Xintekast casting tracking technology provides complete traceability for every casting by linking sand core history, shape history, and liquid metal history in a single database, from sand core production to pouring and drop sand. By using casting tracking technology, castings have unique features from production batches to individual components A unique history of craftsmanship. Casting tracking technology provides Industry 4.0 traceability for castings; Prevent molten iron from pouring into unqualified sand core components; And enable engineers to identify and eliminate the root causes of metallurgical defects.
Casting tracking first carves a unique identification code on the tracking sand core. The tracking sand core is inserted into the assembly of this sand core during assembly to define the starting time and apply this unique identification code to each casting. By using the casting tracking database, reading the convex identification code on the casting can provide complete traceability between the casting and each stage of the casting process.
The identification of each sand core component is associated with the radio frequency identification label attached to the sand box. During pouring, the antenna reads the identification number of the sand box to identify Sand box to identify the castings poured from each ladle. The handshake between the casting tracker and the ladle tracker provides continuous tracking of the history of the sand core and liquid metal, including the pouring sequence of the ladle.
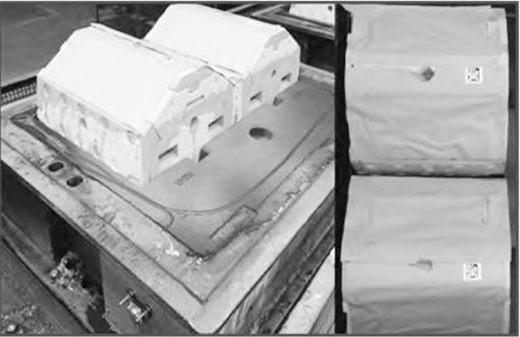
Casting result report
All casting and ladle tracking results – from start to sand drop, from melting to pouring – are compiled into a single data set In the library, used for traceability, process optimization, and metallurgical troubleshooting. The database can also include results of microstructure and chemical analysis. All The results are summarized in the performance summary report and can be generated as needed. All data is stored in a central database, which casting engineers can fully access.
The benefits of casting tracking
- Traceability starts from the assembly of sand cores (initial event);
- Quantitative measurement and control of sand core storage time;
- Associate the sand core history with the liquid metal history during pouring with the Ladle Tracker (casting occurrence event);
- Automatically prevent molten iron from pouring into unqualified or unidentified sand core components;
- The comprehensive database is used for identifying the root cause of defects, including the casting sequence of molten iron in the ladle;
- Eliminate manual data input;
- Eliminate manual data records and paper records;
- Multiple data sources are organized in a process database;
- Industry 4.0 traceability to determine improvements in process efficiency, prevent production of substandard castings, and identify the root cause of metallurgical defects Due to;
- Real time monitoring of the entire casting process on any Internet device;
- Incorporate microstructure, visual inspection, and non-destructive testing results into the casting tracking database.
Casting tracking hardware/software
- The casting tracking hardware consists of separate hardware modules that can be customized and adjusted to fit any metal casting device
The layout, process flow, and production capacity of the equipment. Xintekast can also provide tracking sand core engraving machines; - Optional Radio Frequency Identification (RFID) sandbox label configuration to be suitable for various sandbox configurations;
- The configurable software provides real-time monitoring of processes for engineers, production personnel, and management through customized reporting options.