Abstract
This paper presents a comprehensive study on the casting process design and numerical simulation of thin-walled spherical shell components. The paper begins by introducing the structural features and technical requirements of the thin-walled spherical shell. Subsequently, the initial casting process is reviewed, followed by an analysis of the defects encountered during the initial production phase. Based on this analysis, optimizations are proposed for the parting system, gating system, and venting system. Numerical simulations are conducted using ProCAST software to evaluate the effectiveness of the proposed optimizations. The results demonstrate significant improvements in casting quality, with a notable increase in the first-time yield rate from 54.5% to 89%. This study highlights the importance of process optimization and numerical simulation in achieving high-quality castings for complex thin-walled components.
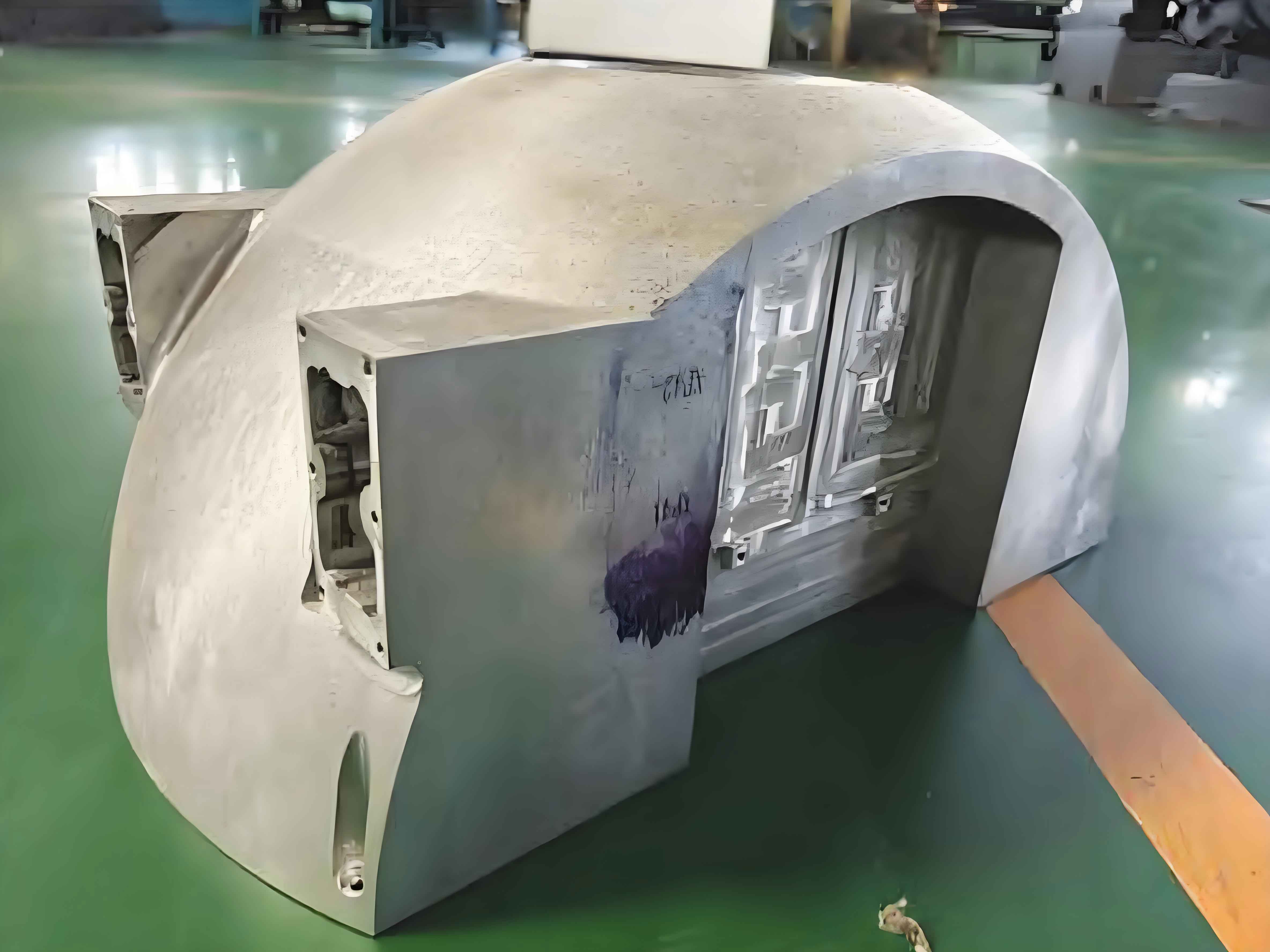
Introduction
Thin-walled spherical shell components are widely used in various industries, including aerospace, automotive, and energy sectors, due to their lightweight and high strength-to-weight ratio. However, casting such components presents several challenges related to their complex geometries, thin walls, and tight dimensional tolerances. This paper focuses on the casting process design and optimization of a thin-walled spherical shell component using numerical simulation techniques.
Part 1: Component Description and Technical Requirements
1.1 Structural Features
The thin-walled spherical shell component under study has a complex geometry. The overall shape resembles a sphere with two “wings” protruding from the left side and a large through-hole on the right. The internal structure includes several disconnected circular bosses, resulting in non-uniform wall thicknesses.
1.2 Technical Requirements
The component must meet specific technical requirements to ensure its functionality and reliability:
- Material and Heat Treatment: The shell is cast using ZL104 aluminum alloy and subjected to T6 heat treatment to improve mechanical properties.
- Chemical Composition: The alloy composition must comply with GB/T 1173—2013 standards (Table 1).
- Mechanical Properties: The post-processed component must meet the mechanical properties outlined in Table 2.
- Dimensional Tolerance: The dimensions must adhere to the specified tolerances to ensure proper assembly and functioning.
- Air Tightness: The component must maintain an airtight seal, with a pressure drop not exceeding 1 kPa in 10 minutes at 1.35 atmospheres.
Table 1: Chemical Composition Requirements (wt.%)
Element | Minimum | Maximum |
---|---|---|
Si | 10.0 | 13.0 |
Cu | 1.0 | 3.0 |
Mg | 0.2 | 0.6 |
Mn | 0.15 | 0.4 |
Ti | 0.10 | 0.20 |
Fe | 0.7 | 1.3 |
Zn | 0.25 | 0.35 |
Sn | 0.10 | 0.25 |
Pb | – | 0.10 |
Other | – | 0.15 |
Al | Balance |
Table 2: Mechanical Properties Requirements
Property | Requirement |
---|---|
Tensile Strength (MPa) | ≥ 220 |
Yield Strength (MPa) | ≥ 150 |
Elongation at Break (%) | ≥ 3 |
Part 2: Initial Casting Process and Defects Analysis
2.1 Initial Casting Process
The initial casting process for the thin-walled spherical shell employed a resin sand gravity casting method using a split-type core box. The gating system was designed as an open bottom pour with a ceramic filter placed at the base of the sprue to filter impurities and reduce turbulence. The riser and gating system were placed in the upper box, and sand cores were painted and dried before assembly.
2.2 Defects Encountered
Despite the initial process appearing sound, defects were observed during post-machining inspections. Specifically, shrinkage porosity was discovered at the side wall corners .
The defects were attributed to two primary causes:
- Inadequate Feeding: The upper riser placement was challenging due to the spherical geometry, resulting in inefficient feeding of the upper sections.
- Poor Ventilation: The side wall corners acted as gas traps, lacking sufficient venting to expel trapped gases during pouring.
Part 3: Process Optimization
Based on the defect analysis, optimizations were proposed for the parting system, gating system, and venting system.
3.1 Parting System Optimization
The parting line was adjusted to improve core stability and facilitate riser placement. The revised parting line .
3.2 Gating System Optimization
The gating system was redesigned to improve metal flow and feeding efficiency. The new system incorporated a larger riser placed strategically to effectively feed the upper sections and reduce shrinkage porosity .
3.3 Venting System Optimization
To address gas trapping, a pressure-assisted venting system was incorporated into the side wall corners. The venting channels were designed to efficiently evacuate trapped gases during pouring .
Part 4: Numerical Simulation
Numerical simulations were conducted using ProCAST software to evaluate the effectiveness of the proposed optimizations.
4.1 Simulation Setup
The simulation model included detailed representations of the gating system, riser, and venting channels. Material properties for ZL104 aluminum alloy were used, and the simulation included solidification analysis to predict defect formation.
4.2 Temperature Field Distribution
The simulated temperature field during solidification . The optimized gating system and riser placement resulted in a more uniform temperature distribution, reducing hot spots and improving feeding efficiency.
4.3 Defect Prediction
The simulation results predicted a significant reduction in shrinkage porosity, particularly in the side wall corners. This confirmed the effectiveness of the optimized gating and venting systems.
Part 5: Production Verification
The optimized casting process was implemented, and production castings were evaluated. The first-time yield rate increased from 54.5% to 89%, confirming the success of the optimization efforts. Post-machining inspections revealed a marked reduction in shrinkage porosity defects .
Part 6: Conclusion
This study demonstrates the importance of casting process optimization and numerical simulation in achieving high-quality thin-walled spherical shell components. By optimizing the parting system, gating system, and venting system, significant improvements were achieved in casting quality and first-time yield rate. The results highlight the potential of combining experimental and numerical approaches to address casting challenges associated with complex thin-walled geometries.