Excavator bucket teeth are crucial components that enable excavators to effectively bite through the earth and perform various excavation tasks. Understanding their design and function can provide insights into their role in excavator operations. Here’s a breakdown of the design and function of excavator bucket teeth:
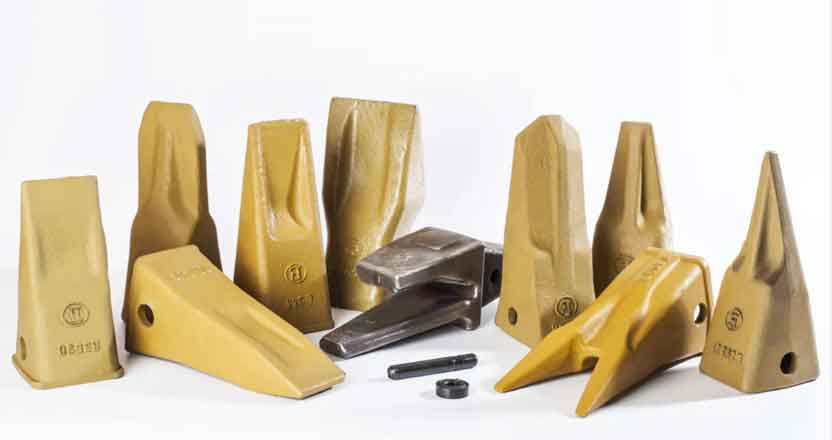
- Tooth Shape: Bucket teeth come in different shapes, each optimized for specific excavation tasks. The most common tooth shapes include:
- Standard Teeth: These teeth have a general-purpose design suitable for a wide range of materials and applications. They typically have a sharp, pointed tip for penetrating the ground efficiently.
- Rock Teeth: Designed for excavating in rocky terrain, rock teeth have a more robust construction with reinforced wear areas. They often feature a chisel-like shape for breaking through tough rock formations.
- Heavy-duty Teeth: These teeth are specifically engineered for demanding excavation tasks that involve compacted soils, frozen ground, or abrasive materials. They have a reinforced structure and additional wear protection to withstand extreme conditions.
- Trenching Teeth: These teeth have a narrow profile and extended tips, allowing for precise and efficient trenching operations. They minimize soil disturbance and facilitate cleaner trench formation.
- Tooth Adapter: The tooth adapter is the part that connects the tooth to the excavator bucket. It acts as a mounting interface, ensuring a secure attachment and facilitating easy tooth replacement when necessary. Tooth adapters are available in various designs and systems to match different excavator models and bucket types.
- Wear Protection: The cutting edges and wear areas of bucket teeth are susceptible to heavy wear during excavation. To enhance durability and extend the service life of the teeth, wear protection solutions are commonly used. These can include:
- Tooth Caps: Removable protective caps that cover the tooth tips, providing an additional layer of wear resistance.
- Side Cutters: Attachments mounted on the sides of the bucket that protect the edges and improve bucket performance in abrasive environments.
- Wear Plates: Reinforced plates welded onto the tooth and adapter surfaces to withstand intense wear and impact.
- Tooth Replacement: Over time, bucket teeth wear out and require replacement. The ease and efficiency of tooth replacement are essential for minimizing downtime. Most excavator bucket teeth are designed for quick and simple replacement, allowing operators to change teeth on-site without extensive tools or equipment.
By optimizing the design and selection of bucket teeth based on the excavation task at hand, operators can maximize the efficiency and performance of their excavators. Choosing the right tooth shape, utilizing appropriate wear protection, and ensuring proper tooth replacement contribute to enhanced productivity, reduced downtime, and cost savings in excavation operations.
It’s important to note that specific excavator models and manufacturers may have unique tooth designs and features. Consulting the manufacturer’s guidelines and recommendations is essential to ensure the best performance and longevity of bucket teeth for a particular excavator.