Grey cast iron is a type of cast iron known for its strength, versatility, and excellent castability. It is widely used in various industries due to its unique properties and cost-effectiveness. Here is a comprehensive overview of grey cast iron:
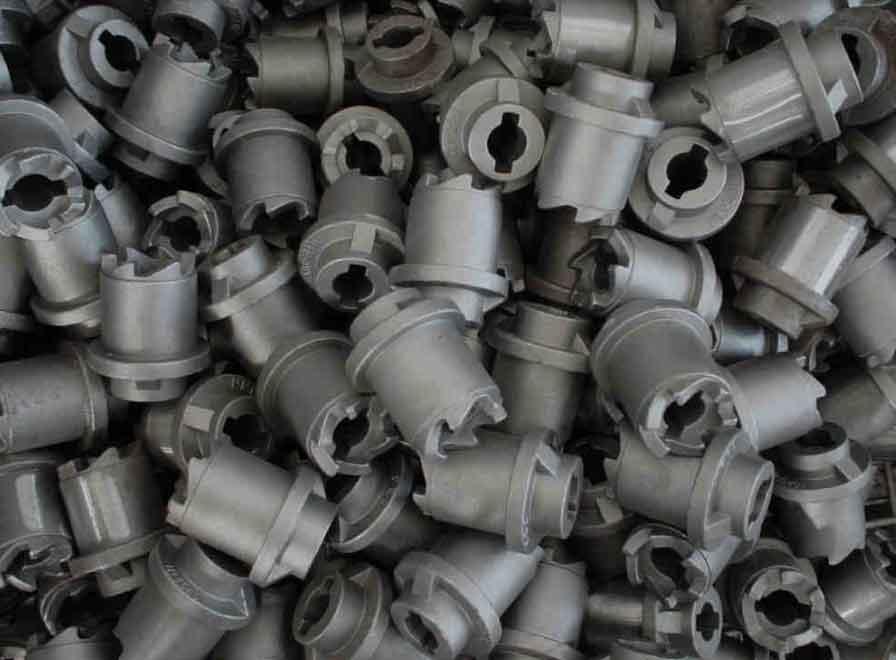
1. Composition:
Grey cast iron is primarily composed of iron (Fe) with a high carbon content of 2% to 4%. It also contains silicon (Si), manganese (Mn), sulfur (S), and phosphorus (P). The presence of carbon in the form of graphite flakes gives it its characteristic grey appearance.
2. Strength and Durability:
Grey cast iron possesses good compressive strength, making it suitable for applications where high load-bearing capacity is required. It has excellent resistance to deformation under compression and can withstand heavy loads without permanent distortion.
3. Castability:
Grey cast iron exhibits excellent casting properties, making it easy to pour and shape into complex geometries. It has a low melting point, good fluidity when molten, and good solidification characteristics, allowing for intricate casting designs and complex parts.
4. Wear Resistance:
Grey cast iron has good wear resistance, particularly in applications involving sliding or abrasive wear. The graphite flakes act as solid lubricants, reducing friction and wear between mating surfaces. This makes it suitable for components that experience repeated contact or sliding, such as machine beds, cylinder liners, and brake drums.
5. Damping Capacity:
Grey cast iron has high damping capacity, which means it can absorb and dissipate vibration and noise. This property makes it ideal for applications where noise reduction or vibration damping is important, such as engine blocks, machine tools, and automotive components.
6. Thermal Conductivity:
Grey cast iron has good thermal conductivity, allowing it to transfer heat efficiently. This property is advantageous in applications where heat dissipation is required, such as engine components, cookware, and heat exchangers.
7. Machinability:
Grey cast iron is relatively easy to machine due to its graphite structure, which helps in chip formation and reduces tool wear. It can be machined into complex shapes with tight tolerances, making it suitable for various manufacturing processes.
8. Corrosion Resistance:
While grey cast iron is not highly corrosion-resistant, it can withstand certain environments and moderate exposure to moisture or chemicals. In some cases, additional coatings or surface treatments may be applied to enhance its corrosion resistance.
9. Cost-Effectiveness:
Grey cast iron is cost-effective compared to other materials, such as steel or non-ferrous alloys. Its abundance, ease of production, and versatility make it a popular choice in many industries where cost is a significant factor.
10. Applications:
Grey cast iron finds wide applications across industries. Some common applications include engine blocks, cylinder heads, brake components, pump housings, valves, pipes, manhole covers, cookware, and machinery parts.
It is important to note that grey cast iron has limitations, such as its brittleness, limited tensile strength, and lower impact resistance compared to other materials. These limitations should be considered when selecting grey cast iron for specific applications. However, its overall strength, versatility, and cost-effectiveness make it a reliable and widely used material in various industrial sectors.