Compared with ordinary quenching and tempering, the hardness, tensile strength, elongation and impact value of forgings can be increased by 10%, 3-10%, 10-40% and 20-30% respectively. Generally, the increase of strength and hardness by ordinary heat treatment is always accompanied by the decrease of plasticity and toughness, while the strength and impact value can be improved by forging residual heat quenching at the same time.
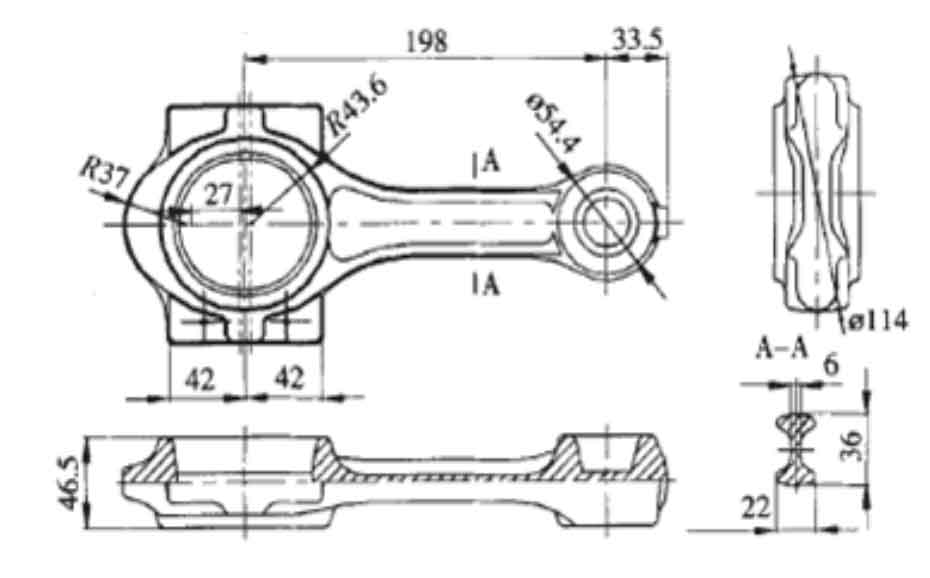
Forging heat quenching is also called thermomechanical treatment process. Due to the effective combination of forging and heat treatment processes, forging heat quenching can play the role of deformation strengthening and heat treatment strengthening at the same time, obtain comprehensive mechanical properties that can not be achieved by a single strengthening method, and eliminate the re high-temperature heating during heat treatment, thus saving a lot of energy consumption, heating equipment and workshop area, and reducing the oxidation burning loss of materials, decarburization, deformation and other heat treatment defects. Therefore, the forging heat quenching process has both excellent toughening effect and huge economic benefits. The forging heat quenching process has long been widely used in the machine manufacturing industry in foreign countries. In China, in the early 1970s, the forging heat quenching process was first applied to the production of connecting rods in the engine manufacturing industry, such as Shanghai diesel engine plant and Beijing internal combustion engine general plant, and great economic benefits were achieved. Compared with the conventional quenching and tempering process, the forging heat quenching process has many excellent characteristics in terms of improving product performance, saving energy, improving environmental protection and improving labor hygiene conditions.