The optimal process parameter combination of lost foam casting valve body is simulated by ProCAST software, and the other parameters and conditions remain unchanged. During the optimization of response surface test, the optimal process parameters were properly corrected and rounded. Finally, the pouring temperature was 1576 ℃, the vacuum degree was 0.04 MPa, the pouring speed was 104 mm/s, and the corresponding hot crack index was 0.010 74, which was consistent with the predicted value of 0.010 11. The simulation results of molten steel filling process under the optimal process parameters are shown in Figure 1. From the simulation results, it can be seen that the reasonable vacuum setting makes the whole filling process continuous and stable, and it is not easy to produce casting defects such as cold shut and insufficient pouring.
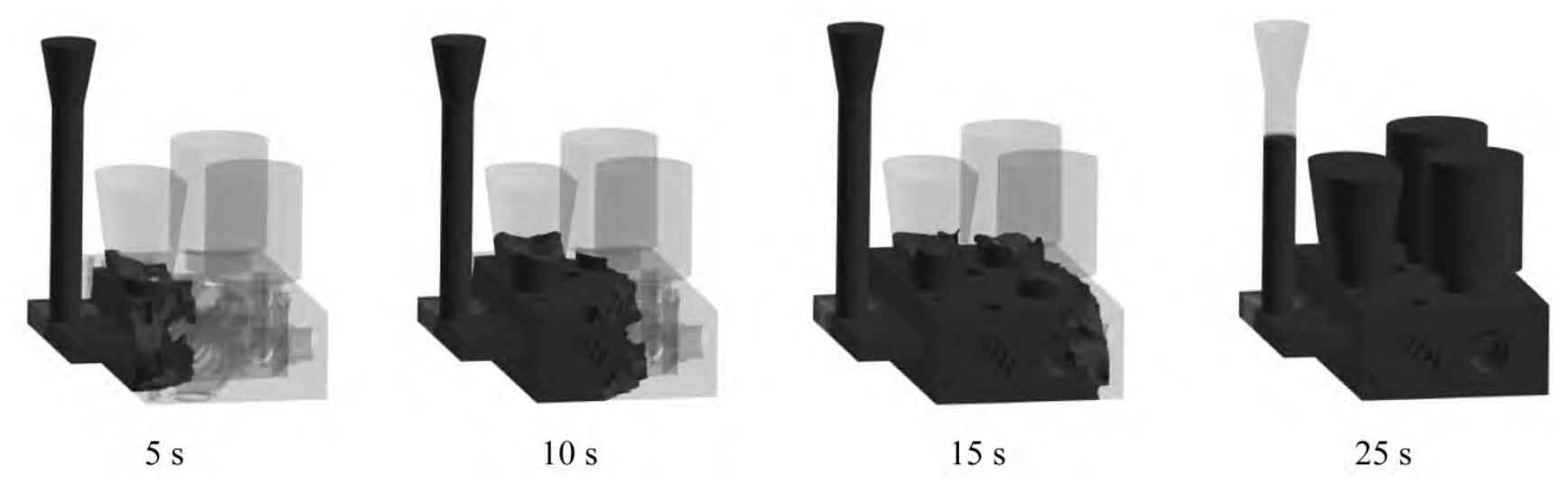
The temperature field during the solidification process of the valve body under the optimal process parameters is shown in Figure 2. In the early stage of solidification, because the pouring system is small and relatively uniform, the pouring system solidification is fast. When the solidification rate is 22.3%, a small part of the molten steel temperature of the transverse runner has been below the solidus temperature, and most of it is still above the liquidus. When the solidification rate reaches 50.1%, the riser temperature above the lost foam casting is still higher than the liquidus temperature, so as to ensure the feeding of the lost foam casting, and the casting near the riser and the inner runner area begins to slowly solidify. When the solidification rate reaches 80.7%, most of the surface of the lost foam casting has been solidified, the internal solidification state of the lost foam casting is good, there is no isolated liquid phase zone, the riser part has not been completely solidified, and the lost foam casting continues to be fed. As the temperature decreases, the viscosity of molten steel gradually increases and the fluidity decreases. The gating system, valve body lost foam casting and riser all solidify, and the molten metal no longer has fluidity.
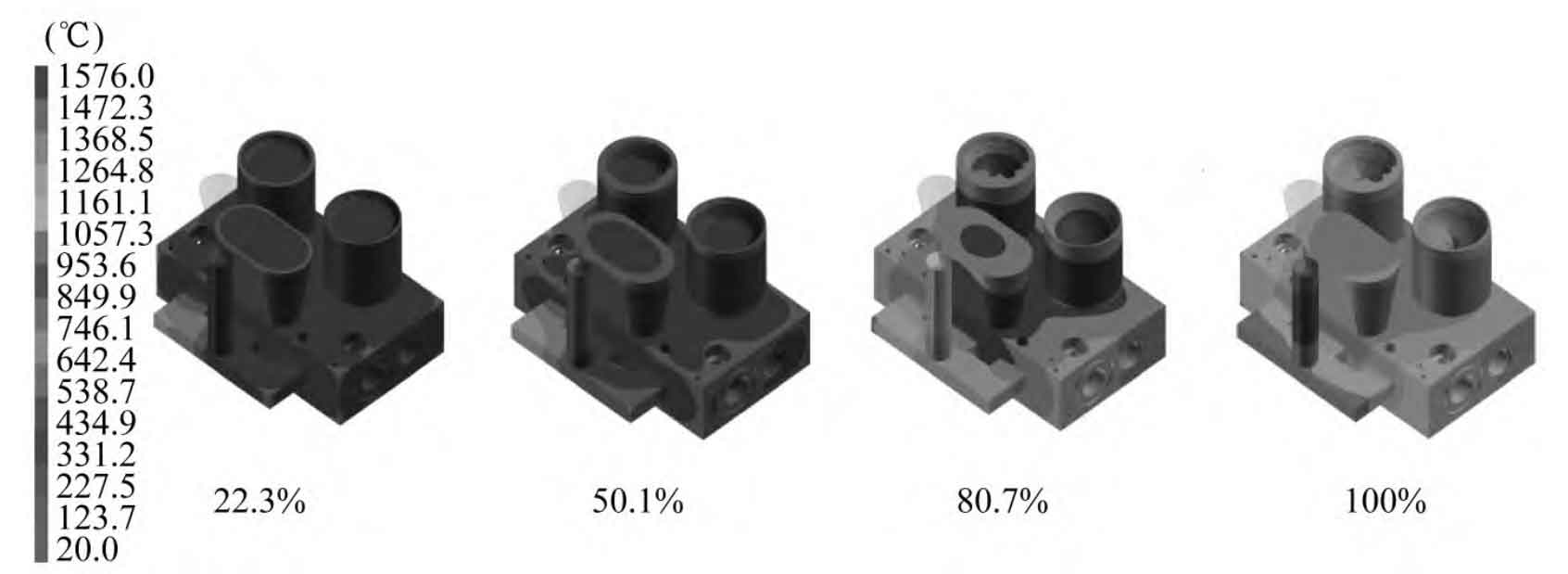
The distribution of shrinkage porosity and shrinkage cavity under the optimal process parameter combination is not left in the lost foam casting. Due to the high temperature and slow cooling of the riser material, the shrinkage porosity and shrinkage cavity are finally left in the riser, which shows that the design can effectively eliminate the shrinkage porosity and shrinkage cavity casting defects while meeting the hot crack prediction.