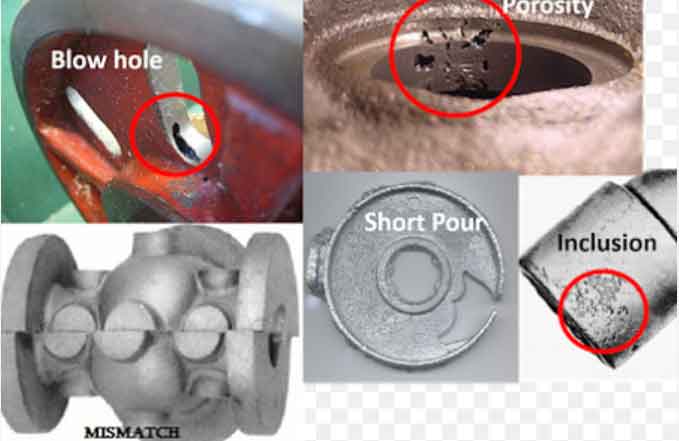
Casting defects can pose significant challenges in the metal casting process, affecting the quality and integrity of the final product. It is crucial to understand these defects, their causes, and effective solutions to ensure successful casting production. This article explores common casting defects, provides insights into their causes, and offers strategies for resolving these challenges.
- Porosity:
- Causes: Porosity occurs when gas is trapped in the casting during solidification. Causes include inadequate venting, improper gating and riser design, high moisture content in molds or cores, and excessive turbulence during filling.
- Solutions: Improve mold and core venting, optimize gating and riser design for efficient gas escape, control moisture content in molds and cores, and use appropriate mold coatings or additives to reduce gas entrapment.
- Shrinkage:
- Causes: Shrinkage defects result from the non-uniform solidification of molten metal, leading to localized shrinkage and voids. Factors include improper riser design, inadequate feeding, high solidification rate, and alloy composition.
- Solutions: Optimize riser design and placement to ensure proper feeding, control solidification rate through insulation or cooling techniques, modify alloy composition to reduce solidification shrinkage, and employ feeding aids such as chills or feeders.
- Cold Shut:
- Causes: Cold shuts occur when two or more streams of molten metal do not fuse properly during filling. Causes include inadequate gating design, insufficient pouring temperature or flow rate, and improper mold or core strength.
- Solutions: Improve gating design for smooth metal flow and fusion, adjust pouring parameters to ensure proper metal fluidity, strengthen molds and cores to prevent premature solidification, and use appropriate mold materials and coatings.
- Inclusions:
- Causes: Inclusions are foreign materials embedded in the casting, such as oxides, slag, or sand. They result from inadequate melt treatment, improper handling of raw materials, or contamination from mold or core materials.
- Solutions: Implement proper melt treatment practices, employ effective filtration systems, handle and store raw materials to prevent contamination, use appropriate fluxes or refining agents to remove impurities, and ensure clean mold and core materials.
- Surface Defects:
- Causes: Surface defects include rough surfaces, cracks, or metal penetration. They can result from inadequate mold or core coatings, improper mold or core materials, poor gating or venting design, and inadequate mold surface finish.
- Solutions: Use suitable mold and core coatings to promote smooth surfaces, select proper mold and core materials for improved casting quality, optimize gating and venting for controlled metal flow, and maintain good mold surface finish through proper mold maintenance.
- Dimensional Variations:
- Causes: Dimensional variations occur when castings deviate from the intended specifications. Causes include mold distortion, inadequate cooling or solidification control, improper mold or core assembly, and insufficient dimensional inspection.
- Solutions: Ensure proper mold alignment and assembly, control cooling rates to prevent distortions, optimize mold and core materials for dimensional stability, and implement thorough dimensional inspections.
Understanding and resolving casting defects is essential for producing high-quality castings. By identifying the causes and implementing appropriate solutions for defects such as porosity, shrinkage, cold shuts, inclusions, surface defects, and dimensional variations, manufacturers can overcome challenges and achieve defect-free castings. Continuous improvement, process optimization, material control, and quality assurance practices are key to navigating the complexities of casting defects and ensuring successful casting production.