By analyzing the influence of the solidification mode of molten metal on the quality of sand castings, the solidification front of the layer-by-layer solidification mode is in direct contact with the solution, and the volume shrinkage occurs when the metal changes from liquid to solid, which directly affects the supply of molten metal. Therefore, the tendency of shrinkage porosity is very small, and the shrinkage cavity is formed at the final solidification position; It is necessary to add a riser to feed the flywheel sand mold casting in liquid state. With the help of design experience and relevant information, the dark riser is directly connected with the feeding channel to reduce the cooling speed of the channel. The riser is located at the end of the transverse runner.
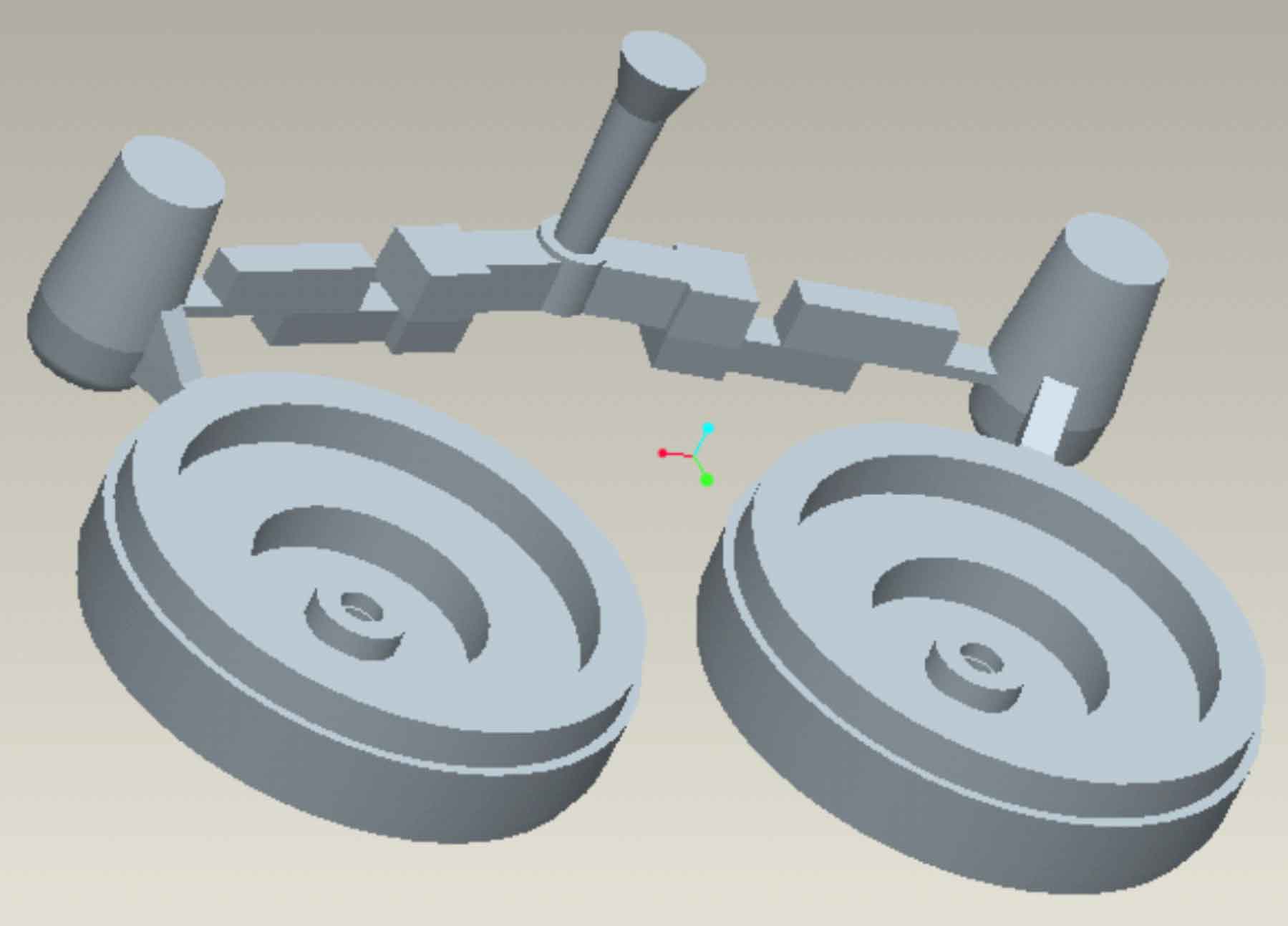
The dimensions of the pouring system are as follows: the sectional area of the sprue is 1800mm ^ 2, and the height is 180mm; The cross runner area is 1130mm ^ 2, the total length is 206mm, the sectional area of the riser bottom is 3600mm, and the height is 120mm. The entity diagram of the improved scheme is shown in Figure 1.
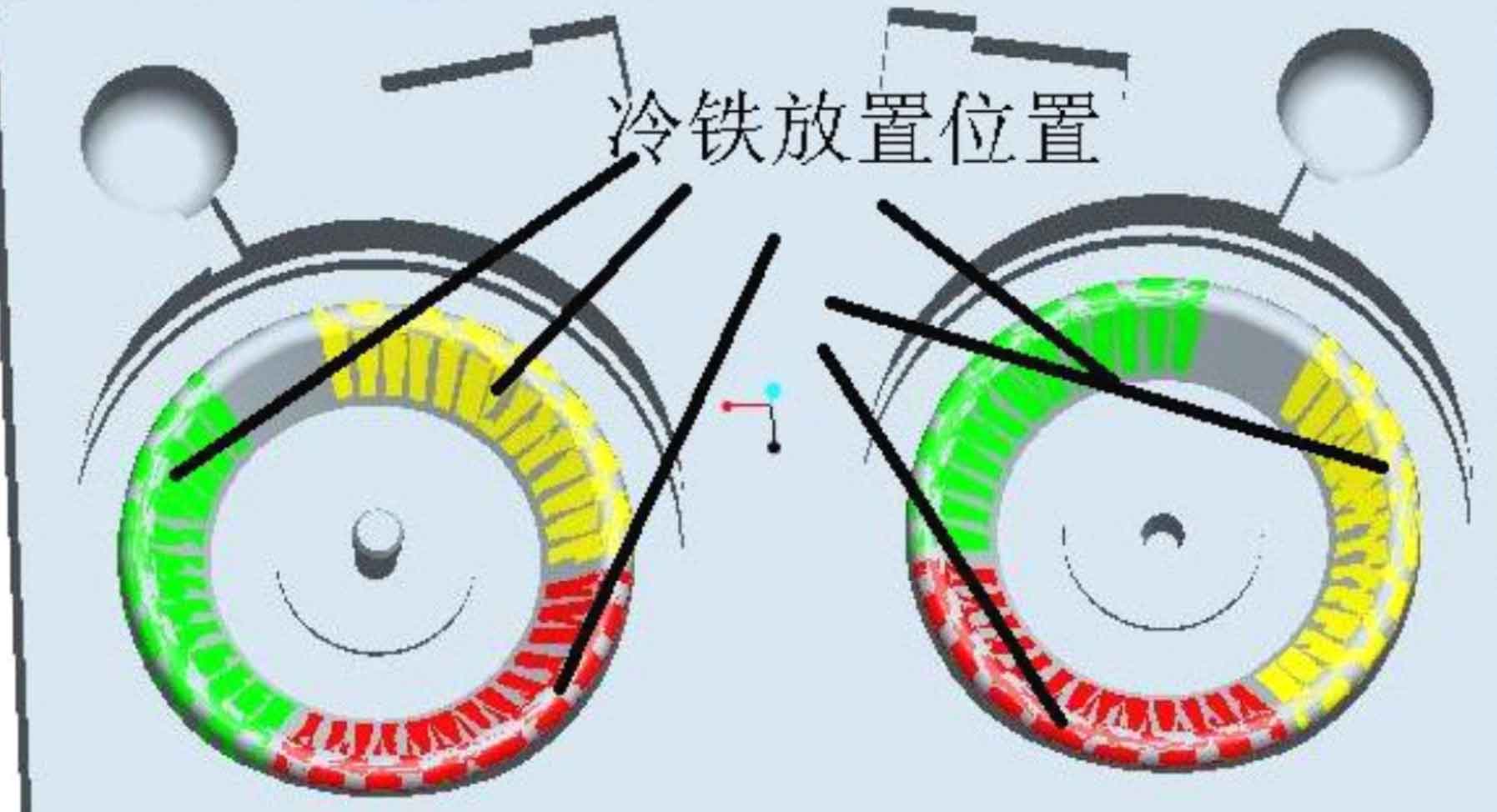
Considering that the overall size of the flywheel is large and the transition part of the step is thick, it is necessary to place three fan-shaped chills (the chills are not placed at the place leading to the inner runner). Through the chilling effect of the chills, the shrinkage porosity and shrinkage hole of the sand casting are transferred to the riser during the layer-by-layer solidification process. The placement of cold iron in the sand mold is shown in Figure 2.