V-method casting and gravity casting are two casting processes used for the production of metal parts. Let’s compare them based on various aspects:
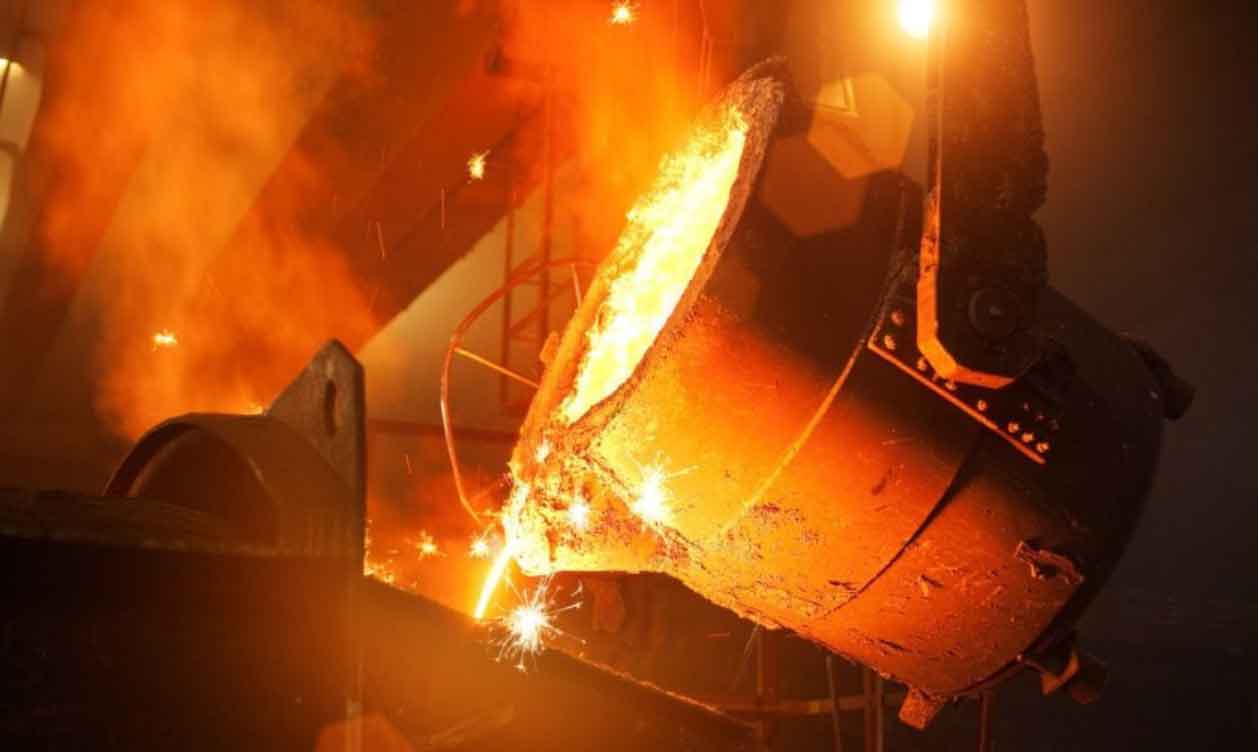
V-method Casting:
- Process: V-method casting, also known as vacuum molding, involves creating a mold using a vacuum-formed plastic film. The plastic film is heated and draped over a pattern to form the mold cavity, and molten metal is poured into the mold.
- Complexity: V-method casting is suitable for producing parts with moderate complexity and can replicate simpler to moderately complex geometries. It may have limitations in replicating intricate details compared to other casting methods.
- Surface Finish: V-method casting provides good surface finish, and the plastic film molds can yield relatively smooth surfaces on the cast parts.
- Material Options: V-method casting supports a wide range of materials, including both ferrous and non-ferrous alloys such as iron, steel, aluminum, and copper alloys.
- Flexibility: V-method casting offers flexibility in mold production as the plastic film molds can be easily and cost-effectively produced, modified, or replaced.
- Batch Production: V-method casting is suitable for small to medium production runs, making it ideal for customized or low to moderate production volumes.
Gravity Casting:
- Process: Gravity casting, also known as permanent mold casting, involves pouring molten metal into a reusable mold under the force of gravity. The mold, usually made of steel or cast iron, is designed to create the desired part shape.
- Complexity: Gravity casting is suitable for producing parts with relatively simpler geometries and moderate complexity. It may have limitations in replicating intricate details compared to other casting methods.
- Surface Finish: Gravity casting can provide a good surface finish, but it may require some post-processing to achieve a higher level of smoothness and refinement.
- Material Options: Gravity casting is commonly used for non-ferrous alloys such as aluminum, magnesium, and brass.
- Batch Production: Gravity casting is suitable for both small-scale and large-scale production runs. It allows for efficient production of parts in larger quantities compared to some other casting methods.
Advantages of V-method Casting:
- Capable of producing parts with moderate complexity.
- Good surface finish can be achieved with relatively smooth plastic film molds.
- Flexibility in mold production and cost-effective mold modifications or replacements.
- Suitable for small to medium production runs.
Disadvantages of V-method Casting:
- Limited in replicating intricate details compared to other casting methods.
- Slower production compared to certain casting methods like die casting.
- Increased labor and material costs associated with mold production and plastic film usage.
Advantages of Gravity Casting:
- Suitable for producing parts with relatively simpler geometries.
- Good surface finish can be achieved with some post-processing.
- Suitable for both small-scale and large-scale production runs.
- Efficient production process without the need for complex equipment.
Disadvantages of Gravity Casting:
- Limited in replicating intricate details compared to other casting methods.
- Material options are mainly focused on non-ferrous alloys.
- Requires careful mold design and gating system to ensure proper metal flow and fill.
When choosing between V-method casting and gravity casting, consider factors such as part complexity, surface finish requirements, material options, batch production needs, and cost considerations. V-method casting is suitable for parts with moderate complexity, while gravity casting is more suitable for simpler parts and larger production volumes. Consulting with casting experts or manufacturers can provide valuable insights into the suitability of each method for your specific application and help you make an informed decision.