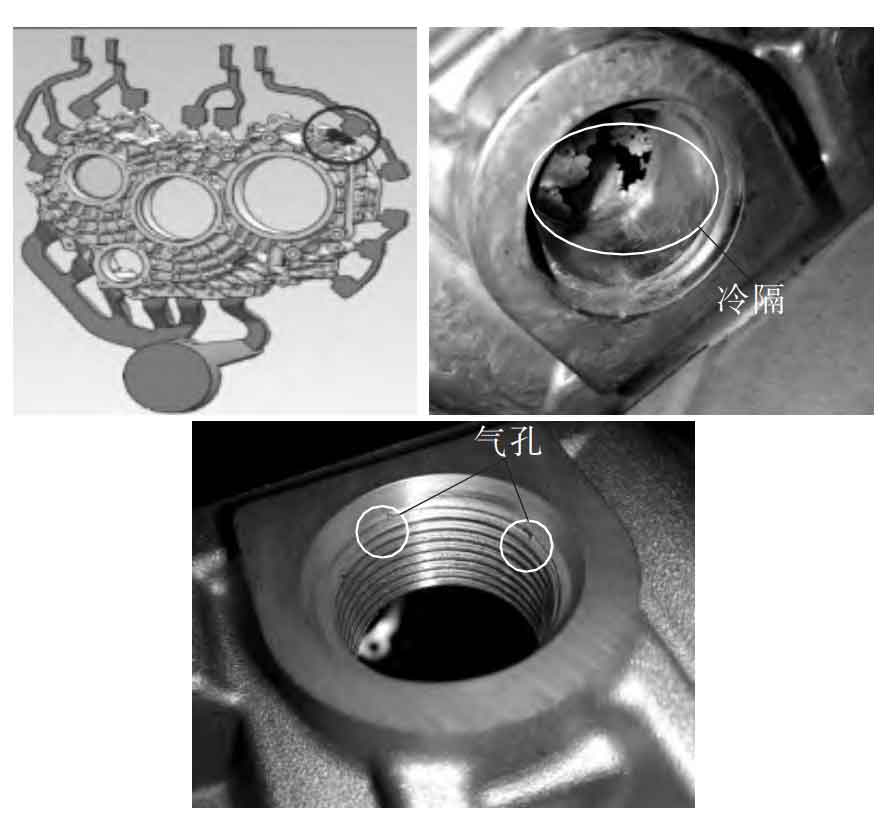
The cold shut defect was found at the oil hole at the far end of the die casting part, and the air hole defect was found after machining, as shown in Figure 1. Track the qualification rate of three batches of die castings, as shown in the table. It can be seen from the table that the cold shut and porosity defects at the far end of the blank are very serious, which seriously affect the product qualification rate.
Product batch | Product No | Number of qualified pieces | Cold shut at blank oil plugging hole/piece | Air hole at oil plug hole after machining/piece | Pass rate/% |
The first batch | 10647017-3 | 126 | 15 | 0 | 89.4 |
The second batch | 10647017-3 | 224 | 155 | 15 | 56.9 |
The third batch | 10647017-3 | 582 | 180 | 49 | 71.8 |
The causes of defects such as blowholes and cold shuts in local areas of die castings were simulated and analyzed by MAGMA software:
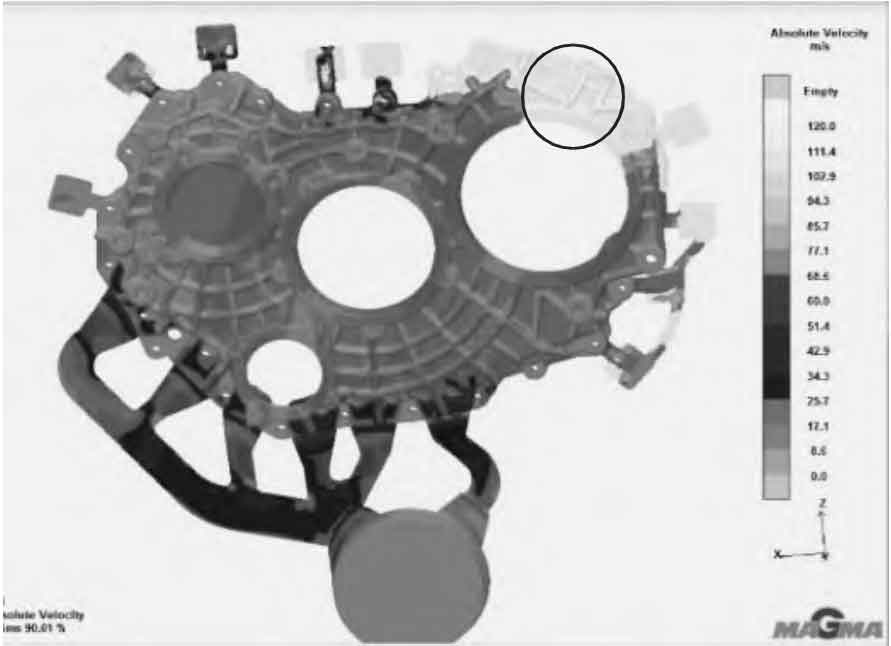
1) MAGMA software was used to simulate the filling process of molten aluminum. Due to the non-uniform wall thickness of the die casting parts, in order to ensure the accuracy of the results, the variable mesh division method was used to divide the three-dimensional mesh of the die casting parts. It was found that the product was finally filled at the end of the filling at the oil plugging hole during the die casting process. It can be judged that the cold material, gas and slag are easy to converge at the oil plugging hole, resulting in cold shut and air hole defects, as shown in Figure 2.
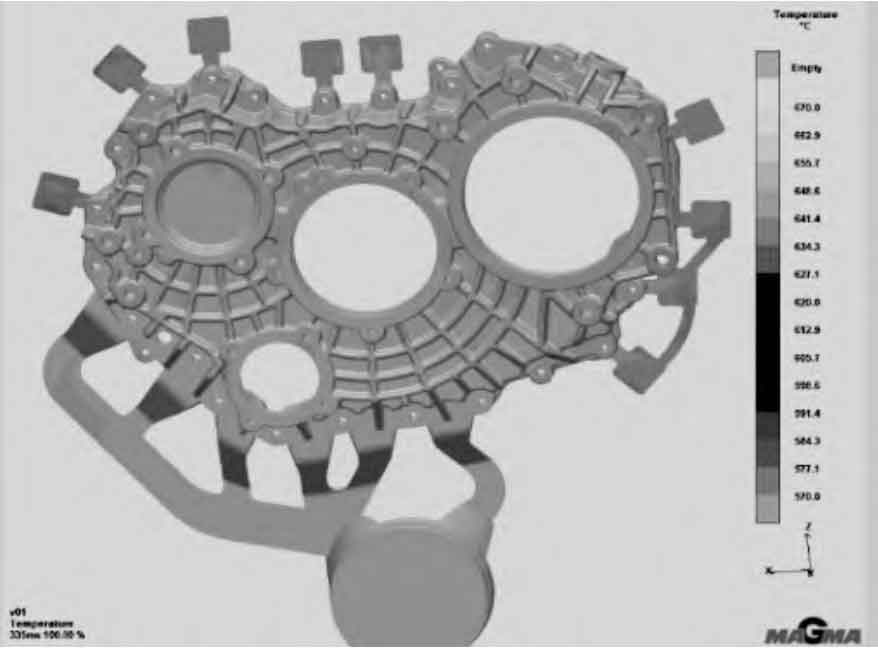
2) The area of cold shut defect is found at the forming end of die casting products by using MAGMA software simulation. Due to the long travel of molten aluminum and large heat loss, the cold shut in this area is serious, and the mold temperature is low far from the gate, so it is easy to produce cold shut defects, as shown in Figure 3 and Figure 4.
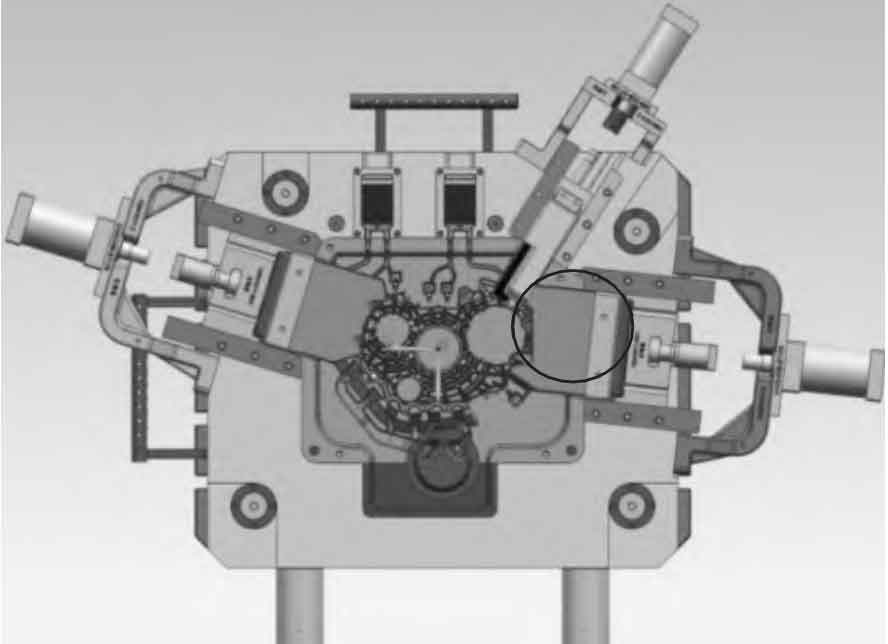