1. Tendency shrinkage defects of gray iron castings after processing
In the process of design and development of gray iron castings, due to its special material requirements, a certain amount of alloy materials need to be added when melting molten iron to meet its performance requirements, and the whole structure and alloy shrinkage tendency are different from ordinary gray iron castings. The main wall thickness of gray iron castings is 15 mm, the maximum section thickness is 120 mm, and the wall thickness is seriously uneven, resulting in different cooling rates at various parts of gray iron castings. In the early stage of process design, Due to the insufficient evaluation of the casting risk of gray iron castings, tendency defects appeared in the three connecting holes of gray iron castings after processing, and statistics found that many defects were located in the direction of 4 and 7 points of the small holes (as shown in Figure 1), which had obvious tendency and regularity. Due to the particularity of the use of engine gray iron castings, the frame will be scrapped and serious economic losses will be caused when the internal tendency defects cannot be repaired.
2. Defect type determination
Generally, due to regional and information exchange restrictions, defect types cannot be effectively identified only through defect photos provided by customers. In order to effectively identify the types of defects, the physical objects of gray cast iron castings were destructively dissected at the same position fed back by the customer, and penetrant testing was carried out. Defects were found in the same area. Macroscopic metallographic examination was carried out on the defects, and holes were found on the corresponding interface (as shown in Figure 2); Through the sampling of the body of the defect part and the inspection under the microscope with a magnification of 100 times, the results show that the defect is in an irregular tearing hole shape, and the defect surface is not smooth, in an irregular serrated shape (as shown in Figure 3). Combined with the analysis of the structure of gray iron castings and the original casting process, the defect area is close to the hot spot of the inner runner, which belongs to the final solidification area, and the thin and thick walls of this part of the gray iron castings structure intersect. After pouring, the liquid shrinkage and solidification shrinkage of this part are greater than its solid shrinkage in the solidification shrinkage process, and the small holes caused by the difference between the two cannot be supplemented by external molten iron, forming small shrinkage holes, so it is determined to belong to shrinkage defects.
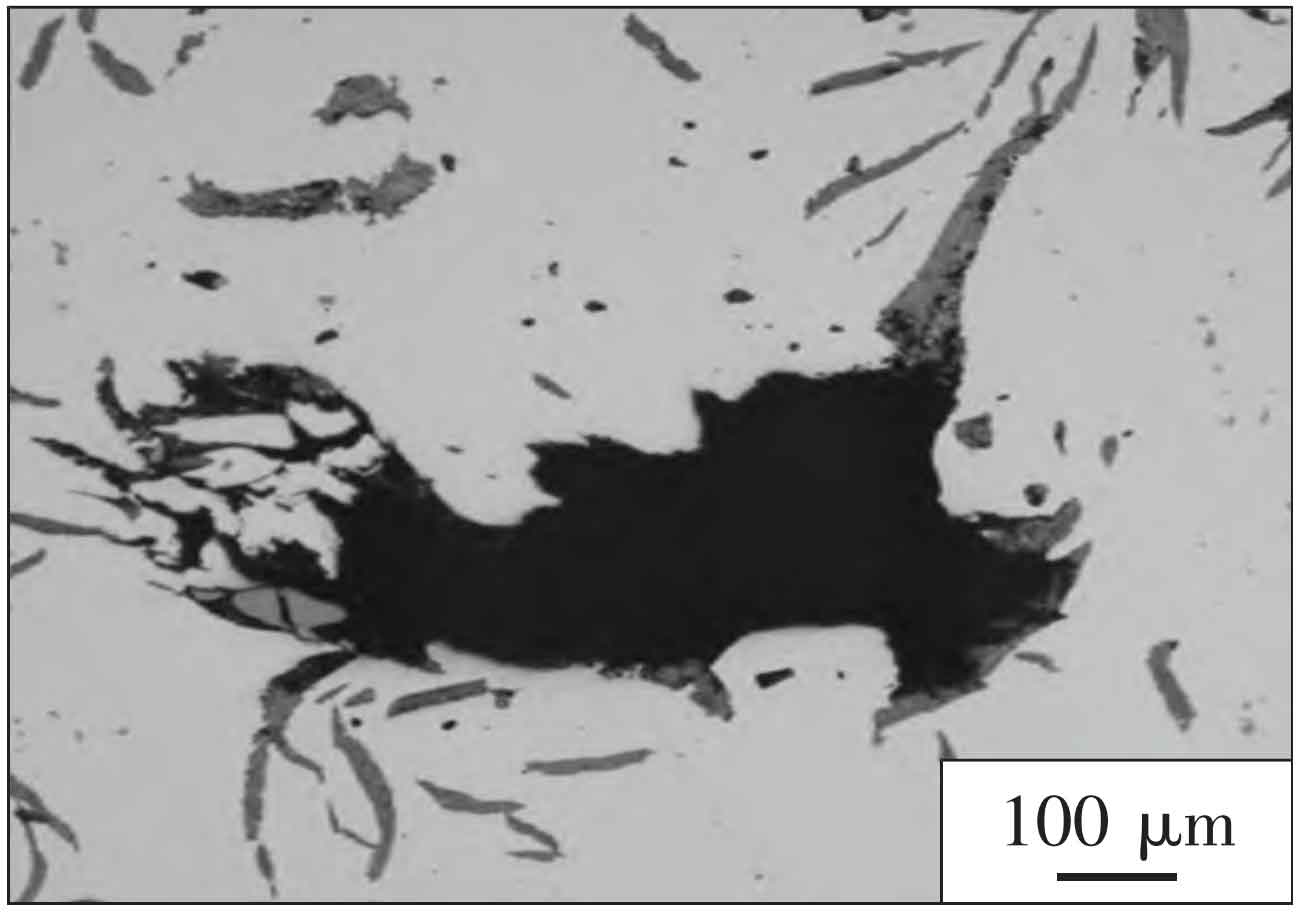