During the mold filling process of dual liquid bimetallic lost foam composite casting, as shown in Figure 1, the high chromium cast iron liquid poured first will burn most of the foam in advance, including the volume of carbon steel. Within the 75 second interval of waiting for the surface of high chromium cast iron to solidify without pouring carbon steel, there is almost an empty mold cavity above the high chromium cast iron, Whether the coating and molding sand can not move to the cavity space is the key factor to determine the success or failure of lost foam casting. The following focuses on the feasibility conditions of the process.
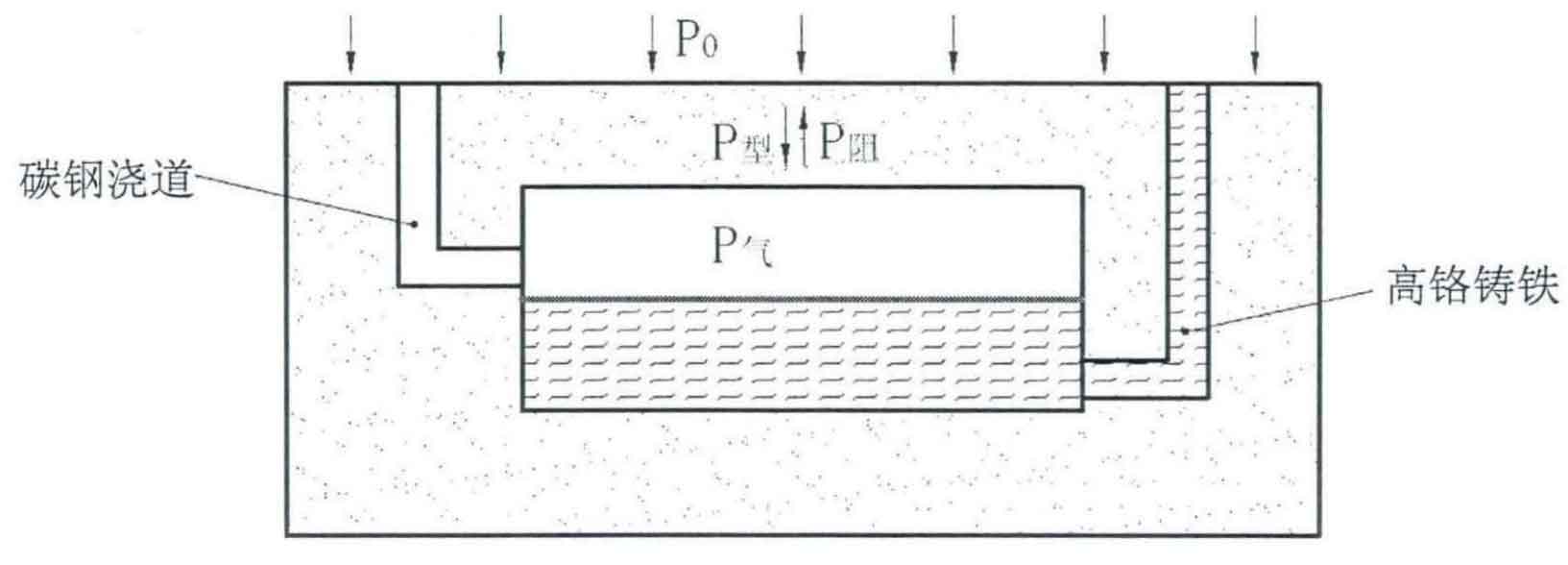
1) According to the analysis of figure 2A based on the bulk mechanics, in order to avoid collapsing the box towards the cavity side, the stress relationship must meet the following formula:

Deformation of the formula:

2) According to the analysis of figure 2B, in order to avoid the box collapsing to the side of the mold cavity, the stress relationship must meet the following formula. The formula shows that the decisive factor to ensure that the molding sand at the top of the mold does not flow to the mold cavity is still the need to provide sufficient P resistance, whether it is in the process of high chromium cast iron pouring or after pouring.
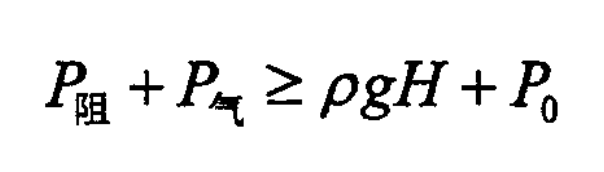
To sum up, the key condition to avoid box collapse at the top and side of the mold during the process of casting or after the completion of Pan casting is that the whole mold provides enough P resistance, and the vacuum pumping of the mold is not important. However, the reduction of vacuum degree in actual casting will indeed lead to box collapse. Why? It is found from group P that the resistance per unit area of the coating layer and molding sand when moving is jointly determined by the strength of the coating layer and the compactness of the molding sand, and the compactness of the molding sand can be increased by increasing the vacuum degree. Therefore, in order to ensure that there is no box collapse in the process of bimetal liquid lost foam casting composite casting, in addition to vacuum pumping process measures, 2-3mm thick high-strength coating layer is used to further increase the P resistance.
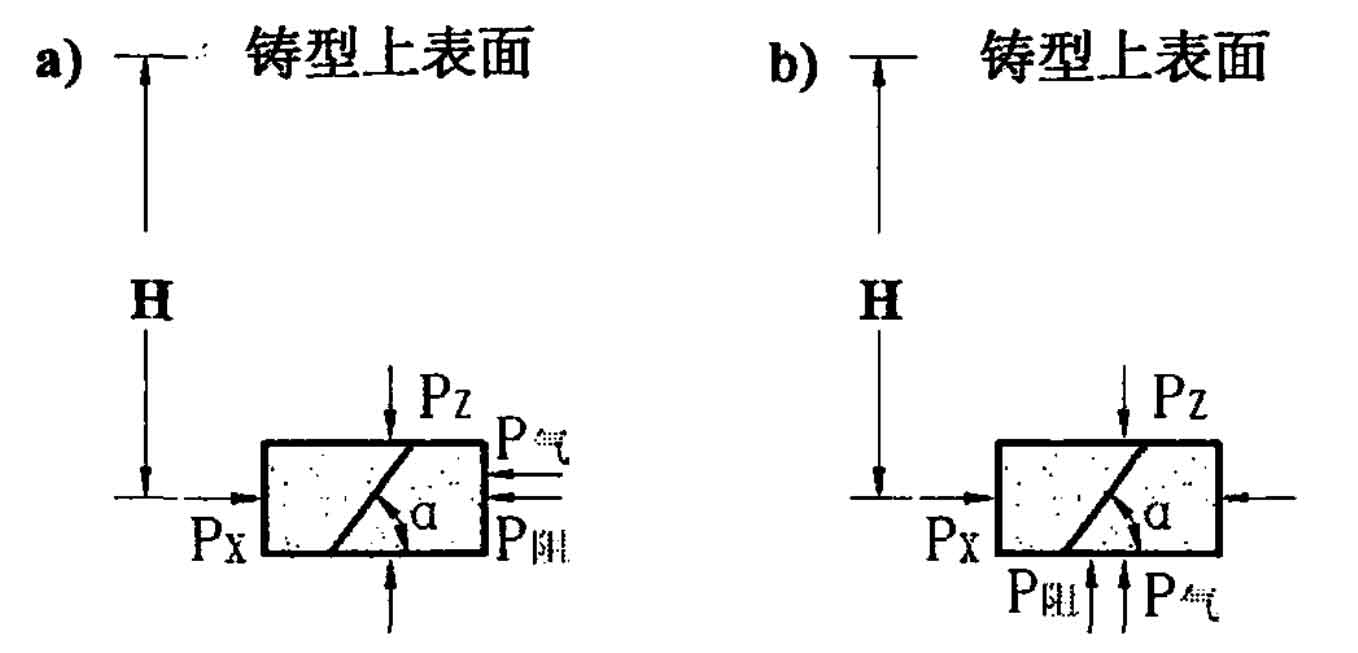