Casting simulation has become an integral part of the modern foundry industry. This innovative technology has the potential to predict potential casting defects, enabling proactive preventative measures. This article explores the role of simulation in predicting and preventing casting defects.
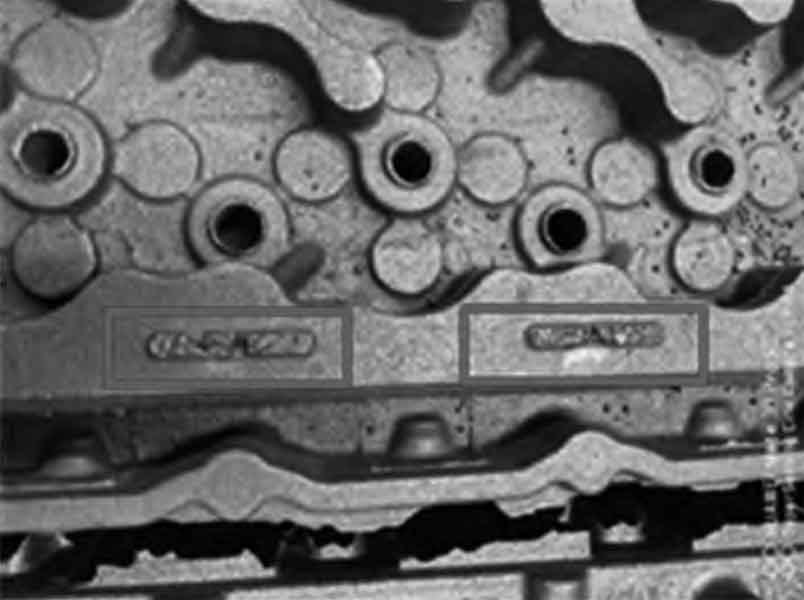
- Predicting Mold Filling: Simulation software can model how molten metal will flow into the mold during the casting process. This allows manufacturers to predict potential defects, like cold shuts or misruns, and adjust the design of the gating system or the pouring technique to ensure complete and uniform filling.
- Solidification Simulation: Simulating the solidification process can help predict defects like shrinkage, porosity, or hot tears that occur due to differential cooling rates. By adjusting the mold design or the placement of risers and chills, these defects can be minimized.
- Thermal Stress Simulation: Simulating thermal stresses during cooling can predict the occurrence of defects like hot tears or warping. By modifying the cooling process or the casting design, these defects can be avoided.
- Microstructure Simulation: Advanced simulation tools can predict the microstructure of the final casting, which can influence its mechanical properties. This can help in predicting and preventing defects like inclusions or segregation.
- Gas Porosity Simulation: Simulation can also help in understanding the generation and escape of gases during casting, thereby predicting potential gas porosity defects. Based on the simulation results, venting systems can be designed more effectively to allow gases to escape.
- Optimizing Process Parameters: By simulating the entire casting process, foundries can optimize various process parameters like pouring rate, pouring temperature, mold temperature, etc., to minimize defects and improve casting quality.
Simulation plays a critical role in the casting industry, allowing foundries to predict potential casting defects and take preventative measures. By integrating simulation tools into their design and manufacturing processes, foundries can improve the quality of their castings, reduce costs associated with defects and rework, and enhance their productivity and competitiveness in the market.