The main stream of 3D printing of sand mold for end cover casting is selective laser sintering, layered solid manufacturing, melting deposition molding, and selective laser sintering scheme is adopted. Selective laser sintering adopts the structure required for laser sintering after each layer of sand is paved, and the unfired loose sand is poured out to obtain the sand mold. Resin sand is mainly used for 3D printing of end cover casting sand mold. Chinese researchers have tested and analyzed the pH value and viscosity index of resin and binder according to the main parameters, studied the relationship between the proportion of raw sand, binder, curing agent and sand mold performance, and the modification method of domestic resin. The compactness and permeability of sand mold printed by different types of equipment are different, and many scholars have also studied the hollowing optimization of sand mold structure.
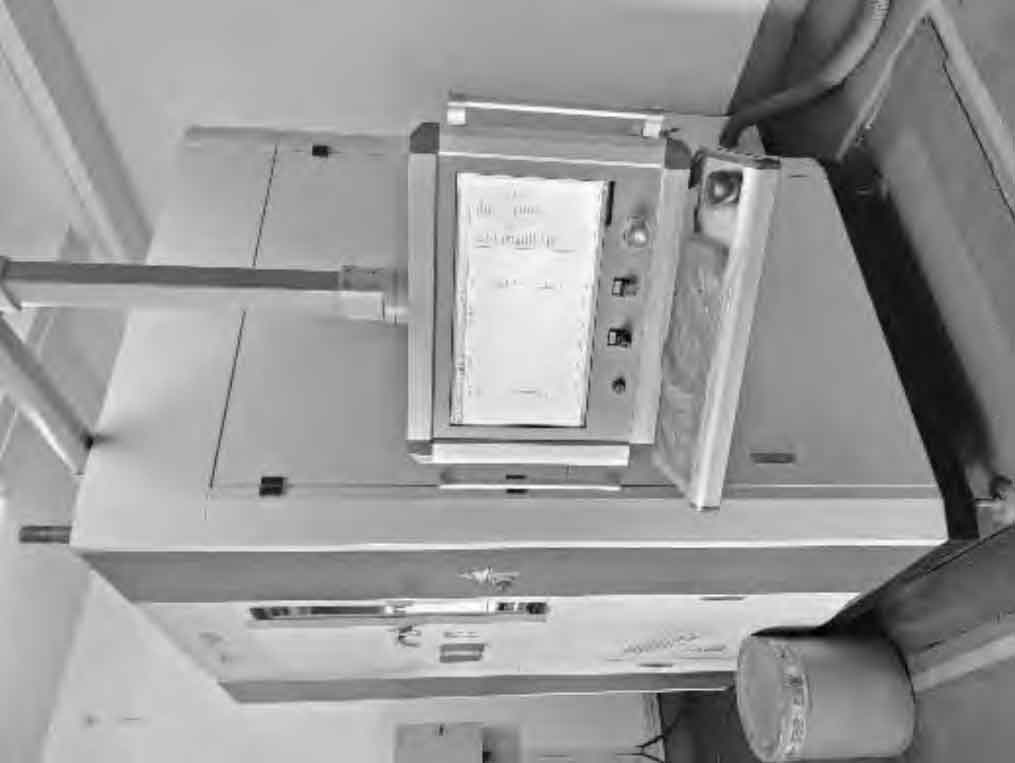
The model of sand 3D printing equipment is EP-C7250, as shown in Figure 1. The working mode is that the printer lays a layer of molding sand on the printing platform, and the laser sintering a layer of sand mold structure according to the path planned by the software, finally obtaining the solidified sand mold. The sand mold printed by the laser sintering printer needs to be dried to strengthen the strength of the sand mold, so there is a requirement that the sand mold structure can not appear thin wall and large area hanging. The inkjet printer does not need to be dried and can be sanded directly without parting.
The main work steps are as follows: use Magics software to lay out two sets of sand molds, the layout meets the requirements of rapid prototyping, and slice the end cover casting into 0.2mm per layer. The slice model is imported into EPHatch software, and the software generates the laser scanning path according to the structure of each layer. For the end cover casting to be supported, the laser scanning path of the supporting part can be set separately. Finally, the laser parameters are set to complete the laser scanning setting. Finally, set the printing device parameters through the device control software EPlus3D and execute printing. According to different requirements, the equipment can adjust the number of pre-laid powder layers before processing, the number of powder layers after processing, the powder laying temperature curve, the processing temperature curve, etc.

The maintenance of the equipment is simple, mainly to detect the connection status of the end cover casting, the molding sand is clean and free of sundries, and the sand humidity is normal, the sand is screened again, and the lens and temperature sensor are wiped. After starting the machine, apply sand first, manually lay sand to check the equipment status, and then prepare enough molding sand for printing. The comparison between modeling sand mold and 3D printing sand mold is shown in Figure 2. QT500-7 is used for pouring, and the cavity is filled for 1s at 1400 ℃, and the end cover casting is obtained after final cleaning.