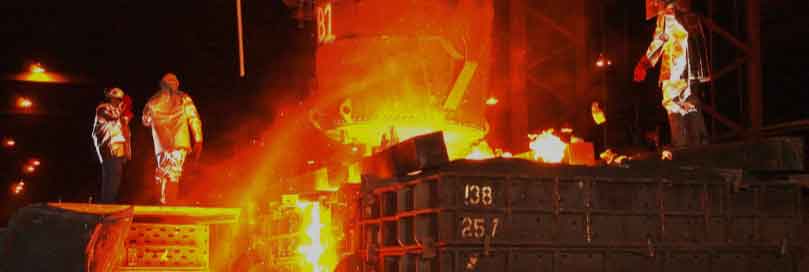
Sand casting is a widely used casting method, but it is important to understand its strengths and limitations compared to other casting methods. Here’s a comparison of sand casting with a few other commonly used casting methods:
- Sand Casting vs. Investment Casting:
- Strengths of Sand Casting: Sand casting is suitable for producing large and complex parts with intricate details. It is a cost-effective method for low to medium production volumes.
- Limitations of Sand Casting: The dimensional accuracy of sand castings may be lower compared to investment castings. The surface finish is generally rougher, requiring additional finishing operations. Sand casting may have limitations in producing thin-walled or highly detailed parts.
- Sand Casting vs. Die Casting:
- Strengths of Sand Casting: Sand casting allows for the production of larger parts and is more suitable for low-volume production. It offers good design flexibility and can accommodate various alloys, including ferrous and non-ferrous metals.
- Limitations of Sand Casting: Sand casting typically has longer production cycles compared to die casting. The dimensional accuracy and surface finish of sand castings may be lower. Die casting is generally more suitable for high-volume production and can achieve tighter tolerances.
- Sand Casting vs. Permanent Mold Casting:
- Strengths of Sand Casting: Sand casting offers greater flexibility in terms of part size and complexity. It can handle larger castings and is suitable for both ferrous and non-ferrous metals. It is a cost-effective method for low to medium production volumes.
- Limitations of Sand Casting: Permanent mold casting generally provides better dimensional accuracy and surface finish compared to sand casting. The tooling costs for permanent mold casting can be higher, making it more suitable for higher production volumes.
- Sand Casting vs. Lost Wax Casting:
- Strengths of Sand Casting: Sand casting is a versatile method that can produce complex parts with larger dimensions. It is cost-effective for low to medium production volumes and is suitable for both ferrous and non-ferrous metals.
- Limitations of Sand Casting: Lost wax casting, also known as investment casting, generally offers better dimensional accuracy and surface finish compared to sand casting. It is more suitable for producing smaller and intricate parts, and it can achieve tighter tolerances.
It’s important to consider factors such as part size, complexity, desired tolerances, production volume, and material selection when choosing the appropriate casting method. Each method has its strengths and limitations, and selecting the right method depends on the specific requirements of the casting project.