The electric vehicle (EV) industry is rapidly transforming the automotive landscape, driven by the need for sustainable transportation solutions. As this industry evolves, the steel casting process plays an increasingly vital role in the production of high-performance, durable, and lightweight components essential for electric vehicles. The steel casting process offers unique advantages in terms of strength, precision, and cost-effectiveness, making it indispensable for various applications within electric vehicle (EV) sector.
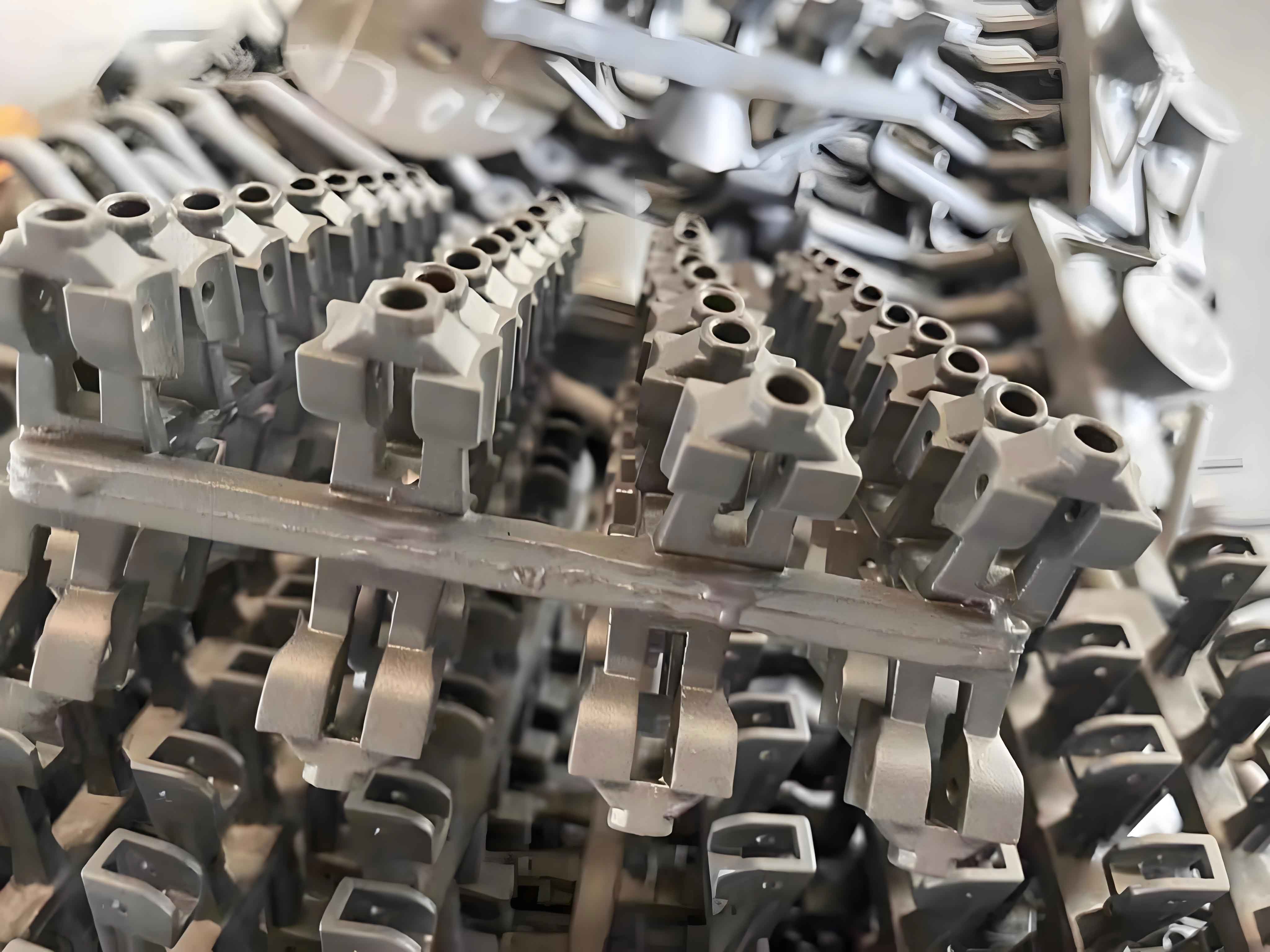
Overview of Steel Casting Process
The steel casting process involves creating components by pouring molten steel into molds, where it solidifies into the desired shape. This process is characterized by several key stages:
- Raw Material Preparation: Selection and preparation of high-quality raw materials, including iron ore and alloys.
- Melting and Refining: Melting raw materials in furnaces and refining the molten steel to achieve the required composition.
- Mold Preparation: Creating precise molds using materials like sand or ceramics.
- Pouring and Casting: Pouring the molten steel into molds and allowing it to cool and solidify.
- Finishing and Machining: Cleaning, machining, and inspecting the castings to ensure they meet specifications.
Importance of Steel Casting in Electric Vehicle Components
1. Structural Components
Chassis and Frame: The chassis and frame of electric vehicles require materials that offer a balance of strength and weight. The steel casting process produces components that are robust yet lightweight, essential for improving vehicle efficiency and safety.
Suspension Parts: Components such as control arms, knuckles, and suspension links benefit from the precision and durability provided by the steel casting process. These parts must withstand dynamic loads and harsh operating conditions.
2. Powertrain Components
Motor Housings: The steel casting process is ideal for producing motor housings that protect electric motors from environmental and mechanical damage while providing thermal conductivity to dissipate heat.
Transmission Components: Gears, shafts, and other transmission components cast from steel offer the necessary strength and wear resistance to handle the high torque and rotational speeds typical in electric vehicles.
3. Battery Enclosures
Battery enclosures in electric vehicles must be strong enough to protect the battery cells while being lightweight to enhance vehicle range. The steel casting process enables the production of thin-walled, complex shapes that meet these requirements.
Advantages of Steel Casting Process for Electric Vehicle Industry
- High Precision: The steel casting process allows for the creation of components with intricate geometries and tight tolerances, ensuring a perfect fit and function within electric vehicles.
- Material Strength: Steel castings offer superior mechanical properties, including high tensile strength, impact resistance, and durability, essential for critical electric vehicle (EV) components.
- Cost-Effectiveness: The steel casting process is cost-efficient, especially for producing complex parts in large quantities, making it an economical choice for the electric vehicle industry.
- Design Flexibility: The ability to cast complex shapes and incorporate multiple functions into a single component reduces the need for assembly and welding, streamlining manufacturing processes.
Environmental Considerations
As the electric vehicle industry emphasizes sustainability, the environmental impact of the steel casting process is a critical consideration. Efforts to minimize this impact include:
- Recycling: Utilizing recycled steel scrap in the casting process reduces the need for virgin raw materials and decreases energy consumption.
- Energy Efficiency: Implementing energy-efficient technologies in melting and refining can significantly reduce greenhouse gas emissions.
- Waste Management: Proper disposal and recycling of foundry waste, including spent sand and slag, mitigate environmental pollution.
Tables Illustrating Key Components and Their Benefits
Table 1: Key Structural Components in Electric Vehicles
Component | Function | Benefits of Steel Casting Process |
---|---|---|
Chassis and Frame | Provides structural integrity and safety | High strength, lightweight, precise |
Suspension Parts | Ensures smooth ride and handling | Durable, wear-resistant, precise |
Motor Housings | Protects electric motor and dissipates heat | Thermal conductivity, robust, precise |
Transmission Components | Transmits power from motor to wheels | High strength, wear-resistant, precise |
Table 2: Environmental Benefits of Steel Casting Process
Aspect | Benefits |
---|---|
Recycling | Reduces raw material consumption and energy use |
Energy Efficiency | Lowers greenhouse gas emissions |
Waste Management | Mitigates environmental pollution |
Lists of Common Applications and Their Requirements
Common Applications of Steel Casting in Electric Vehicles:
- Chassis and Frame Components: Require high strength-to-weight ratio, corrosion resistance, and durability.
- Suspension Parts: Need to withstand dynamic loads, offer precision fit, and resist wear and tear.
- Motor Housings: Must provide thermal management, mechanical protection, and structural integrity.
- Transmission Components: Require high torque capacity, precision engineering, and longevity.
Key Requirements for Steel Casting Components in Electric Vehicles:
- Mechanical Strength: Ability to withstand high loads and stresses.
- Precision: Tight tolerances to ensure proper fit and function.
- Durability: Long service life with resistance to wear and environmental factors.
- Weight Efficiency: Lightweight to enhance vehicle performance and range.
Conclusion
The steel casting process plays a pivotal role in the electric vehicle industry, contributing to the production of high-quality, reliable, and efficient components. The inherent advantages of the steel casting process, including high precision, material strength, cost-effectiveness, and design flexibility, make it indispensable for manufacturing critical electric vehicle (EV) parts. As the electric vehicle industry continues to grow, the importance of sustainable practices within the steel casting process will become increasingly significant, ensuring that the transition to electric mobility is both technologically advanced and environmentally responsible.