Lost foam casting is an innovative manufacturing process that involves the use of foam patterns to create complex metal parts. The process has gained popularity in recent years due to its ability to produce intricate designs with high precision and cost-effectiveness. While I don’t have access to real-time information on specific lost foam casting manufacturers, I can provide you with an overview of the process and its benefits.
Lost foam casting, also known as evaporative pattern casting, is a casting method where a foam pattern is used as a mold for creating metal parts. The foam pattern is typically made of expanded polystyrene (EPS) or other foam materials, which can be easily shaped and carved into complex forms. The pattern is then coated with a refractory material to enhance its strength and heat resistance.
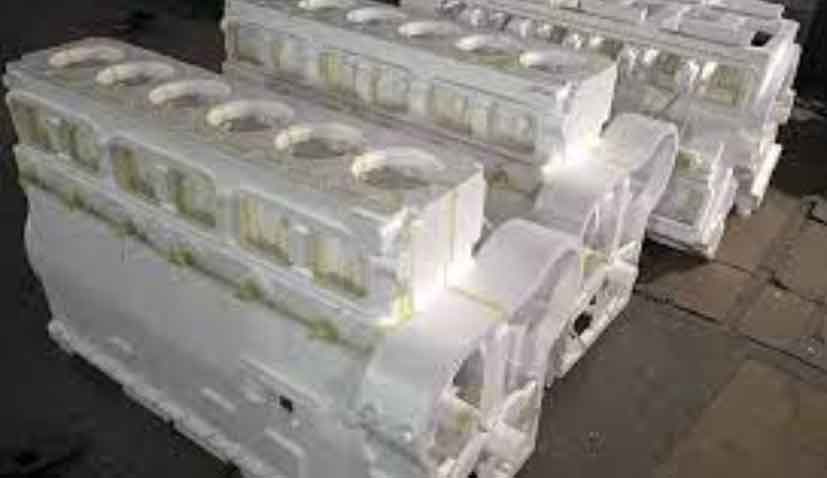
Once the pattern is ready, it is embedded in a flask and surrounded by unbonded sand or other loose molding media. Molten metal is poured into the flask, causing the foam pattern to vaporize and escape through the sand, leaving behind a cavity in the shape of the desired part. The molten metal fills this void, solidifies, and forms the final metal part.
Lost foam casting offers several advantages over traditional casting methods:
- Complex Designs: The foam patterns can be easily shaped and carved into intricate designs, allowing for the production of complex parts that may be difficult or expensive to manufacture using other methods.
- Dimensional Accuracy: The foam patterns provide precise and consistent dimensions, resulting in high-quality and accurately sized metal parts.
- Cost-effectiveness: Lost foam casting eliminates the need for complex molds, cores, and gating systems, reducing tooling costs and overall production expenses. It also minimizes material waste since the foam pattern is evaporated and recycled.
- Reduced Post-processing: The casting process produces parts with a smooth surface finish, reducing the need for extensive post-processing operations such as machining or polishing.
- Material Versatility: Lost foam casting can be used with a wide range of metals and alloys, including aluminum, iron, steel, and various non-ferrous metals.
To find lost foam casting manufacturers, you can search online directories, industry-specific trade shows, or contact local foundries that specialize in metal casting processes. It’s important to evaluate the manufacturers based on their expertise, capabilities, quality control measures, and past projects to ensure they meet your specific requirements.