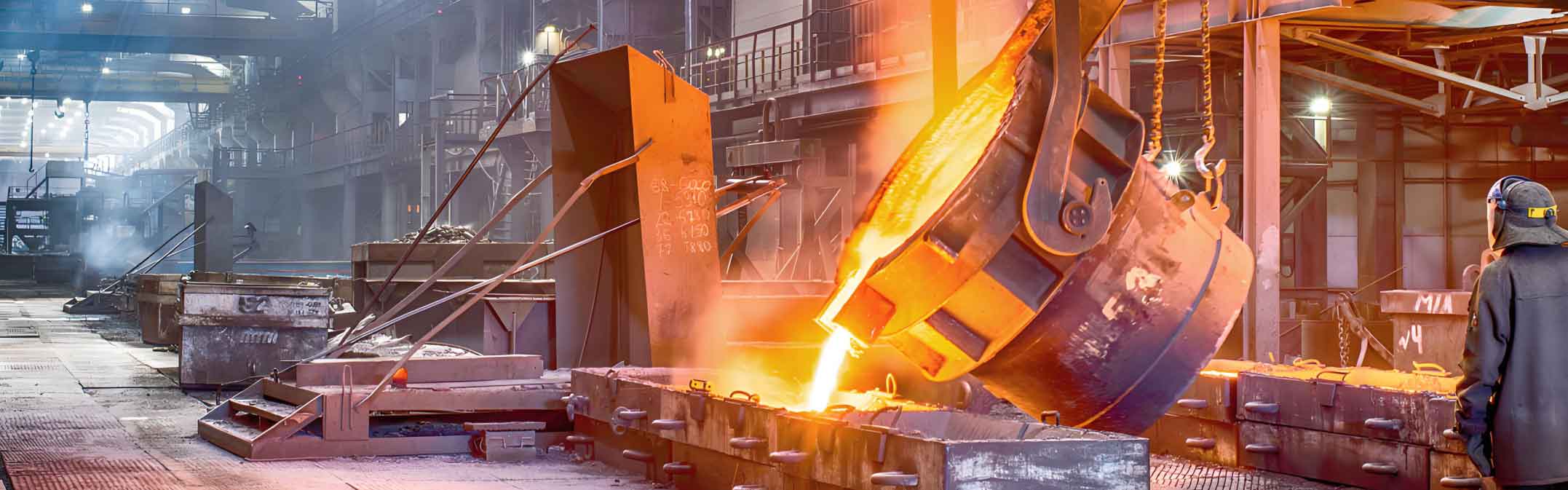
Lost foam casting and lost wax casting are two highly regarded techniques in the casting industry, each offering unique advantages and applications. Both methods allow for the production of intricate and complex metal components, but they differ significantly in their processes, materials, and outcomes. This comparative study aims to explore the key differences between lost foam casting and lost wax casting, highlighting their respective advantages, disadvantages, and suitability for various applications.
Introduction to Lost Foam Casting and Lost Wax Casting
Lost foam casting and lost wax casting are precision casting methods used to create detailed and complex metal parts. Despite their similarities in producing high-quality castings, the two processes have distinct methodologies.
Lost Foam Casting
Lost foam casting involves creating a foam pattern that replicates the final metal part, coating it with a refractory material, and embedding it in a sand mold. When molten metal is poured into the mold, the foam pattern vaporizes, leaving behind a detailed metal casting.
Key Steps in Lost Foam Casting
- Foam Pattern Creation: A foam model of the desired component is created using suitable foam materials.
- Pattern Assembly: The foam pattern is assembled with gating systems if needed.
- Coating: The foam pattern is coated with a refractory material to form a thin shell.
- Mold Preparation: The coated foam pattern is placed in a sand mold, and sand is packed around it.
- Metal Pouring: Molten metal is poured into the mold, causing the foam pattern to vaporize and be replaced by the metal.
- Mold Breakout: Once the metal has solidified, the sand mold is broken away to reveal the metal casting.
- Finishing: The casting is cleaned, and any excess material is removed to achieve the final product.
Lost Wax Casting
Lost wax casting, also known as investment casting, involves creating a wax pattern that replicates the final metal part, coating it with a ceramic shell, and then melting the wax out of the mold before pouring molten metal into the cavity.
Key Steps in Lost Wax Casting
- Wax Pattern Creation: A wax model of the desired component is created using suitable wax materials.
- Pattern Assembly: The wax pattern is assembled with gating systems if needed.
- Shell Building: The wax pattern is repeatedly dipped into a ceramic slurry and coated with fine sand to build a ceramic shell.
- Wax Removal: The ceramic shell is heated to melt and remove the wax, leaving a hollow ceramic mold.
- Metal Pouring: Molten metal is poured into the ceramic mold, filling the cavity left by the wax pattern.
- Shell Removal: Once the metal has solidified, the ceramic shell is broken away to reveal the metal casting.
- Finishing: The casting is cleaned, and any excess material is removed to achieve the final product.
Comparative Analysis: Lost Foam Casting vs. Lost Wax Casting
The following sections provide a detailed comparison of lost foam casting and lost wax casting based on various factors such as materials, process complexity, casting defects, surface finish, dimensional accuracy, and applications.
Materials
Lost Foam Casting
- Foam Pattern Materials: Typically uses expanded polystyrene (EPS), expanded polypropylene (EPP), or polyurethane foam.
- Coating Materials: Uses refractory coatings to create a thin shell around the foam pattern.
- Mold Materials: Sand is used to create the mold around the coated foam pattern.
Lost Wax Casting
- Wax Pattern Materials: Uses various types of waxes, such as paraffin, beeswax, or synthetic wax.
- Shell Building Materials: Uses ceramic slurry and fine sand to build a ceramic shell.
- Mold Materials: The ceramic shell acts as the mold for the molten metal.
Aspect | Lost Foam Casting | Lost Wax Casting |
---|---|---|
Pattern Materials | Expanded polystyrene, expanded polypropylene, polyurethane foam | Paraffin, beeswax, synthetic wax |
Coating Materials | Refractory coatings | Ceramic slurry, fine sand |
Mold Materials | Sand | Ceramic shell |
Process Complexity
Lost Foam Casting
- Complexity: Moderate; involves creating a foam pattern, coating, and embedding in sand.
- Key Challenges: Managing the vaporization of the foam pattern and ensuring complete mold filling.
Lost Wax Casting
- Complexity: High; involves creating a wax pattern, building a ceramic shell, and melting out the wax.
- Key Challenges: Ensuring the integrity of the ceramic shell and removing all traces of wax.
Aspect | Lost Foam Casting | Lost Wax Casting |
---|---|---|
Process Complexity | Moderate | High |
Key Challenges | Vaporization of foam, mold filling | Integrity of ceramic shell, complete wax removal |
Casting Defects
Lost Foam Casting
- Common Defects: Gas porosity, shrinkage porosity, surface defects.
- Mitigation Strategies: High-quality sand, enhanced mold coatings, optimized gating and venting systems, controlled pouring temperature.
Lost Wax Casting
- Common Defects: Shell cracking, incomplete filling, surface roughness.
- Mitigation Strategies: Careful shell building, proper wax removal, controlled pouring and cooling rates.
Aspect | Lost Foam Casting | Lost Wax Casting |
---|---|---|
Common Defects | Gas porosity, shrinkage porosity, surface defects | Shell cracking, incomplete filling, surface roughness |
Mitigation Strategies | High-quality sand, enhanced mold coatings, optimized gating and venting, controlled pouring temperature | Careful shell building, proper wax removal, controlled pouring and cooling |
Surface Finish
Lost Foam Casting
- Surface Finish: Good, but may require post-casting machining for fine details.
- Enhancement Techniques: Advanced foam pattern techniques, improved coating materials, optimized sand properties.
Lost Wax Casting
- Surface Finish: Excellent, often requiring minimal post-casting machining.
- Enhancement Techniques: High-quality wax patterns, precise shell building, controlled cooling rates.
Aspect | Lost Foam Casting | Lost Wax Casting |
---|---|---|
Surface Finish | Good, may require post-casting machining | Excellent, minimal post-casting machining |
Enhancement Techniques | Advanced foam pattern techniques, improved coating materials, optimized sand properties | High-quality wax patterns, precise shell building, controlled cooling rates |
Dimensional Accuracy
Lost Foam Casting
- Accuracy: High, suitable for complex geometries.
- Factors Affecting Accuracy: Foam pattern quality, coating material properties, mold stability.
Lost Wax Casting
- Accuracy: Very high, ideal for intricate and detailed components.
- Factors Affecting Accuracy: Wax pattern precision, shell integrity, controlled pouring and cooling processes.
Aspect | Lost Foam Casting | Lost Wax Casting |
---|---|---|
Dimensional Accuracy | High, suitable for complex geometries | Very high, ideal for intricate components |
Factors Affecting Accuracy | Foam pattern quality, coating material properties, mold stability | Wax pattern precision, shell integrity, controlled pouring and cooling |
Applications
Lost Foam Casting
- Automotive Industry: Engine blocks, brake discs, suspension components.
- Industrial Machinery: Gear housings, pump housings, machine frames.
- Aerospace Industry: Structural components, turbine blades, airframe parts.
Lost Wax Casting
- Aerospace Industry: Turbine blades, engine components, precision structural parts.
- Medical Devices: Implants, surgical instruments, dental components.
- Art and Jewelry: Sculptures, intricate jewelry pieces, decorative items.
Industry | Lost Foam Casting Applications | Lost Wax Casting Applications |
---|---|---|
Automotive | Engine blocks, brake discs, suspension components | Not commonly used |
Industrial Machinery | Gear housings, pump housings, machine frames | Not commonly used |
Aerospace | Structural components, turbine blades, airframe parts | Turbine blades, engine components, precision structural parts |
Medical Devices | Not commonly used | Implants, surgical instruments, dental components |
Art and Jewelry | Not commonly used | Sculptures, intricate jewelry pieces, decorative items |
Conclusion
Lost foam casting and lost wax casting are two highly effective casting methods, each offering distinct advantages and challenges. Lost foam casting is well-suited for producing large, complex metal components with high dimensional accuracy and good surface finish, making it ideal for automotive, industrial machinery, and aerospace applications. On the other hand, lost wax casting excels in producing intricate and detailed components with excellent surface finish and very high dimensional accuracy, making it the preferred choice for aerospace, medical devices, and art and jewelry applications.
Aspect | Lost Foam Casting | Lost Wax Casting |
---|---|---|
Pattern Materials | Expanded polystyrene, expanded polypropylene, polyurethane foam | Paraffin, beeswax, synthetic wax |
Coating Materials | Refractory coatings | Ceramic slurry, fine sand |
Mold Materials | Sand | Ceramic shell |
Process Complexity | Moderate | High |
Key Challenges | Vaporization of foam, mold filling | Integrity of ceramic shell, complete wax removal |
Common Defects | Gas porosity, shrinkage porosity, surface defects | Shell cracking, incomplete filling, surface roughness |
Mitigation Strategies | High-quality sand, enhanced mold coatings, optimized gating and venting, controlled pouring temperature | Careful shell building, proper wax removal, controlled pouring and cooling |
Surface Finish | Good, may require post-casting machining | Excellent, minimal post-casting machining |
Enhancement Techniques | Advanced foam pattern techniques, improved coating materials, optimized sand properties | High-quality wax patterns, precise shell building, controlled cooling rates |
Dimensional Accuracy | High, suitable for complex geometries | Very high, ideal for intricate components |
Factors Affecting Accuracy | Foam pattern quality, coating material properties, mold stability | Wax pattern precision, shell integrity, controlled pouring and cooling |
Applications | Automotive, industrial machinery, aerospace | Aerospace, medical devices, art and jewelry |
By understanding the differences and applications of these two casting methods, manufacturers can choose the most suitable technique for their specific needs, ensuring high-quality, reliable, and cost-effective castings for a wide range of industries.