The process of casting parts involves several stages, from initial design to final production. Each stage requires careful planning, expertise, and attention to detail to ensure the successful creation of high-quality cast parts. Here is an overview of the steps involved in the art of casting parts:
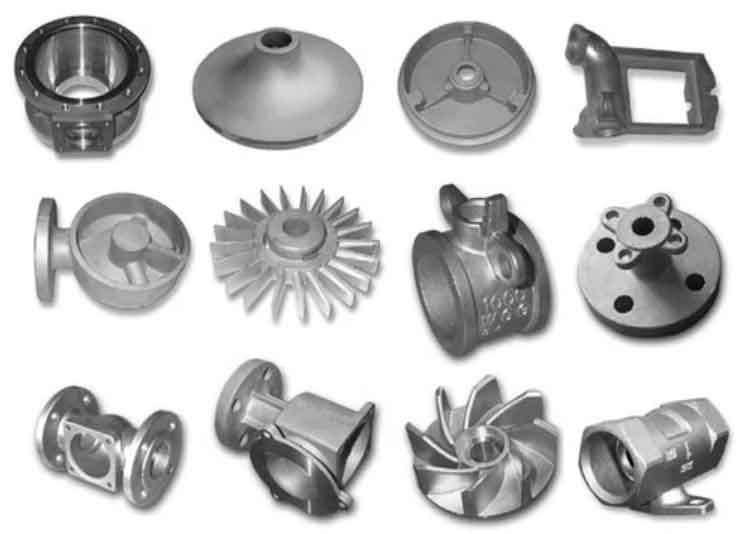
- Design: The first step is the design phase, where engineers or designers create a detailed design of the part to be cast. This includes determining the dimensions, shape, and features of the part, as well as any specific requirements or constraints.
- Pattern Making: Once the design is finalized, a pattern is created. The pattern is a replica of the final part and is used to create the mold for casting. Patterns can be made from various materials, such as wood, metal, or plastic, depending on the complexity and size of the part.
- Mold Making: The pattern is used to create the mold, which is the negative space that will be filled with molten metal to form the final part. The mold can be made from sand, plaster, ceramic, or other materials, depending on the casting process and the type of part being produced.
- Melting and Pouring: In this stage, the chosen metal or alloy is melted in a furnace at high temperatures. Once the metal reaches the desired temperature, it is poured into the mold through a sprue, which allows the molten metal to flow into the mold cavity.
- Solidification and Cooling: After pouring, the molten metal begins to solidify and take the shape of the mold cavity. During this stage, it is important to control the cooling rate to prevent defects and ensure proper solidification of the part.
- Shakeout and Cleaning: Once the metal has cooled and solidified, the mold is removed, and the casting is shaken out to separate it from the remaining mold material. The casting is then cleaned to remove any residual mold material, such as sand or ceramic.
- Finishing and Machining: Depending on the desired final specifications, the casting may undergo additional finishing processes, such as grinding, sandblasting, or heat treatment. If precise dimensions or specific surface finishes are required, the casting may also undergo machining operations such as milling, drilling, or turning.
- Inspection and Quality Control: Throughout the casting process, various inspections and quality control measures are carried out to ensure the part meets the required specifications and quality standards. This may include dimensional checks, visual inspections, non-destructive testing, and material analysis.
- Finishing and Assembly: Once the casting has been inspected and approved, it may undergo further finishing processes, such as painting, coating, or plating, to enhance its appearance or improve its corrosion resistance. If the part is part of a larger assembly, it may also be assembled with other components.
- Final Inspection and Packaging: Before the part is shipped or delivered to the customer, a final inspection is conducted to ensure that all quality requirements have been met. The part is then carefully packaged to protect it during transportation and storage.
Throughout the entire casting process, it is essential to maintain strict quality control measures, adhere to safety standards, and continuously monitor and optimize the process to ensure consistent and high-quality cast parts.