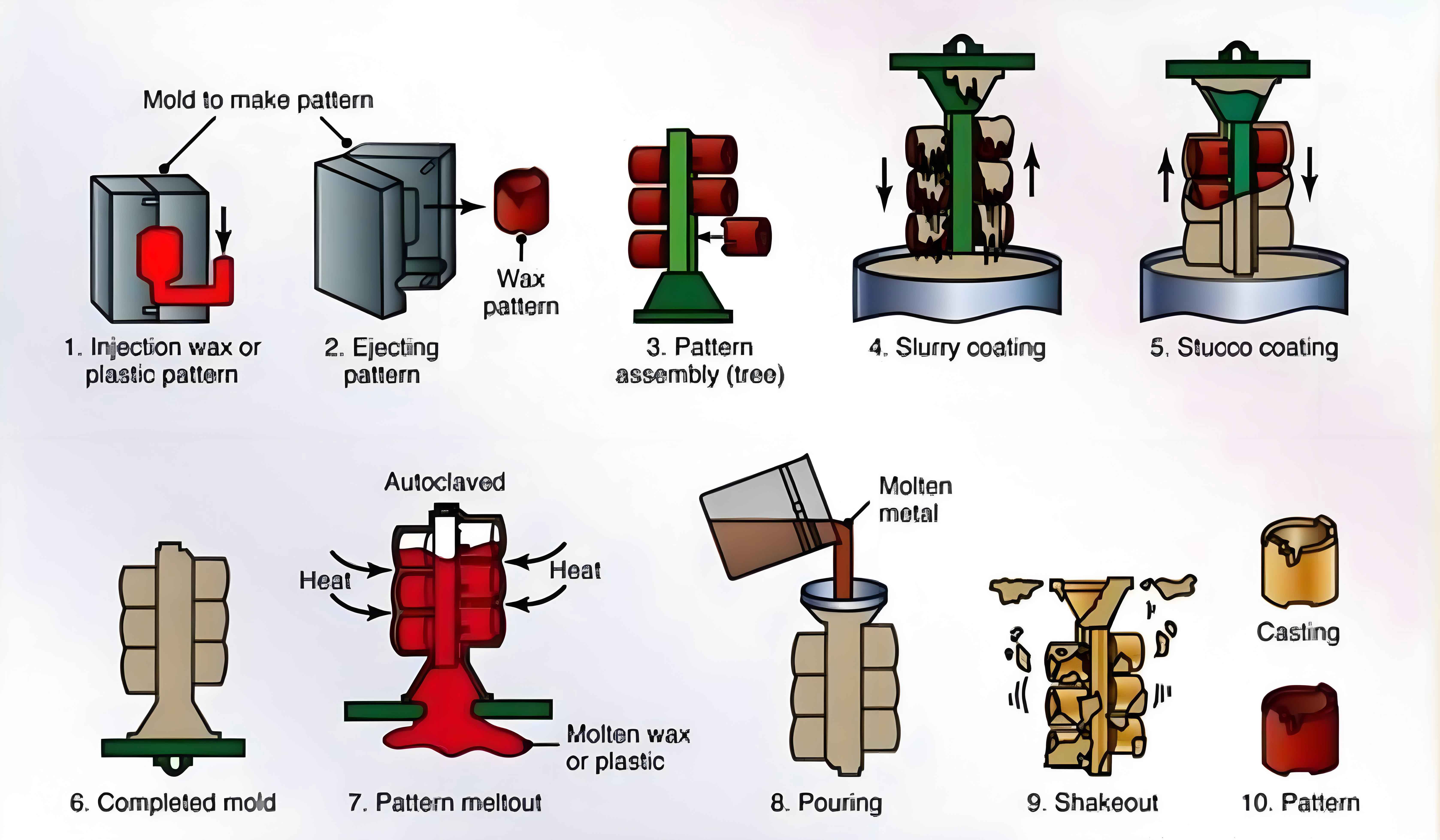
Investment casting is a manufacturing process with ancient origins but significant modern-day applications. It is especially critical in industries that demand high precision, superior performance, and complex geometries. Among these industries, aerospace and electric vehicles (EVs) stand out due to their stringent requirements and rapid advancements. This article delves into the pivotal role of investment casting in these two high-tech sectors, highlighting its benefits, applications, and the synergies between them.
Introduction to Investment Casting
Investment casting involves creating a detailed wax model of the part to be produced. This model is then coated with a ceramic material to form a mold, after which the wax is melted away, leaving a hollow ceramic shell. Molten metal is poured into this shell to form the final part. This process allows for the production of components with intricate designs, fine details, and excellent surface finishes, making it ideal for high-precision applications.
Benefits of Investment Casting
1. Precision and Accuracy
Investment casting can produce parts with tight tolerances and complex geometries, essential for aerospace and EV components that require high precision and reliability.
2. Material Versatility
The process supports a wide range of metals, including aluminum, titanium, stainless steel, and superalloys, allowing for the selection of materials best suited for specific performance requirements.
3. Surface Finish and Detail
The method yields excellent surface finishes and fine details, reducing the need for extensive post-processing and ensuring high-quality final products.
4. Design Flexibility
Investment casting facilitates the production of complex shapes, internal passages, thin walls, and intricate details, providing designers with significant freedom and innovation potential.
5. Cost Efficiency
For large production runs, investment casting becomes cost-effective due to its precision and minimal need for secondary operations. The near-net shape capability also reduces material waste.
Investment Casting in the Aerospace Industry
The aerospace industry relies heavily on investment casting for its ability to produce high-strength, lightweight components with exceptional precision. Key applications include:
1. Turbine Blades
Turbine blades used in jet engines are often produced using investment casting due to the process’s ability to handle high-performance superalloys and create intricate cooling passages within the blades.
2. Structural Components
Aerospace structures, such as airframe components and landing gear parts, benefit from the strength-to-weight ratio provided by investment-cast titanium and aluminum alloys.
3. Engine Parts
Components like combustion chambers, nozzle guide vanes, and compressor blades are critical for engine efficiency and performance. Investment casting ensures these parts meet exacting standards.
4. Space Exploration
Investment casting is also essential in producing components for spacecraft, where reliability, lightweight, and high performance are crucial.
Investment Casting in the Electric Vehicle Industry
The rise of electric vehicles (EVs) has spurred demand for advanced manufacturing techniques that can meet the industry’s unique challenges. Investment casting plays a crucial role in this sector by enabling the production of components that contribute to vehicle efficiency, performance, and sustainability.
1. Battery Components
Investment casting is used to produce components for EV batteries, such as battery housings and connectors, ensuring precise fit and optimal performance.
2. Motor Parts
Electric motors rely on intricate cast parts like rotor and stator components. Investment casting ensures these parts meet the necessary specifications for efficiency and durability.
3. Lightweight Structures
The need for lightweight yet strong components is paramount in EVs to maximize range and efficiency. Investment-cast aluminum and magnesium parts help reduce vehicle weight without compromising strength.
4. Thermal Management
Investment casting is used to produce parts for thermal management systems in EVs, such as heat exchangers and cooling plates, which are critical for maintaining optimal battery temperatures.
Comparative Analysis: Aerospace vs. Electric Vehicle Investment Casting
Parameter | Aerospace Industry | Electric Vehicle Industry |
---|---|---|
Primary Materials | Superalloys, Titanium, Aluminum | Aluminum, Magnesium, Stainless Steel |
Key Components | Turbine Blades, Structural Components, Engine Parts | Battery Components, Motor Parts, Lightweight Structures |
Precision Requirements | Very High (±0.005 inches per inch) | High (±0.010 inches per inch) |
Surface Finish Needs | Excellent (minimal post-processing) | Good (some post-processing) |
Production Volumes | Moderate to High | High |
Design Complexity | Very High (complex geometries, fine details) | High (complex shapes, internal passages) |
Cost Sensitivity | High (due to material and precision requirements) | Moderate (focus on balance between cost and performance) |
Future Trends in Investment Casting for Aerospace and EVs
Integration with Additive Manufacturing
The combination of additive manufacturing (3D printing) with investment casting is revolutionizing both industries. 3D printing can create highly detailed wax patterns or direct ceramic molds, enhancing the precision and reducing lead times for investment casting.
Advanced Materials
Research into new materials and alloys, such as lightweight composites and high-temperature superalloys, is expanding the capabilities of investment casting. These materials offer superior performance characteristics, essential for both aerospace and EV applications.
Digital Twin Technology
The use of digital twin technology, which creates a virtual replica of the casting process, is improving the ability to predict and optimize outcomes. This reduces defects and enhances overall process efficiency.
Sustainable Practices
Sustainability is becoming a priority, with investment casting incorporating eco-friendly materials, energy-efficient processes, and recycling initiatives. This shift is particularly important in the EV industry, which emphasizes environmental sustainability.
Conclusion
Investment casting plays a critical role in the aerospace and electric vehicle industries, providing the precision, versatility, and efficiency needed to produce high-performance components. The ability to create complex geometries with tight tolerances and excellent surface finishes makes investment casting indispensable for both sectors.
As technology continues to advance, the integration of additive manufacturing, the development of advanced materials, and the adoption of digital twin technology will further enhance the capabilities of investment casting. These innovations will drive improvements in component performance, cost-efficiency, and sustainability, ensuring that investment casting remains a cornerstone of modern manufacturing in the aerospace and electric vehicle industries.
In conclusion, investment casting is not only meeting the current demands of aerospace and EV manufacturing but also paving the way for future advancements. Its continued evolution will support the development of next-generation aircraft and electric vehicles, contributing to technological progress and industry growth.