ZHY casting once produced 750 large-scale nodular cast iron pump body for customers. Figure 1 shows the casting drawing. The overall dimension of the casting is about 4156 mm × 3915 mm × 685 mm, the main wall thickness is 75 mm, and the maximum wall thickness is 150 mm. The casting material grade is QT600-3, and the casting mass is 10190kg. Because the casting is a large piece, the technology is difficult. During the trial production, many pieces have been scrapped continuously, resulting in great economic loss. Later, through the analysis of defect causes, the casting process was improved. The above defect problems were solved, and the casting quality completely met the customer’s requirements.
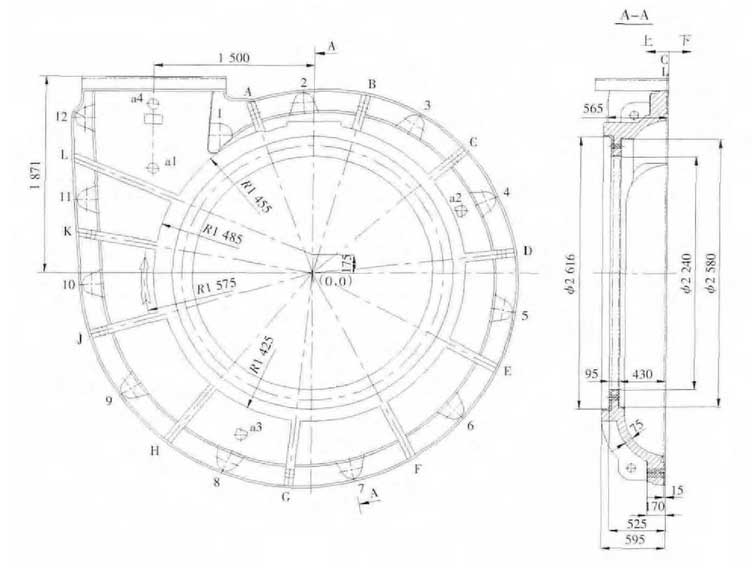
1.Casting process
Figure 2 shows the original casting process: the casting is placed horizontally, the inner cavity is downward, and the parting surface is set at the bottom of the casting; the casting is provided with an annular cross sprue, and the molten iron enters the cavity through 12 internal sprues; the internal sprue size is 50 / 54 mm × 14 mm, and the total cross-sectional area of the internal sprue is 87.36 cm2; the cross-sectional area is 65 / 75 mm × 100 mm, and the total cross-sectional area is 140 cm2; the diameter of the direct sprue is 120 mm, and the cross-sectional area is 113 cm2; The ratio of sprue cross-sectional area is Σ f in Σ f cross Σ f straight = 1:1.6:1.29. Four open risers are set at the top of the casting, with the diameter of 220 mm; the diameter of riser neck is 75 mm; the thick wall part of the casting is laid with cold iron, as shown in Figure 2.
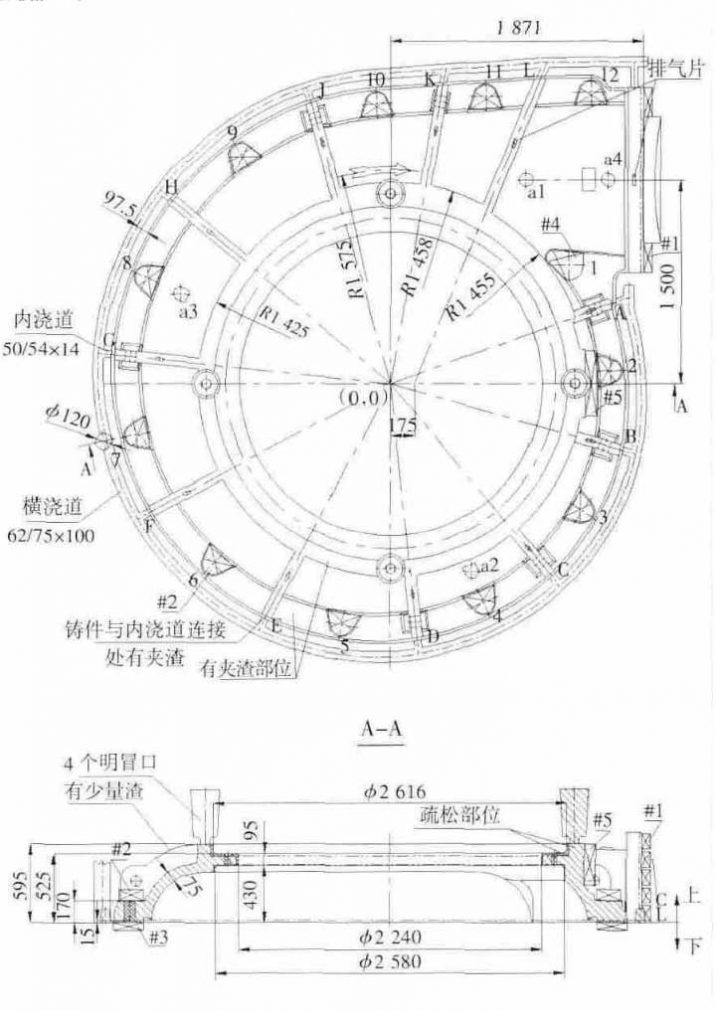
2 Sand mix
Furan resin sand is used for molding, the ingredients are: xy90-2 furan resin, adding amount is 1.1%; xy-gsy sulfonic acid curing agent, adding amount is determined by sand temperature; Fujian sea sand, particle size is 40 / 70 mesh.
3 Smelting and pouring process
Medium frequency induction furnace is adopted for smelting, and the chemical composition of molten iron is controlled as shown in Table 1. The charge ratio is 40% Q10 Benxi pig iron + 30% ordinary carbon steel scrap + 30% nodular iron. The amount of Si Fe, Mn Fe and electrolytic Cu added is adjusted according to the requirements of the original molten iron.
The spheroidizing treatment adopts the flushing process, adopts the dyke type spheroidizing treatment package, puts the spheroidizing agent into one side of the dyke and the molten iron into the other side, adopts the z-ii spheroidizing agent of Wuxi Yongxin Special Metal Co., Ltd., and selects the ා 2 spheroidizing agent.
The addition amount of spheroidizing agent is 1.3%, and the spheroidizing agent is covered with 10 ~ 20 mm Fe Si 75 particles (the addition amount is 0.2%). The surface is covered with a layer of machined iron chips to delay the reaction time of spheroidizer. The spheroidizing temperature is 1 450 ℃. The inoculation process is as follows: when the liquid iron reaches 2 / 3, 0.7% BS-1 inoculant (including Ba and CA) is added gradually.
By using the above technology, the pouring temperature was changed many times (1300-1380 ℃), and the results of trial production showed that the bottom of riser and the joint of thick wall had serious shrinkage and porosity defects, and there were slag inclusions on the top of casting.
As the riser used in the original process did not play the role of feeding, but caused shrinkage and porosity, so all the risers were cancelled and replaced with 8 flaky vent plates, which were still located at the hot spot on the top of the casting. The thickness of the inner runner shall be appropriately thinned, and the size shall be changed to 12 runner 100 / 125 mm × 7 mm (cross section area is 12 × 7.875 = 94.5 cm2). The size and laying position of the cold iron shall not be changed, as shown in Figure 3. Molding sand, smelting burden, smelting, spheroidizing treatment and inoculation treatment have not changed.
The results show that the defects of shrinkage cavity, porosity and slag inclusion have been eliminated.