Investment casting is a versatile process that enables the production of intricate and complex metal parts with high precision. This article explores various techniques used in investment casting to achieve complex geometries, along with case studies demonstrating successful applications of these techniques in different industries.
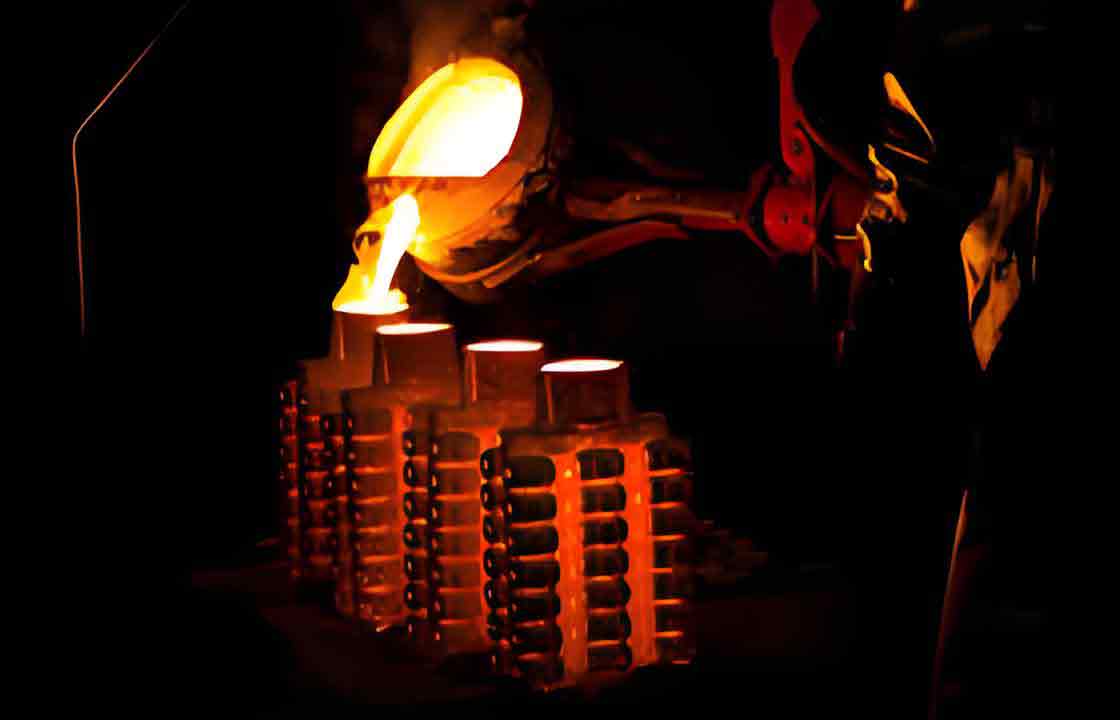
Introduction
Investment casting is a manufacturing process that allows for the creation of parts with detailed geometries and fine features. The process involves creating a wax pattern, encasing it in a ceramic shell, and then melting away the wax to leave a mold for molten metal. This method is ideal for producing components with complex shapes that are difficult or impossible to achieve with other casting methods.
Techniques for Casting Complex Geometries
- 3D Printing for Pattern Making
- Ceramic Shell Building
- Gating and Riser Design
- Directional Solidification
- Core Inserts and Multi-Part Molds
- Advanced Simulation and Modeling
3D Printing for Pattern Making
Key Points:
- Precision and Detail: 3D printing allows for the creation of highly detailed and precise wax patterns directly from CAD models.
- Complex Shapes: Enables the production of intricate and complex geometries without the need for traditional tooling.
Benefits:
- Reduces lead times and costs associated with tooling.
- Enhances design flexibility and allows for rapid prototyping.
Ceramic Shell Building
Key Points:
- Layered Coating: Applying multiple layers of ceramic slurry and stucco to build a strong and durable mold around the wax pattern.
- High-Temperature Tolerance: Ensures the mold can withstand the high temperatures of molten metal.
Benefits:
- Provides excellent surface finish and dimensional accuracy.
- Suitable for casting high-melting-point alloys.
Gating and Riser Design
Key Points:
- Optimal Metal Flow: Designing gates and risers to control the flow of molten metal and minimize turbulence.
- Defect Reduction: Prevents common casting defects such as porosity and incomplete fills.
Benefits:
- Improves the quality and consistency of the final cast parts.
- Enhances yield and reduces material waste.
Directional Solidification
Key Points:
- Controlled Cooling: Managing the solidification process to ensure that the metal solidifies in a controlled manner from one end to the other.
- Grain Structure Optimization: Produces a finer and more uniform grain structure, enhancing mechanical properties.
Benefits:
- Reduces internal stresses and improves the mechanical properties of cast parts.
- Minimizes defects such as shrinkage and segregation.
Core Inserts and Multi-Part Molds
Key Points:
- Complex Internal Features: Using ceramic cores or multi-part molds to create complex internal geometries and hollow sections.
- Removable Cores: Ensuring that cores can be easily removed after casting without damaging the part.
Benefits:
- Allows for the production of intricate internal passages and features.
- Expands the design possibilities for complex components.
Advanced Simulation and Modeling
Key Points:
- Process Simulation: Utilizing advanced simulation software to model the entire casting process, from wax pattern creation to solidification.
- Defect Prediction: Identifying potential defects and optimizing process parameters before actual production.
Benefits:
- Reduces trial-and-error and increases first-time quality.
- Enhances process understanding and control.
Comparative Table: Traditional vs. Advanced Investment Casting Techniques
Aspect | Traditional Techniques | Advanced Techniques |
---|---|---|
Pattern Making | Manual or injection molding | 3D printing |
Mold Building | Single-layer coatings | Multi-layer ceramic shell building |
Gating and Riser Design | Basic designs | Optimized designs using simulation |
Solidification Control | Natural cooling | Directional solidification |
Internal Features | Limited to simple cores | Complex internal features with core inserts |
Defect Prediction | Based on experience and inspection | Advanced simulation and modeling |
Case Studies
Aerospace Industry: Turbine Blades
Technique Used: Directional Solidification and Advanced Alloys
Overview: Turbine blades in jet engines operate under extreme temperatures and stresses, requiring high precision and superior mechanical properties. The use of directional solidification in investment casting allows for the production of blades with a fine, uniform grain structure that enhances their performance and durability.
Outcome:
- Enhanced Durability: The controlled solidification process results in blades with excellent high-temperature strength and resistance to thermal fatigue.
- Cost Efficiency: The ability to cast complex geometries in a single piece reduces the need for assembly and machining, lowering production costs.
Automotive Industry: Engine Components
Technique Used: 3D Printing for Pattern Making and Gating Design
Overview: The automotive industry demands lightweight and high-strength components for improved fuel efficiency and performance. Using 3D printing to create wax patterns allows for intricate designs and optimized gating systems to ensure proper metal flow and minimal defects.
Outcome:
- Improved Performance: The use of advanced alloys and precise casting techniques results in components with superior strength and fatigue resistance.
- Reduced Lead Time: Rapid prototyping with 3D printing shortens development cycles, enabling faster time-to-market for new designs.
Medical Devices: Surgical Instruments
Technique Used: Multi-Part Molds and Core Inserts
Overview: Surgical instruments require high precision and must meet stringent quality standards. Investment casting with multi-part molds and core inserts allows for the production of instruments with complex geometries and fine details.
Outcome:
- High Precision: The ability to cast intricate features ensures that surgical instruments meet the required specifications for medical use.
- Cost Savings: The efficiency of the casting process reduces the need for extensive machining, lowering overall production costs.
Future Trends in Investment Casting
- Integration of AI and Machine Learning
- Development of New Alloys and Materials
- Sustainability Initiatives
- Enhanced Simulation Capabilities
Integration of AI and Machine Learning
Trend:
- Utilizing AI and machine learning to analyze casting data, predict defects, and optimize process parameters in real-time.
Impact:
- Improved Quality: Enhanced ability to detect and correct issues before they result in defects.
- Increased Efficiency: Streamlined processes and reduced waste.
Development of New Alloys and Materials
Trend:
- Research and development of new alloys with improved mechanical properties, corrosion resistance, and thermal stability.
Impact:
- Expanded Applications: Ability to meet the demands of more challenging environments and industries.
- Superior Performance: Enhanced durability and reliability of cast components.
Sustainability Initiatives
Trend:
- Implementation of sustainable practices, including the use of recyclable materials and energy-efficient processes.
Impact:
- Environmental Benefits: Reduced carbon footprint and waste.
- Regulatory Compliance: Meeting increasingly stringent environmental regulations.
Enhanced Simulation Capabilities
Trend:
- Advancements in simulation software to provide more accurate and detailed modeling of the casting process.
Impact:
- Predictive Accuracy: Greater ability to predict and mitigate potential defects.
- Process Optimization: Improved understanding and control over the entire casting process.
Conclusion
The investment casting of complex geometries has been significantly enhanced by advanced techniques such as 3D printing, improved ceramic shell building, optimized gating and riser design, directional solidification, and the use of core inserts. These advancements have enabled the production of high-quality, intricate parts across various industries, including aerospace, automotive, and medical devices. As technology continues to evolve, the integration of AI, new materials, sustainable practices, and enhanced simulation capabilities will further elevate the capabilities and applications of investment casting. By adopting these innovations, manufacturers can achieve greater durability and cost efficiency, ensuring their competitiveness in a rapidly changing market.