Introduction
Electric vehicles represent the future of the automotive industry, driven by the need for sustainable and efficient transportation. As the demand for electric vehicles grows, so does the necessity for advanced manufacturing techniques capable of producing lightweight and complex components. Sand casting, a versatile and cost-effective method, has evolved to meet these demands. This article explores advanced sand casting techniques tailored for the intricate geometries required in electric vehicle applications.
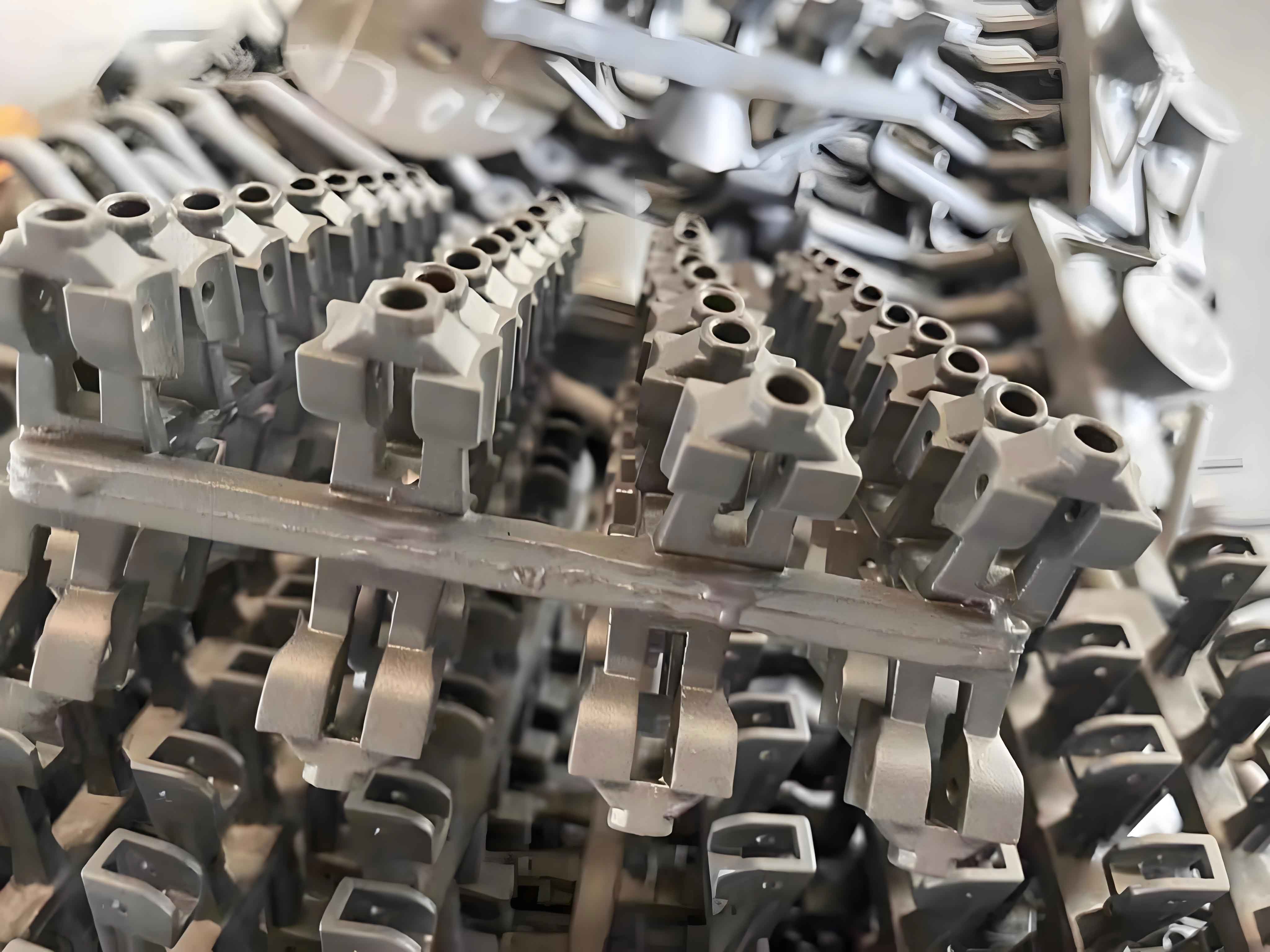
Overview of Sand Casting
Sand casting involves creating a mold from a sand-based mixture, into which molten metal is poured to form the desired shape. The fundamental steps in the sand casting process are:
- Pattern Making: Creating a pattern that resembles the final product.
- Mold Making: Placing the pattern in a flask and packing it with sand to form a mold.
- Core Making: Producing cores for hollow sections within the casting.
- Pouring: Pouring molten metal into the mold cavity.
- Cooling and Shakeout: Allowing the metal to solidify before breaking the mold to retrieve the casting.
- Finishing: Cleaning and finishing the casting to achieve the desired specifications.
Advanced Sand Casting Techniques
1. 3D Printing for Sand Molds and Cores
3D printing technology has transformed sand casting by enabling the creation of highly complex molds and cores directly from digital models. This eliminates the need for traditional pattern making and allows for:
- Rapid Prototyping: Quick turnaround times for prototype development.
- Complex Geometries: Ability to produce intricate designs and internal features.
- Customization: Easy adjustments to digital models for customized parts.
2. Automated Mold Making Systems
Automated systems enhance the efficiency and accuracy of mold making. These systems use computer-controlled machinery to pack sand around the pattern, ensuring consistent mold quality and reducing human error. Key benefits include:
- Consistency: Uniform mold density and integrity.
- Speed: Faster production compared to manual methods.
- Cost Reduction: Lower labor costs and reduced manual intervention.
3. Hybrid Casting Techniques
Hybrid casting techniques combine traditional sand casting with other processes like investment casting or die casting. This hybrid approach offers:
- Improved Surface Finish: Smoother surfaces and finer details.
- Enhanced Properties: Better mechanical properties through material control.
- Versatility: Suitable for a wider range of materials and geometries.
4. Simulation and Modeling Software
Advanced simulation and modeling tools play a critical role in optimizing the sand casting process. These tools allow engineers to predict and analyze various aspects of casting, such as mold filling, solidification, and defect formation. Advantages include:
- Defect Mitigation: Identifying and addressing potential defects before casting.
- Process Optimization: Fine-tuning parameters for optimal results.
- Cost Savings: Reducing trial-and-error approaches and lowering production costs.
Applications in Electric Vehicles
Case Study 1: Battery Housing
A leading EV manufacturer used 3D printed sand molds to produce battery housings with complex internal cooling channels. The advanced mold-making process enabled the creation of intricate geometries, enhancing thermal management and overall battery performance.
Case Study 2: Motor Housings
Hybrid casting techniques were employed to produce lightweight motor housings with improved mechanical properties. The combination of sand casting and investment casting allowed for fine details and superior surface finish, contributing to better motor efficiency and longevity.
Comparison of Traditional and Advanced Sand Casting Techniques
Feature | Traditional Sand Casting | Advanced Sand Casting |
---|---|---|
Pattern Making | Manual | 3D Printing |
Mold Making | Manual | Automated |
Complexity of Geometries | Limited | High |
Lead Time | Long | Short |
Consistency | Variable | High |
Customization | Limited | Extensive |
Defect Rates | Higher | Lower |
Cost Efficiency | Moderate | High |
Advantages and Disadvantages
Advantages of Advanced Sand Casting
- High Precision: Enhanced accuracy for producing complex geometries.
- Flexibility: Quick adaptation to design changes.
- Efficiency: Reduced lead times and labor costs.
- Quality: Improved surface finish and material properties.
Disadvantages of Advanced Sand Casting
- Initial Investment: Higher costs for advanced equipment and software.
- Training: Need for skilled personnel to operate advanced machinery and software.
- Material Limitations: Certain advanced techniques may be limited to specific materials.
Key Components for Electric Vehicles Using Advanced Sand Casting
- Battery Housings: Lightweight and complex structures with integrated cooling channels.
- Motor Housings: Precision components requiring high strength and fine surface finish.
- Inverter Casings: Compact and complex designs for efficient thermal management.
- Chassis Components: Structural parts benefiting from reduced weight and enhanced strength.
Future Trends
The future of sand casting in EV applications is promising, with trends focusing on further integration of digital technologies and materials innovation. Key future trends include:
- Artificial Intelligence (AI): Utilizing AI for predictive analytics and defect detection.
- New Materials: Development of advanced alloys and composites tailored for sand casting.
- Sustainability: Eco-friendly sand casting processes and materials to reduce environmental impact.
Conclusion
Advanced sand casting techniques have significantly expanded the capabilities of traditional sand casting, making it possible to produce the intricate and high-performance components required in electric vehicle applications. By embracing these advancements, manufacturers can achieve superior quality, reduced production times, and cost savings, ultimately contributing to the growth and success of the electric vehicle industry.