1 Scheme design
(1) The horizontal parting resin sand molding and bottom pouring scheme are adopted, as shown in Figure 1. The open gating system is adopted, and the runner area ZF: ZFw: ZFh=1:1.5:1.25; The inner diameter of the sprue is 80mm ceramic pipe, and the refractory bricks are placed at the bottom to prevent the molten iron directly impacting the sand mold, which causes the bottom of the sand washing cross runner to be set with four 120mmx120mmx20mm foam ceramic filter screen inner runners, which are connected to the bottom of the sand casting through the collecting tank at the bottom of the filter screen with ceramic pipes, so as to ensure the purity of the molten iron and smoothly enter the mold cavity, effectively preventing sand inclusion and slag inclusion in the sand casting, as shown in Figure 2.
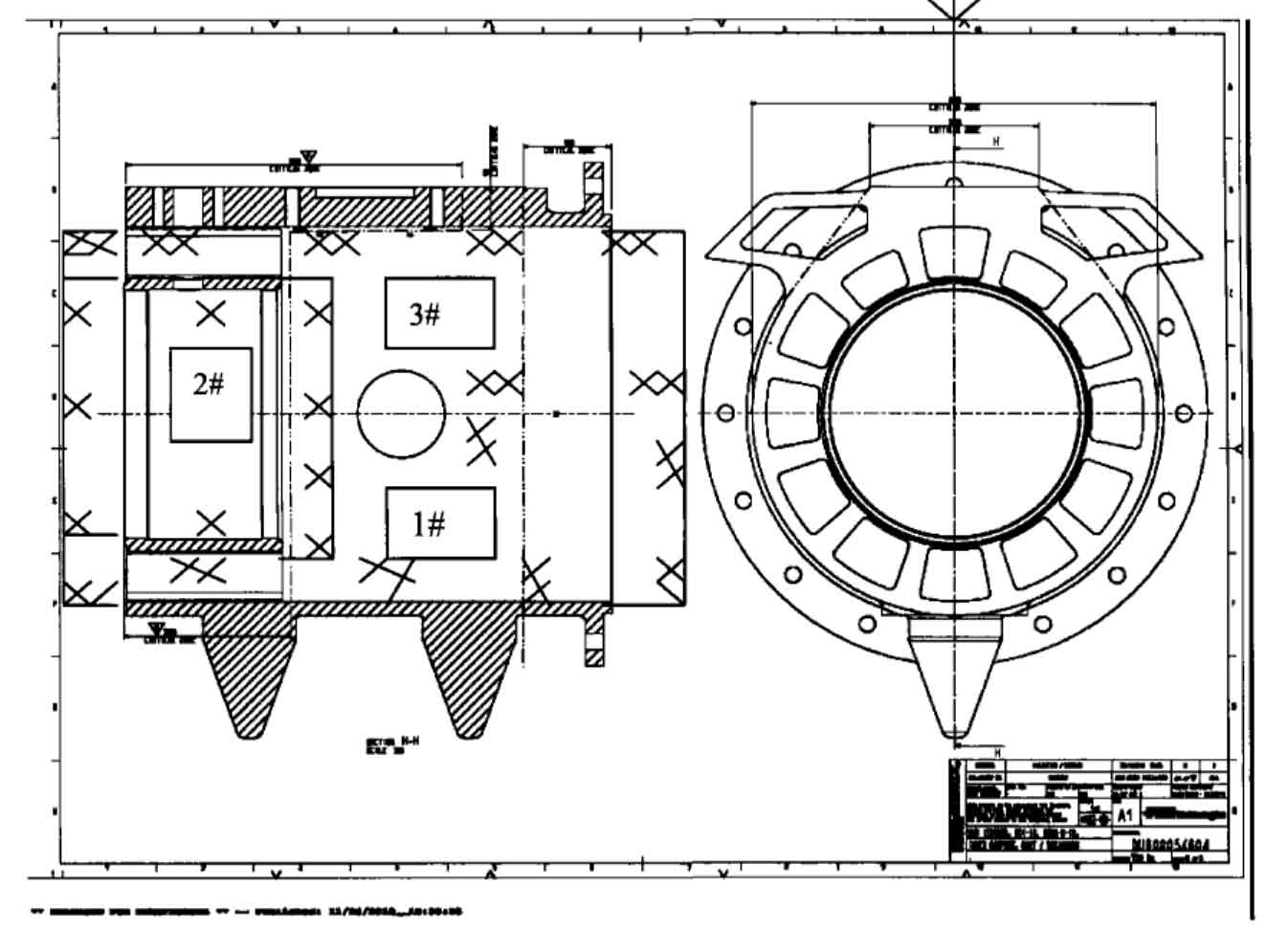
(2) Size of sand box: 1500mmx1500mmx600mm/600mm, welded with 20mm thick steel plate to ensure that the sand box has enough rigidity to resist the pressure generated by graphitization expansion, and create necessary conditions for riser-free sand casting.
(3) The maximum wall thickness of the two conical support feet is 160mm, which is very easy to produce shrinkage defects, which makes it impossible to meet the requirements of ultrasonic testing. The formed chill iron is placed at this part for chilling to ensure balanced solidification, and the residual water at the chill iron part is dried with gas before the box is closed to avoid gas holes at the chill iron part. The cold iron shall be shot cleaned by shot blasting machine before use without moisture and rust. (4) P120mm steel pipe is used in the middle of the sand core to strengthen and vent the air around the pipe.
(5) Place four D20mm air outlets on the upper mold (see Figure 2), and use the graphitization expansion principle to cancel the feeding riser to improve the process yield.
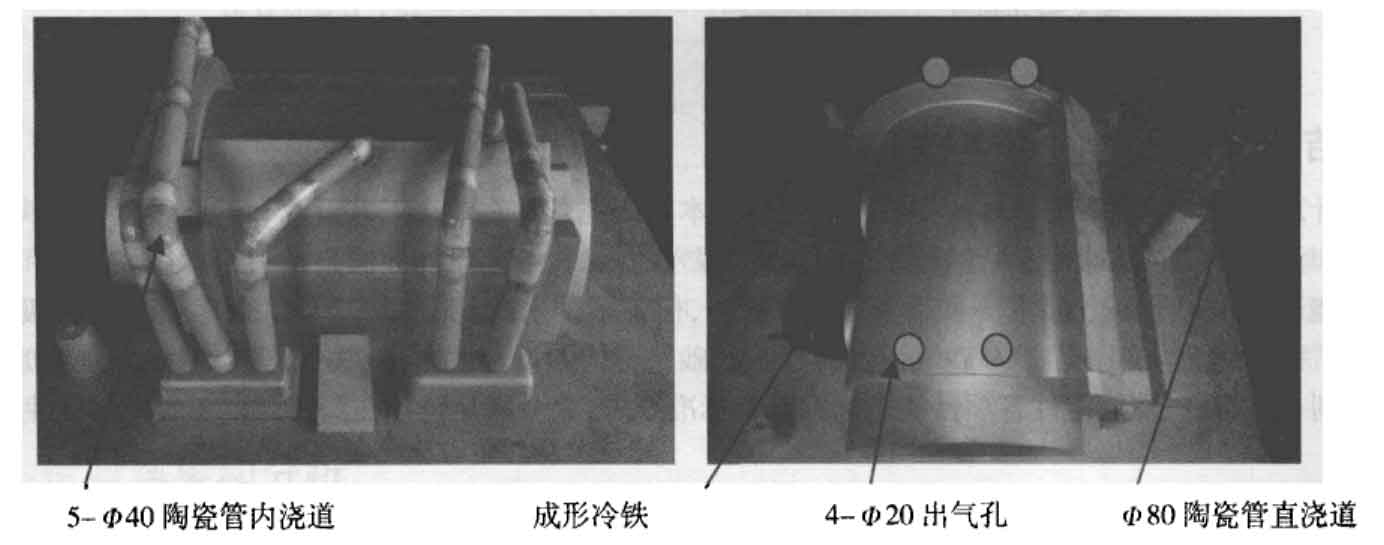
2.Melting and pouring process
(1) Selection of raw materials. Use Benxi 010 or 012 low PSMn high-quality pig iron scrap produced by the company to focus on controlling MmPS and Ti_ Cr. CuPb and other trace elements, adjust the carbon content with low sulfur high-quality carburetor.
(2) The composition after furnace shall be C3.60%~3.70% Si185% – 2.15%, Mn<0.20% P<0.40% S<0.01% Mg (residual 0.035%~0.05%), which shall be controlled at the lower limit as far as possible under the condition of ensuring spheroidization.
(3) Spheroidizing treatment temperature: 1430~1460 Spheroidizing agent dosage: 1.0%~1.15% After spheroidizing, slag removal and re-transfer for a inoculation treatment of 0.3%~0.4%.
(4) Pouring temperature: 1330~1350C. During pouring, special inoculant with particle size of 0.~1mm and ratio of 0.1%~0.15% is used for stream inoculation. During pouring, ensure that the gating cup is in 2/3 full state, and ensure the continuity of molten iron flow to avoid gas and inclusion being drawn into the mold cavity and the generation of cold shuts.
3.Test results
(1) Tensile strength: 410 MPa, yield strength: 250 MPa, elongation: 24%, Brinell hardness HB: 135.
(2) Spheroidization rate: 95%, graphite size; Grade 6, ferrite 98%, as shown in Figure 3
(3) – 20C low temperature impact value: 14J16J15, average 15J.
(4) The sound speed is 5670m/s, and no recordable defects are found through magnetic particle and ultrasonic testing.
(5) The appearance of sand casting is flat and smooth, as shown in Figure 4. There are no sand mold casting defects such as sand inclusion, slag inclusion and cold shut, and the dimensional accuracy meets the technical requirements.
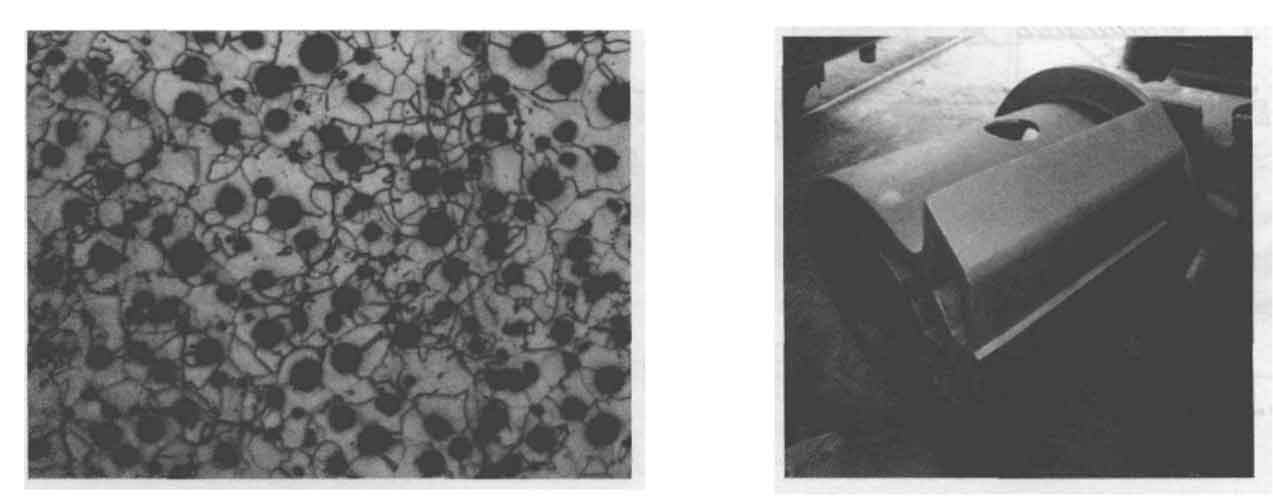