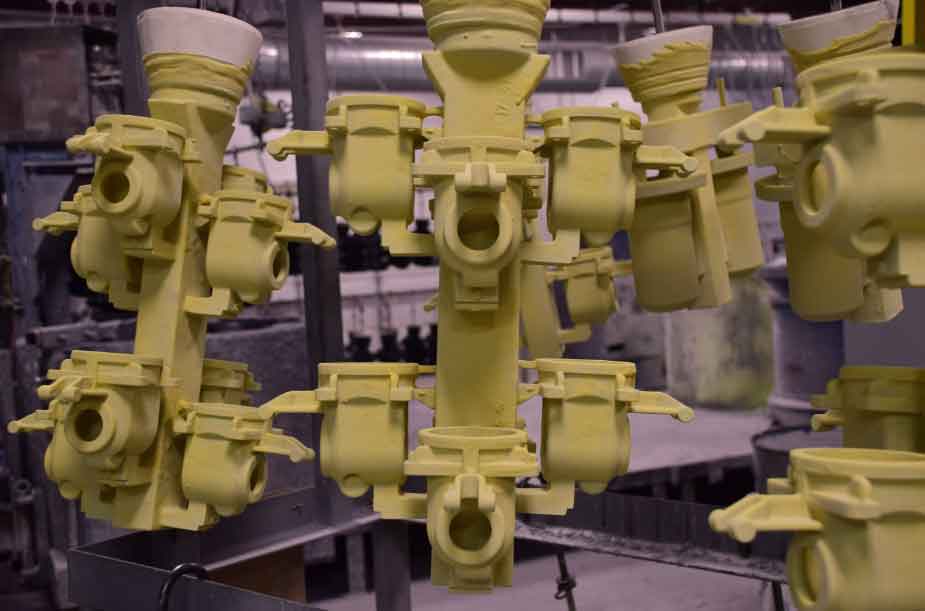
Investment casting, also known as lost-wax casting, is a versatile and precise casting method that unlocks a wide range of design possibilities for manufacturing complex metal components. It is widely used in industries such as aerospace, automotive, jewelry, and medical. Let’s take a comprehensive overview of investment casting and its potential in design:
1. Process Overview:
Investment casting involves the following steps:
- Pattern Creation: A wax or resin pattern is created using a mold or additive manufacturing techniques.
- Assembly: Multiple patterns are attached to a central wax sprue to create a cluster.
- Investment: The cluster is immersed in a ceramic slurry and coated with refractory material.
- Dewaxing: The ceramic shell is heated to remove the wax, leaving behind a cavity.
- Metal Pouring: Molten metal is poured into the ceramic shell to fill the cavity.
- Cooling and Solidification: The metal is allowed to cool and solidify.
- Shell Removal: The ceramic shell is broken or dissolved, revealing the cast metal component.
- Finishing: The casting is cleaned, finished, and any necessary post-processing operations are performed.
2. Design Advantages:
Investment casting offers several design advantages, including:
- Complex Geometries: Investment casting can produce parts with intricate geometries, thin walls, and complex internal features that are challenging to achieve using other casting methods.
- Near-Net Shape: The process enables the production of near-net shape components, reducing the need for extensive machining and material wastage.
- Intricate Details: Investment casting can capture intricate details, such as fine surface textures, lettering, and engraving, preserving the design intent.
- Variety of Materials: Investment casting supports a wide range of materials, including various metals and alloys, allowing designers to choose materials that meet specific performance requirements.
- Design Flexibility: The flexibility of wax or resin patterns allows for easy modifications and design iterations, enabling designers to refine and optimize their designs.
3. Precision and Accuracy:
Investment casting offers excellent dimensional accuracy and surface finish. The process allows for tight tolerances and minimal post-casting machining. This precision makes investment casting suitable for components with critical dimensions or intricate mating surfaces.
4. Versatility in Component Size and Complexity:
Investment casting can accommodate a wide range of component sizes, from small intricate parts to large and complex structures. It can produce components weighing just a few grams up to several hundred kilograms, offering versatility in meeting various design requirements.
5. Material Selection:
Investment casting supports a wide variety of materials, including stainless steel, carbon steel, tool steel, aluminum, titanium, and superalloys. This material versatility allows designers to select the optimal material for specific mechanical, thermal, or chemical properties required by the application.
6. Cost-Effectiveness:
Investment casting can be cost-effective, especially for producing complex components in medium to high volumes. The near-net shape capability reduces material waste, and the precision of the process reduces the need for extensive post-casting machining, resulting in cost savings.
7. Design for Manufacturability:
Design for manufacturability is critical in investment casting. Collaboration between designers and casting experts is crucial to optimize designs for mold filling, minimize casting defects, and ensure successful manufacturing.
8. Limitations:
Investment casting has a few limitations to consider:
- Size and Weight: Extremely large and heavy components may be challenging to produce using investment casting.
- Cost for Low-Volume Production: Investment casting can be cost-effective for medium to high volumes, but for low-volume production, the cost of tooling and setup may be relatively higher.
Investment casting unlocks a wide range of design possibilities, offering precise and complex components with excellent dimensional accuracy. By leveraging its design advantages,manufacturers can create intricate, near-net shape components with a high level of detail and accuracy. The versatility in material selection and the ability to produce components of various sizes and complexities make investment casting an attractive option for a wide range of industries and applications. With careful design considerations and collaboration with casting experts, investment casting can unlock innovative designs and bring complex concepts to reality.