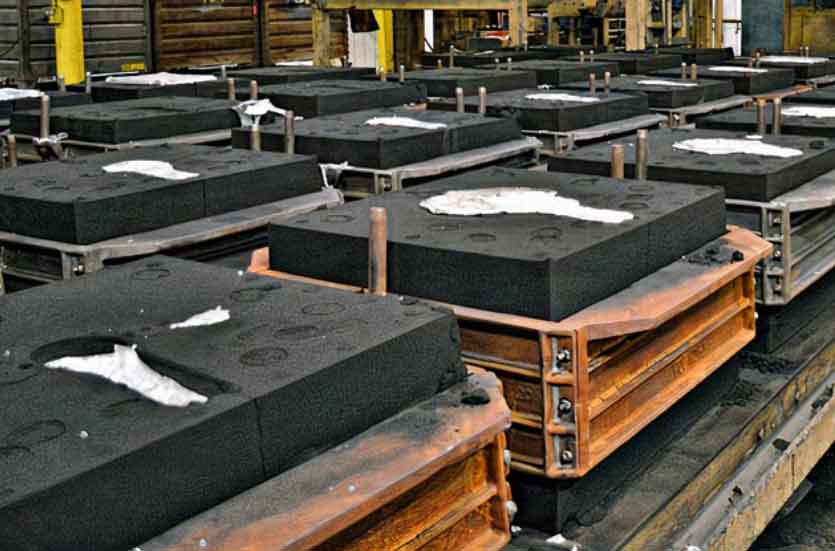
Resin sand casting has significantly expanded design possibilities for the production of complex metal components. With its unique capabilities and advantages, resin sand casting enables engineers and designers to create intricate shapes, detailed features, and complex geometries that were previously difficult or impossible to achieve using traditional casting methods. Let’s explore how resin sand casting unlocks new design possibilities for complex metal components.
1. Intricate Geometries:
Resin sand casting allows for the production of intricate and complex geometries with precision. The combination of resin and sand provides excellent moldability, enabling the creation of intricate details, undercuts, thin walls, and complex internal cavities. This capability opens up possibilities for designing components with intricate patterns, intricate textures, and complex internal structures.
2. Thin-Walled Structures:
Resin sand casting is well-suited for the production of thin-walled metal components. The use of high-quality sand and resin binders ensures the integrity and stability of the mold, even with thin sections. This enables the fabrication of lightweight components with thin walls, reducing material usage and weight while maintaining structural integrity. Thin-walled structures find applications in industries such as aerospace, automotive, and consumer electronics.
3. Complex Internal Features:
Resin sand casting allows for the creation of complex internal features within metal components. The mold can be designed to incorporate intricate cores and channels, facilitating the production of components with complex cooling or fluid flow requirements. This capability is particularly advantageous for manufacturing components such as engine blocks, cylinder heads, and heat exchangers that require intricate internal passages.
4. Multi-Component Assemblies:
Resin sand casting enables the production of multi-component assemblies in a single casting. By utilizing expendable cores and patterns, complex assemblies can be cast as a single integrated unit, reducing the need for additional machining or assembly operations. This not only saves time and costs but also ensures tighter dimensional tolerances and improved overall component performance.
5. Material Selection Flexibility:
Resin sand casting offers versatility in material selection, accommodating a wide range of ferrous and non-ferrous alloys. Engineers and designers have the flexibility to choose the most suitable material for their specific application requirements, whether it’s aluminum, iron, steel, bronze, or other alloys. This material selection flexibility allows for the optimization of mechanical properties, corrosion resistance, and other performance characteristics.
6. Design Iteration and Prototyping:
Resin sand casting facilitates design iteration and prototyping processes. The ability to quickly produce molds and cast metal components enables engineers and designers to iterate and refine their designs rapidly. This iterative approach helps optimize the component’s performance, functionality, and manufacturability before committing to large-scale production, ultimately reducing development time and costs.
7. Customization and Personalization:
Resin sand casting allows for customization and personalization of metal components. Complex shapes, intricate patterns, and unique features can be easily incorporated into the design, catering to specific customer requirements or market preferences. This customization capability is particularly valuable in industries such as art, architecture, and jewelry, where individuality and uniqueness are highly valued.
8. Integration of Inserts and Reinforcements:
Resin sand casting enables the integration of inserts, reinforcements, and other functional elements into metal components during the casting process. This eliminates the need for additional assembly operations and enhances the structural integrity and performance of the final component. Inserts, such as threaded inserts or reinforcement plates, can be securely incorporated into the casting, resulting in a more robust and efficient design.
Resin sand casting has revolutionized the design possibilities for complex metal components. Its ability to produce intricate geometries, thin-walled structures, complex internal features, multi-component assemblies, and customized designs has expanded the horizons of engineers and designers. With resin sand casting, manufacturers can create highly efficient, visually appealing, and functionally optimized metal components across a wide range of industries.