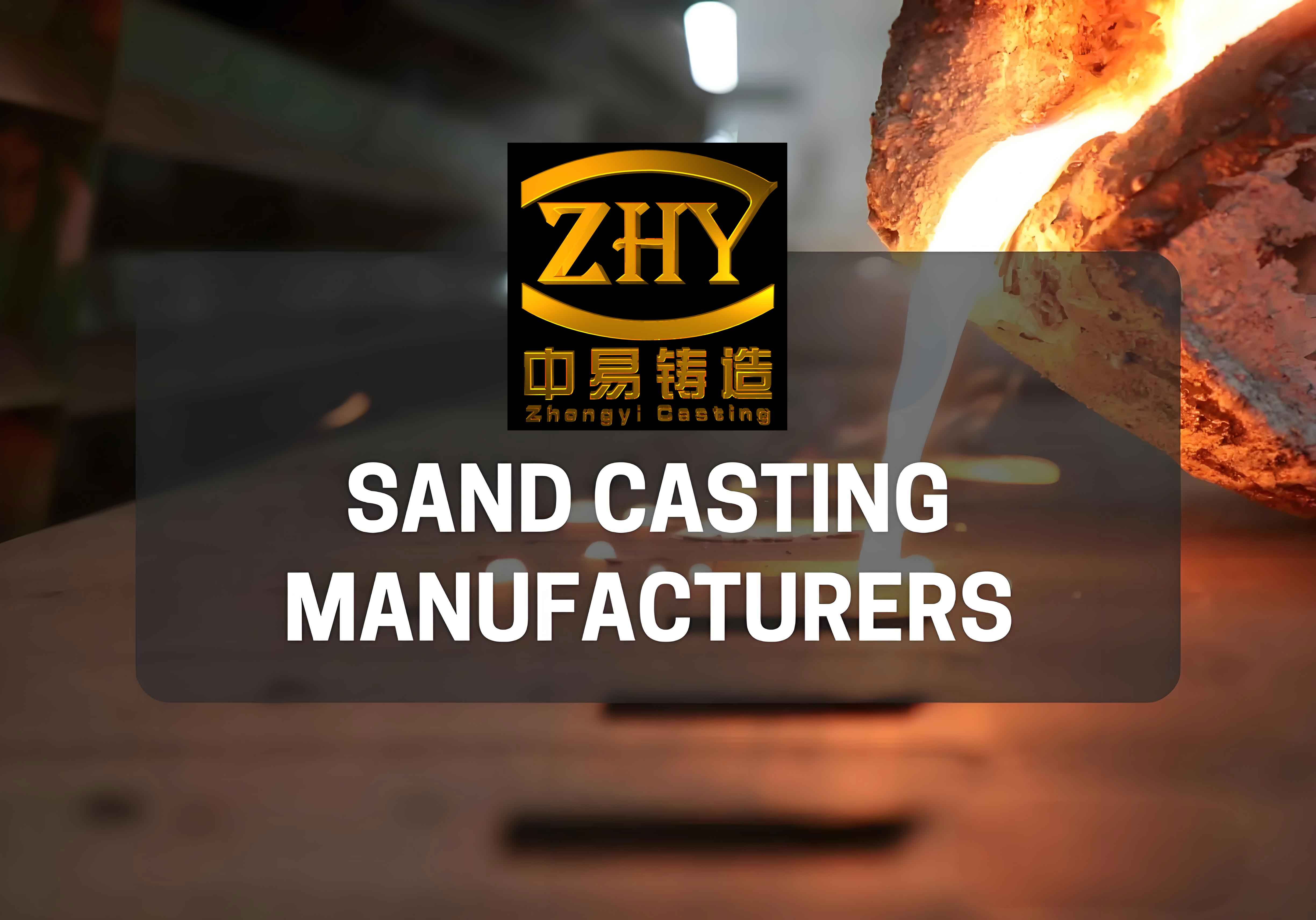
Sand casting is widely used manufacturing process that allows for the production of complex metal parts. However, achieving high product quality in sand casting can be challenging due to factors such as material variability, process complexity, and the inherent properties of sand molds. This article explores how a leading sand casting manufacturer successfully improved product quality through strategic initiatives, advanced technologies, and continuous improvement practices.
Introduction to Sand Casting Quality Challenges
Sand casting manufacturers face several quality challenges, including:
- Defects in Castings:
- Common defects include porosity, shrinkage, and surface imperfections.
- These defects can lead to rework, scrap, and customer dissatisfaction.
- Material Variability:
- Variations in raw materials, such as sand and metal alloys, can affect the consistency and quality of cast parts.
- Process Control:
- The complexity of the sand casting process requires precise control to ensure consistent quality.
Strategic Initiatives for Quality Improvement
1. Implementing Advanced Quality Control Systems
The sand casting manufacturer invested in advanced quality control systems to monitor and ensure product quality at every stage of the manufacturing process. Key components of these systems include:
- Automated Inspection Systems:
- Utilizing automated inspection systems, such as X-ray and ultrasonic testing, to detect defects in cast parts.
- Automated systems provide consistent and accurate inspection results, reducing the likelihood of human error.
- Real-Time Monitoring:
- Implementing real-time monitoring of critical process parameters, such as temperature, pressure, and mold integrity.
- Real-time data allows for immediate corrective actions to prevent defects.
Quality Control System | Description | Benefits |
---|---|---|
Automated Inspection | Using X-ray and ultrasonic testing for defect detection | Consistent, accurate inspection results |
Real-Time Monitoring | Monitoring critical process parameters in real-time | Immediate corrective actions, reduced defects |
2. Enhancing Material Quality and Consistency
To address material variability, the sand casting manufacturer took several steps to ensure the quality and consistency of raw materials:
- Supplier Partnerships:
- Establishing long-term partnerships with reliable suppliers to ensure a consistent supply of high-quality raw materials.
- Working closely with suppliers to develop and maintain quality standards.
- Material Testing:
- Implementing rigorous testing protocols for incoming raw materials to verify their properties and suitability for casting.
- Using advanced testing equipment to assess the composition and characteristics of sand and metal alloys.
Material Quality Strategy | Description | Benefits |
---|---|---|
Supplier Partnerships | Long-term relationships with reliable suppliers | Consistent, high-quality raw materials |
Material Testing | Rigorous testing of incoming materials | Verified material properties, reduced variability |
3. Process Optimization and Control
Optimizing and controlling the sand casting process is crucial for achieving high product quality. The sand casting manufacturer implemented several process optimization strategies:
- Computer-Aided Design (CAD) and Simulation:
- Using CAD and simulation software to design and optimize molds, ensuring accurate and efficient casting.
- Simulation helps identify potential defects and allows for adjustments before production.
- Standard Operating Procedures (SOPs):
- Developing and enforcing SOPs for all stages of the sand casting process.
- SOPs ensure consistency and repeatability, reducing the likelihood of defects.
- Continuous Improvement Programs:
- Implementing continuous improvement programs, such as Six Sigma and Lean Manufacturing, to identify and eliminate sources of variation and waste.
- Encouraging a culture of quality and continuous improvement among employees.
Process Optimization Strategy | Description | Benefits |
---|---|---|
CAD and Simulation | Designing and optimizing molds using software | Accurate, efficient casting, defect prevention |
Standard Operating Procedures | SOPs for consistent, repeatable processes | Reduced defects, increased consistency |
Continuous Improvement Programs | Six Sigma, Lean Manufacturing for ongoing improvement | Elimination of variation, enhanced quality |
Leveraging Technology for Quality Improvement
1. Advanced Data Analytics
The sand casting manufacturer leveraged advanced data analytics to gain insights into the production process and identify opportunities for quality improvement:
- Predictive Analytics:
- Using predictive analytics to anticipate potential issues and take preventive measures.
- Analyzing historical data to identify patterns and trends that impact product quality.
- Process Optimization:
- Utilizing data analytics to optimize process parameters and improve consistency.
- Real-time data analysis allows for quick adjustments to maintain quality standards.
2. Internet of Things (IoT)
IoT technology played a significant role in improving product quality for the sand casting manufacturer:
- Connected Devices:
- Implementing IoT devices to monitor and control equipment and processes in real-time.
- Connected devices provide continuous feedback and enable proactive maintenance.
- Smart Manufacturing:
- Integrating IoT technology with manufacturing processes to create a smart manufacturing environment.
- Smart manufacturing enhances visibility, control, and efficiency, leading to higher product quality.
Technology | Description | Benefits |
---|---|---|
Predictive Analytics | Anticipating issues and analyzing historical data | Preventive measures, pattern identification |
Connected Devices (IoT) | Real-time monitoring and control of processes | Continuous feedback, proactive maintenance |
Smart Manufacturing (IoT) | Integration of IoT for enhanced visibility and control | Higher efficiency, improved product quality |
Case Study: Improving Quality in Practice
A leading sand casting manufacturer faced challenges with product defects and variability in raw materials. By implementing the strategies and technologies discussed above, the manufacturer achieved significant improvements in product quality:
- Reduction in Defects:
- Automated inspection systems and real-time monitoring reduced defects by 30%.
- Enhanced material testing and supplier partnerships ensured consistent raw material quality.
- Increased Consistency:
- Process optimization and CAD simulation improved the accuracy and repeatability of casting processes.
- SOPs and continuous improvement programs fostered a culture of quality and consistency.
- Enhanced Customer Satisfaction:
- Improved product quality led to higher customer satisfaction and increased demand.
- The manufacturer’s reputation for quality attracted new clients and strengthened existing relationships.
Improvement Area | Achievements | Impact on Quality |
---|---|---|
Defect Reduction | 30% reduction in defects | Higher quality, reduced rework and scrap |
Consistency | Improved process accuracy and repeatability | Increased consistency, fewer variations |
Customer Satisfaction | Higher satisfaction and demand | Strengthened reputation, new client acquisition |
Conclusion
Improving product quality is a critical goal for sand casting manufacturers seeking to remain competitive and meet customer expectations. By implementing advanced quality control systems, enhancing material quality and consistency, optimizing processes, and leveraging modern technologies such as data analytics and IoT, a leading sand casting manufacturer successfully improved product quality. These initiatives not only reduced defects and increased consistency but also enhanced customer satisfaction and positioned the manufacturer as a leader in the industry. As the manufacturing landscape continues to evolve, ongoing innovation and a commitment to quality will be essential for sustaining success and driving further improvements in product quality.