Sand casting, like any manufacturing process, can encounter various challenges that may affect the quality and efficiency of the castings produced. Here are some common challenges in sand casting and potential troubleshooting solutions:
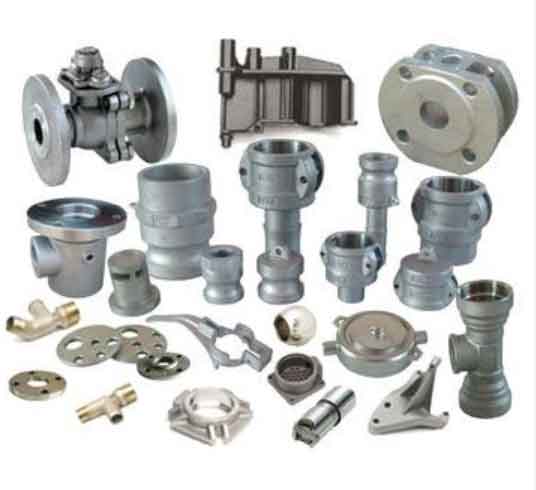
- Incomplete filling or misruns: This occurs when the molten metal does not completely fill the mold cavity, resulting in incomplete castings. Possible causes include low pouring temperature, inadequate gating system design, or insufficient venting. To troubleshoot this issue, you can increase the pouring temperature, modify the gating system to ensure proper flow, or improve venting to allow trapped gases to escape.
- Porosity or gas defects: Porosity refers to the presence of small voids or gas bubbles within the casting. It can be caused by inadequate venting, moisture or contaminants in the mold, or excessive turbulence during pouring. Troubleshooting solutions may include improving venting to allow gases to escape, ensuring the mold is properly dried, and using de-gassing agents or fluxes to remove impurities from the metal.
- Surface defects: Surface defects like roughness, sand inclusions, or metal penetration can occur due to issues with mold preparation or mold release agents. Solutions may involve improving mold surface quality, using proper mold release agents, or adjusting the molding sand properties.
- Dimensional inaccuracies: Variations in casting dimensions can result from factors like mold shift, shrinkage, or improper pattern design. Troubleshooting measures may include ensuring proper alignment of mold halves, adjusting the pattern dimensions to account for shrinkage, or using shrinkage compensating techniques.
- Cracking or hot tearing: Cracks or hot tears can occur due to high thermal stresses during solidification or cooling of the casting. This can be caused by inadequate feeding systems, improper riser design, or insufficient mold strength. Solutions may involve improving the feeding system, redesigning risers to provide proper feeding, or increasing mold strength through additives or coatings.
- Casting distortion: Distortion or warping of castings can result from uneven cooling or insufficient rigidity in the mold. Troubleshooting measures may include optimizing cooling rates, using chills or cooling inserts to control cooling rates, or modifying the mold material to improve rigidity.
- Mold erosion or erosion-related defects: Erosion of the mold can occur due to the high temperature and turbulence of the molten metal during pouring. This can lead to defects such as metal penetration or sand wash. Solutions may involve using coatings or refractory materials to improve mold resistance or adjusting pouring parameters to reduce turbulence.
To troubleshoot these challenges effectively, it is important to carefully analyze the specific cause of the problem through visual inspection, process monitoring, or laboratory testing. By identifying the root cause, appropriate corrective actions can be taken to address the challenges and improve the quality and efficiency of the sand casting process.