Heat treatment defects can pose significant challenges in achieving desired material properties and ensuring the reliability and performance of the treated components. Understanding these challenges is crucial for effective defect prevention and mitigation. Here are some key challenges associated with heat treatment defects:
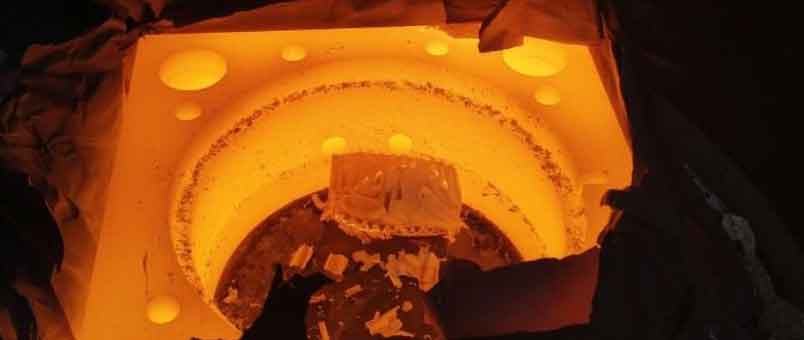
Complexity of the Heat Treatment Process:
Heat treatment involves a series of complex thermal and mechanical processes, including heating, soaking, cooling, and often multiple cycles of these steps. The interactions between temperature, time, cooling rates, and material composition can be challenging to control and optimize, making it susceptible to defects.
Material Variability:
Materials used in heat treatment processes can exhibit inherent variations in composition, microstructure, and prior processing history. These variations can influence the response to heat treatment and increase the likelihood of defects. Understanding material variability and its impact on the treatment process is essential.
Thermodynamic Transformations:
Heat treatment relies on phase transformations within the material, such as austenitization, martensitic transformation, and precipitation reactions. These transformations can be sensitive to process parameters and material composition, leading to defects if not adequately controlled. The complexity of these transformations makes it challenging to predict and prevent defects.
Non-Uniform Heating and Cooling:
Achieving uniform heating and cooling throughout the material can be difficult, especially for complex shapes or large components. Non-uniform temperature distribution can result in inconsistent microstructures and residual stresses, leading to defects such as distortion, soft spots, or cracking.
Quenching Challenges:
Quenching, a critical step in many heat treatment processes, involves rapid cooling to achieve desired material properties. However, the selection of quenching media, cooling rates, and agitation methods can be challenging. Improper quenching can lead to quench cracks, residual stresses, and inadequate hardness, compromising the component’s integrity.
Surface Contamination and Reactive Environments:
Heat treatment in reactive atmospheres or with inadequate protection can lead to surface contamination, such as decarburization or oxidation. Contamination can negatively affect the material’s properties and compromise its performance. Ensuring proper atmospheric control or using protective coatings is vital to prevent surface-related defects.
Inadequate Process Monitoring and Control:
Insufficient monitoring and control of process parameters, such as temperature, time, and cooling rates, can contribute to heat treatment defects. Lack of real-time monitoring, improper instrumentation, or human error can lead to deviations from the desired treatment conditions, resulting in defects.
Limited Knowledge and Expertise:
Heat treatment is a specialized field that requires a deep understanding of material science, thermodynamics, and process metallurgy. Limited knowledge or expertise in heat treatment practices can lead to improper process design, inadequate process optimization, and increased risk of defects.
Addressing these challenges requires a multidisciplinary approach, combining material science, process engineering, and quality control measures. Process optimization, robust process controls, adequate training, and continuous improvement initiatives are essential to minimize heat treatment defects and enhance the reliability of heat-treated components.