1. Foundry Technology
The casting modulus is 4.29 cm, the quality of molten iron is 11 500 kg, the pouring temperature is 1 360 C, the heat insulation in the box is 104 h, and the pouring time is 120 s.The charge ratio is 75% wind-driven iron + 10% scrap steel + 15% reburning charge, and 0.3% SiC is used for pretreatment.Target values of chemical composition: CE controlled at about 4.4%, w (C-end) 3.7%, w (Si-end) 2.1%.
Foundry technology is shown in Figure 2. Molding with furan resin sand and core-making is adopted. The split-die and open-loop moulding is determined considering the lifting capacity of the vehicle, the direction of lifting and the model structure.In order to ensure the size of the castings and prevent the deformation of the sand core, #1 and #2 sand core shells are made of steel and wood. #1 sand core is made of exhaust steel pipes with a diameter of_70 mm x 1 800 mm and #2 sand core is used as special core bones.
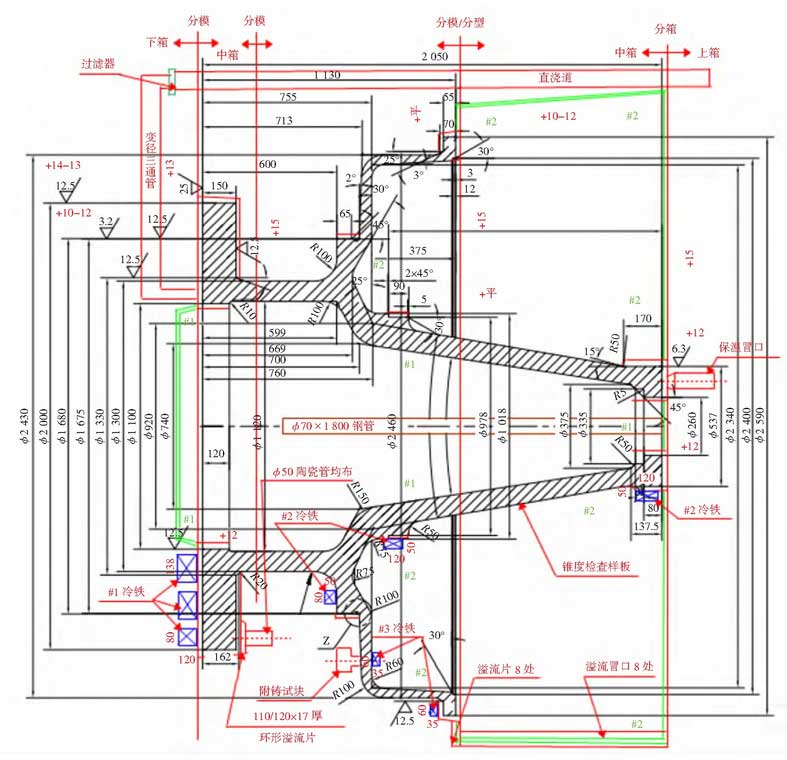
It is difficult to control the solidification process because the casting position is small and large, which is not conducive to shrinkage. 5 dispersed heat joints are difficult to control the solidification process and need to be focused on.The shrinkage condition of rotary casting is not easy to master and also has flaw detection requirement. Therefore, it is very important to prevent shrinkage defects and shrinkage defects for casting quality. The solidification process can be controlled by combining cold iron and riser technology to prevent shrinkage defects.
Select the bottom pouring, open pouring system [1-7], the gate ratio is F straight: F horizontal: F inside = 1:1.3:2.5.The inner runner is made of 10_80 mm/_50 mm variable diameter tee ceramic bends and 10 funnel-shaped filter devices. Each filter device is equipped with a 120 mm x 120 mm x 22 mm foam ceramic filter. The filter area is more than 5 times the cross-section area of the inner runner. The cross-runner is made of_80 mm ceramic tube with symmetrical double-sided flow direction. The straight runner is made of_100 mm ceramic tube.
The cold iron is arranged as follows: the flange surface of the lower box of the hot section 5 is the position of the inner runner, 110 pieces of heavy cold iron with a thickness of 138 mm x 80 mm x 120 mm and a thickness of 120 mm are placed; the position of the hot section 4 is the compensating passage, and the thickness of the cold iron is smaller than the calculated value. There are 28 pieces of # cold iron with a size of 120 mm x 80 mm x 50 mm and a thickness of 50 mm.30 pieces of #2 chilled iron are placed in the hot section 3 to regulate solidification. The hot section 2 is protruding with good heat dissipation regulation. The thickness of chilled iron is smaller than the calculated value. 60 pieces of #3 chilled iron are placed in the hot section 3 with the size of 100 mm x 60 mm x 35 mm and the thickness of 35 mm.Mm; hot joint 1 is located at the lower end of riser, the cold iron should not only regulate solidification, but also keep the compensating passage unblocked. The thickness of cold iron is smaller than the calculated value, and 16 pieces of #2 cold iron should be placed; 6 contact hot joints formed by casting test pieces are attached, and 12 pieces of #3 cold iron should be placed at the corresponding position in #2 sand core on its back.
The riser is set as follows: the upper plane of the flange of_2 000 mm x 150 mm is dead angle and easy to agglomerate; the process setting is 110/120 mm x 17 mm annular overflow piece, on which the ceramic pipe of_50 mm is distributed; the middle_2 590 mm flange surface is set with 8 overflow sheets and overflow side risers; the local modulus of the upper box surface is 3.66 cm, and three_180 mm x 450 mm insulation risers (riser neck_90 mm) are set with the riser modulus of 3.74.Cm, mainly acts as a supplement.
After core setting, dry with hot air blower until pouring.In order to maximize the graphitized expansion of ductile iron, a strong sand box with thick wall is selected. When the sand boxes are fastened between layers, M24 bolts are used to connect the bonding surfaces. Two sets of lock box pressure are set on the upper box to prevent lifting.15 t plug-pulling gate cup is used for pouring.
2. Pilot production results of the first piece
First castings No. 0094276001, chemical composition: w(C) 3.56%, w(Si) 1.96%, w(Mn) 0.18%, w(P) 0.024%, w(S) 0.011%, w(Ce) 0.005%, w(Mg) 0.052%, w(CE) 4.22%, pouring temperature 1 382%, tensile strength 374 MPa, yield strength 234 MPa, elongation 22%, low temperature impact value 12 J, 13.5 J, 14 J.
Compared with the technical requirements, the magnetic particle test, appearance, full-size scribe test, leakage test, metallographic structure, tensile strength, elongation are all qualified, and the yield strength is not qualified.The ultrasonic inspection results of the castings show that there are no surface slag and there are 6 large areas of shrinkage and porosity defects. As shown in Figure 3, the ultrasonic inspection results are not qualified. Based on the above technical indexes, the castings are scrapped.