioning (HVAC) systems. They are often preferred for their low-pressure drop and precise flow control.
3.Selection and Maintenance of Gate Valve Bodies
In order to choose the most suitable gate valve for a specific application, a number of factors must be considered:
a. Fluid properties: The type and properties of the fluid being handled, such as its temperature, pressure, viscosity, and chemical compatibility with the valve materials, directly affect the performance and service life of the gate valve.
b. Flow requirements: The desired flow rate, pressure drop, and control precision must be considered when selecting the appropriate gate valve size, type, and actuator.
c. Installation, maintenance, and repair: Gate valves should be easy to install, inspect, maintain, and repair, as their performance depends on proper alignment, sealing, and actuation. Routine maintenance, such as checking for leaks or wear, and timely repairs can extend the service life of gate valves and reduce downtime and replacement costs.
Gate valve bodies play a crucial role in fluid flow control systems across various industries. Their proper selection, installation, and maintenance are key factors in ensuring their efficient and reliable performance. With advancements in materials, design, manufacturing processes, and smart technology, gate valves will continue to meet the evolving needs and challenges of fluid flow control applications.