Niyama criterion is selected as the prediction method of shrinkage porosity of spiral bevel gear casting. As shown in figures (a) and (b), there is a high probability of shrinkage casting defects at the geometric edges and corners of the casting. The residual melt modulus is set as the casting defect parameter as the prediction method of shrinkage cavity of gear steel castings; Figures (c) and (d) show the distribution of shrinkage casting defects. Although the filling process of molten metal of the casting is not stable, the strong feeding capacity of the insulation riser ensures that the shrinkage casting defects are moved to the riser area, and the casting has no shrinkage casting defects. Figures (E) and (f) show the distribution of air pressure at the section of pouring and riser; As shown in the figure, there are different degrees of air residues inside the riser and in the center of the casting, which indicates that the flow of liquid metal is too violent, resulting in part of the air in the mold cavity being drawn into the liquid metal, which is very easy to cause casting defects.
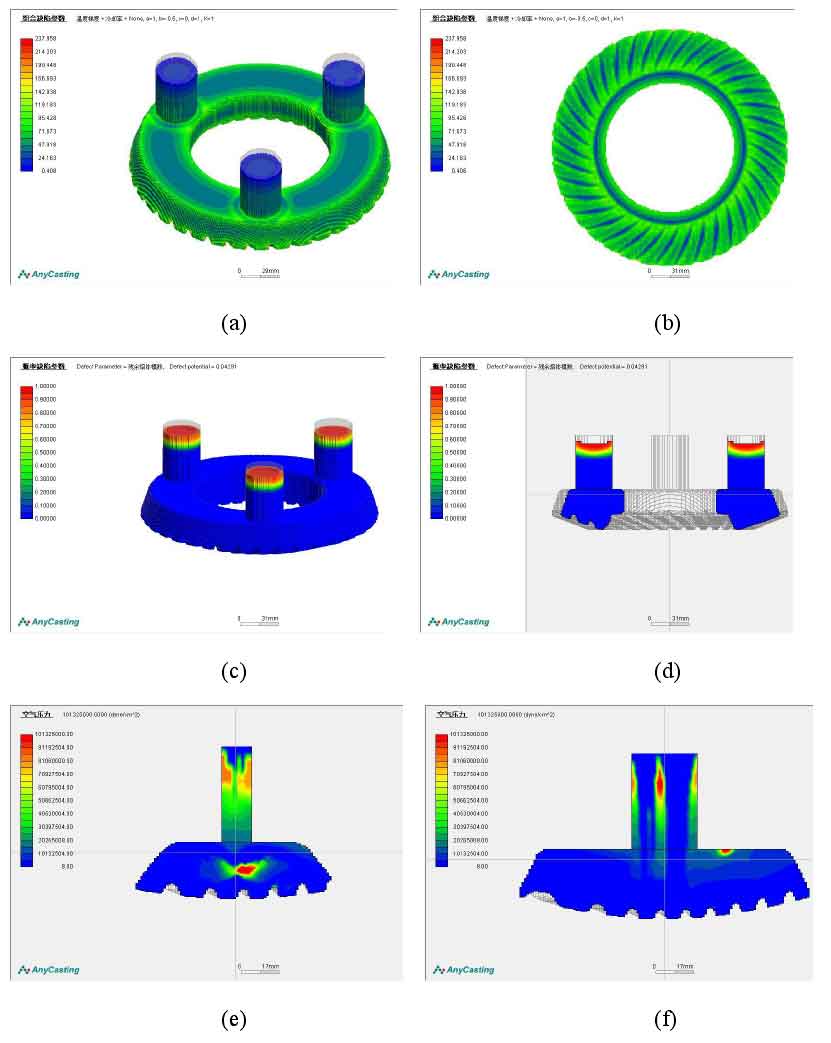
Comparing the numerical simulation results of the two pouring schemes, it can be seen that the casting with common Pouring Scheme of pouring riser has a violent flow of liquid metal in the mold cavity due to the lack of buffer and deceleration effect of liquid metal in the pouring system; The mold filling speed is too fast, which seriously affects the casting forming process. The metal liquid poured from the gate directly washes the inner wall of the mold cavity, and the mold filling is not completed at the same time. Local metal liquid has no time to discharge gas and slag, which is very easy to produce casting defects; There are different degrees of air distribution on the upper surface and the center of the casting, which will cause major hidden dangers to the quality and service performance of the casting. In contrast, although the molding of scheme I adopting the central top injection pouring scheme is complex, the mold filling process is stable and orderly, the riser feeding effect is ideal, the castings solidify in sequence, and the possible porosity casting defects on the upper surface can be eliminated by increasing the machining allowance on the upper surface and adjusting process parameters. There are no obvious casting defects in the interior and tooth surface of gear blank castings.