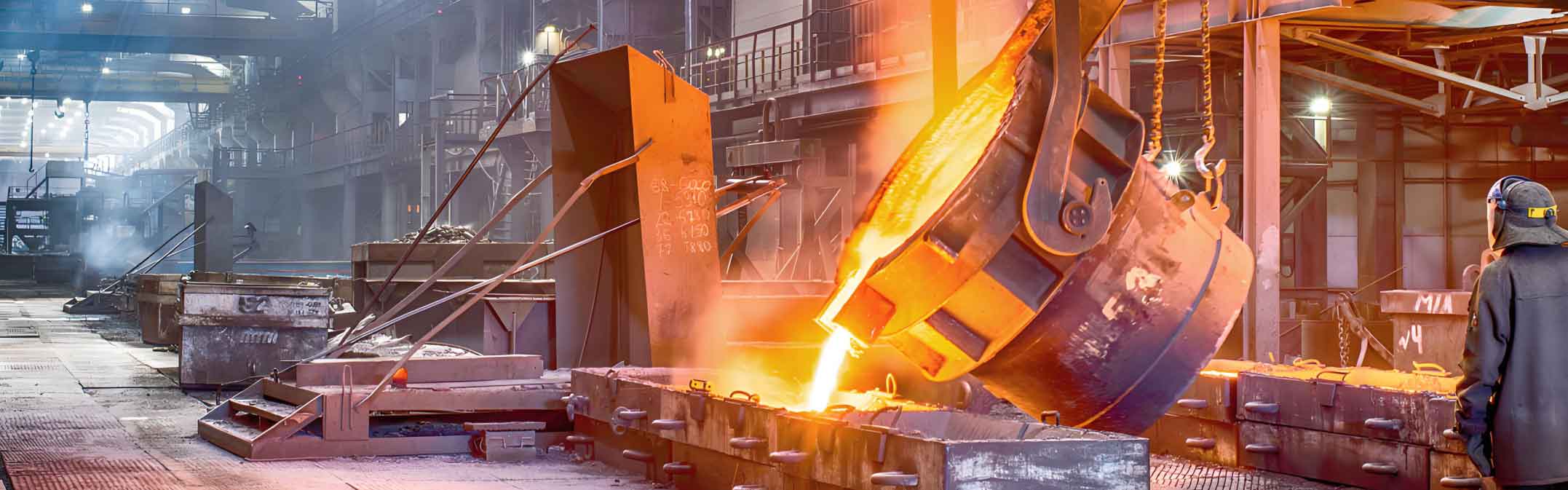
Investment casting has emerged as a pivotal process in modern manufacturing. This technique, with roots dating back thousands of years, has evolved to meet the stringent demands of today’s industrial landscape. It offers unparalleled precision, versatility, and efficiency, making it a preferred choice for producing complex components across various industries. This article explores the role of investment casting in modern manufacturing, highlighting its advantages, applications, and future prospects.
Introduction to Investment Casting
Investment casting involves creating a wax model of the desired part, coating it with a ceramic material to form a mold, and then melting away the wax to leave a cavity. Molten metal is poured into this cavity to form the final part. The process allows for the production of components with intricate designs, fine details, and excellent surface finishes. This ability to produce highly detailed and precise parts is what sets investment casting apart from other manufacturing methods.
Advantages of Investment Casting
1. Precision and Accuracy
Investment casting is renowned for its ability to produce parts with tight tolerances and complex geometries. The process can achieve exceptional accuracy, often within ±0.005 inches per inch, making it ideal for components that require high precision.
2. Versatility
The process is versatile and can be used with a wide range of metals, including stainless steel, aluminum, titanium, and superalloys. This versatility allows manufacturers to select the best material for their specific application, whether it requires high strength, corrosion resistance, or lightweight properties.
3. Surface Finish
Investment casting produces parts with excellent surface finishes, often requiring minimal post-processing. This reduces the need for additional machining and polishing, saving time and costs.
4. Design Flexibility
The ability to cast complex shapes and intricate details provides designers with greater freedom in creating innovative components. Features such as internal passages, thin walls, and fine details can be easily incorporated into the design.
5. Cost-Effectiveness
While the initial tooling costs for investment casting can be high, the process becomes cost-effective for large production runs due to its precision and minimal need for secondary operations. Additionally, the ability to produce near-net shape parts reduces material waste.
Applications of Investment Casting
Aerospace
Investment casting is widely used in the aerospace industry for producing critical components such as turbine blades, engine parts, and structural elements. The process’s ability to produce high-precision, high-strength parts from superalloys is crucial for aerospace applications.
Automotive
In the automotive industry, investment casting is employed to manufacture parts such as engine components, transmission parts, and suspension systems. The process allows for the production of lightweight yet strong components, contributing to improved fuel efficiency and performance.
Medical Devices
Investment casting is essential in the production of medical devices and implants. The process’s precision and ability to work with biocompatible materials like titanium and stainless steel make it ideal for surgical instruments, orthopedic implants, and dental devices.
Energy
The energy sector relies on investment casting for producing components used in power generation, including gas and steam turbines, as well as parts for oil and gas exploration. The process ensures the reliability and durability of these critical components.
Industrial Machinery
Investment casting is used to manufacture various components for industrial machinery, such as pump housings, valve bodies, and gear components. The process’s ability to produce complex shapes with high precision enhances the performance and reliability of industrial equipment.
Comparative Analysis: Investment Casting vs. Other Manufacturing Methods
Parameter | Investment Casting | Sand Casting | Machining |
---|---|---|---|
Precision | High (±0.005 inches per inch) | Moderate (±0.020 inches per inch) | Very High (±0.001 inches per inch) |
Surface Finish | Excellent (minimal post-processing) | Fair (requires machining) | Excellent |
Material Waste | Low (near-net shape parts) | Moderate (more excess material) | High (significant waste) |
Complexity of Shapes | High (intricate designs possible) | Moderate (limited by sand mold) | Low (limited by tooling capabilities) |
Cost for Large Runs | Cost-effective | Cost-effective for simple parts | Expensive |
Tooling Cost | High (initial mold creation) | Low | None (tooling costs in cutting tools) |
Production Speed | Moderate | High for large parts | Slow |
Material Versatility | High | High | Limited |
Future Prospects of Investment Casting
Digitalization and Industry 4.0
The integration of digital technologies, such as computer-aided design (CAD) and computer-aided manufacturing (CAM), is revolutionizing investment casting. These tools enable precise modeling and simulation of the casting process, reducing errors and improving efficiency. Additionally, Industry 4.0 technologies like IoT and AI are enhancing real-time monitoring and quality control.
Additive Manufacturing Integration
The synergy between additive manufacturing (3D printing) and investment casting is opening new avenues for producing complex and customized parts. 3D printing can be used to create highly detailed wax patterns or directly print ceramic molds, reducing lead times and costs.
Advanced Materials
Ongoing research into new materials and alloys is expanding the capabilities of investment casting. Advanced materials that offer superior mechanical properties, corrosion resistance, and temperature stability are being developed to meet the demands of high-performance applications.
Sustainable Manufacturing
Investment casting is becoming more sustainable through the adoption of eco-friendly materials and processes. Recyclable waxes, energy-efficient furnaces, and reduced material waste contribute to the environmental benefits of this manufacturing method.
Conclusion
Investment casting plays a crucial role in modern manufacturing, offering unparalleled precision, versatility, and efficiency. Its ability to produce complex geometries with high accuracy and excellent surface finishes makes it indispensable in industries such as aerospace, automotive, medical devices, energy, and industrial machinery. Despite its challenges, continuous advancements in digitalization, materials, and sustainability are enhancing the capabilities and applications of investment casting.
In conclusion, the strategic implementation of investment casting in modern manufacturing not only meets the stringent requirements of high-performance components but also drives innovation and competitiveness. As technology continues to evolve, investment casting will remain a vital and dynamic process, contributing to the development of advanced, high-quality parts that support the growth and advancement of various industries.