In the modern landscape of manufacturing, the integration of automation and robotics has become a game-changer for various industries, and sand casting manufacturing is no exception. This article explores the profound impact, benefits, challenges, and future prospects of implementing automation and robotics in sand casting manufacturing.
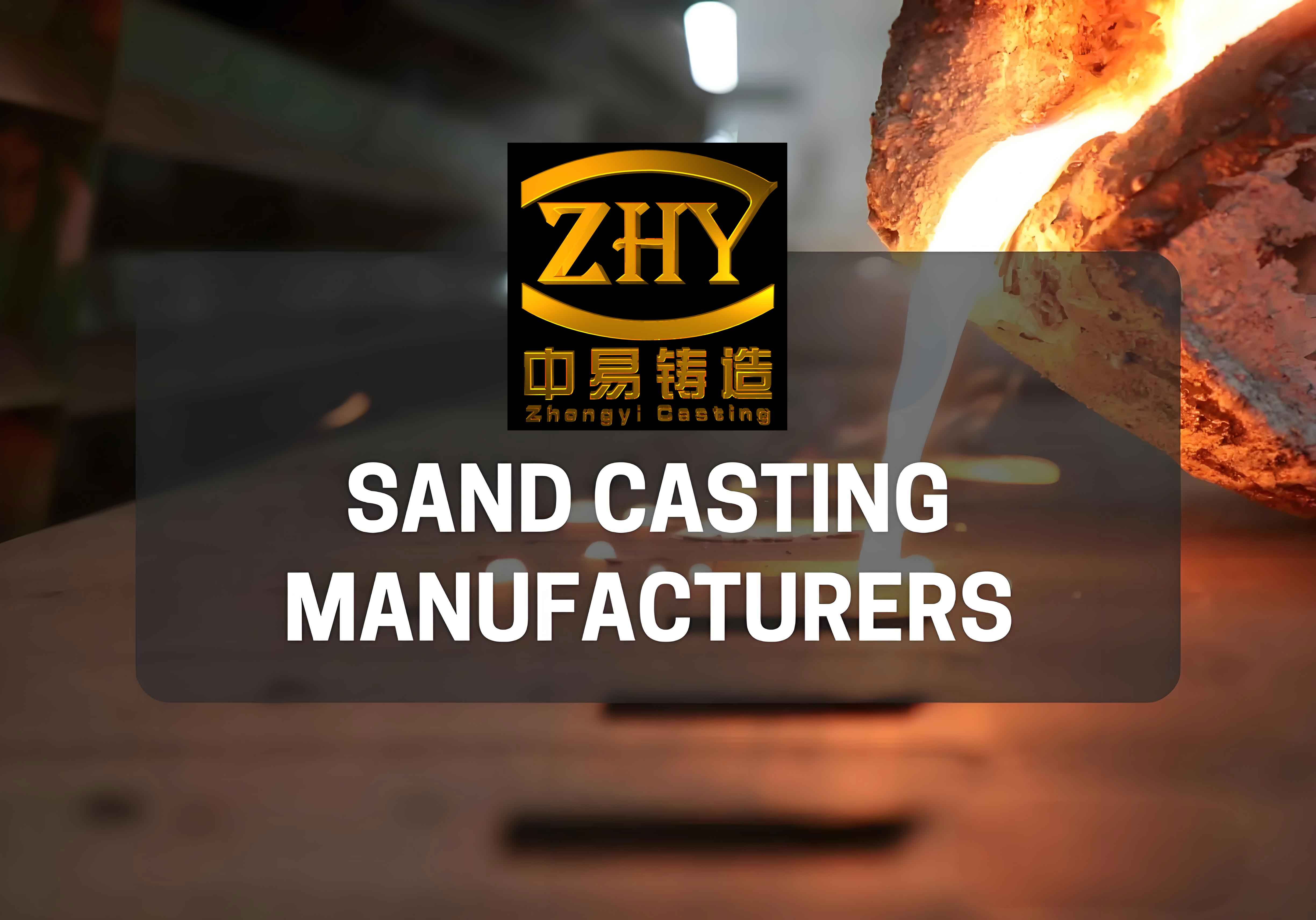
Introduction
Sand casting manufacturing has long been an essential process for producing complex metal components. However, to meet the escalating demands for quality, productivity, and cost-effectiveness in the contemporary market, the adoption of advanced technologies like automation and robotics has become imperative.
The Role of Automation in Sand Casting Manufacturing
- Process Automation
- Automation systems can precisely control various parameters in the sand casting process, such as sand mixing ratios, mold compaction pressure, and pouring temperatures.
- This ensures consistent quality and reduces the variability often associated with manual operations.
- Material Handling Automation
- Robotic arms and conveyors can handle the movement of raw materials, molds, and finished castings, minimizing human intervention and the risk of damage or errors.
- Automated storage and retrieval systems can optimize the management of inventory.
- Quality Inspection Automation
- Vision systems and sensors can perform detailed inspections of castings, detecting defects with high accuracy and speed.
- This leads to early detection and correction of quality issues, reducing scrap and rework.
Benefits of Automation and Robotics in Sand Casting Manufacturing
- Increased Productivity
- Robots can work around the clock without fatigue, significantly increasing the output of sand casting manufacturing facilities.
- Faster cycle times and reduced downtime result in higher production volumes.
- Improved Quality
- The precision and repeatability of automated processes lead to more consistent and higher-quality castings.
- Minimized human errors contribute to better dimensional accuracy and surface finish.
- Cost Reduction
- Reduced labor costs as robots can replace some manual tasks.
- Lower scrap rates and rework costs due to improved quality control.
- Energy savings through optimized process control.
- Enhanced Workplace Safety
- Robots can handle hazardous or heavy tasks, reducing the risk of workplace injuries to human workers.
Types of Robotics and Automation Applications in Sand Casting Manufacturing
- Industrial Robots for Mold Handling
- These robots can precisely position and manipulate molds during the casting process, ensuring accurate alignment and reducing the risk of mold damage.
- Examples include articulated robots and SCARA robots.
- Automated Pouring Systems
- Controlled by advanced sensors and algorithms, these systems can ensure the precise and consistent pouring of molten metal into the molds.
- Reduces the variability in pouring and improves the quality of the castings.
- Robotic Deburring and Finishing
- After the casting process, robots can perform deburring, grinding, and polishing operations to achieve the desired surface finish.
- Improves the efficiency and consistency of the finishing process.
Challenges in Implementing Automation and Robotics in Sand Casting Manufacturing
- High Initial Investment
- The acquisition and installation of advanced automation and robotics systems require a significant upfront capital expenditure.
- This can pose a financial burden for some sand casting manufacturers, especially small and medium-sized enterprises.
- Complex Integration
- Integrating robotics and automation systems with existing manufacturing infrastructure and processes can be complex and time-consuming.
- Compatibility issues with legacy equipment and software may arise.
- Skills Gap
- Operating and maintaining automated and robotic systems require specialized skills that may be lacking in the existing workforce.
- Training and upskilling of employees are necessary but can take time and resources.
- Programming and Customization
- Customizing the robotics and automation software to meet the specific requirements of sand casting manufacturing processes can be challenging.
- Frequent reprogramming may be needed to adapt to changes in production.
Success Stories of Automation and Robotics in Sand Casting Manufacturing
- Company A
- Company A implemented a fully automated sand mixing and mold preparation system, which resulted in a significant improvement in the quality and consistency of molds.
- The use of robotic arms for mold handling reduced the risk of damage and increased productivity by 30%.
- Company B
- Company B adopted an automated pouring system with real-time temperature and flow control. This led to a reduction in defects and a 25% increase in production capacity.
- They also utilized robotic deburring stations to improve the surface finish of castings and reduce labor costs.
Future Trends and Prospects of Automation and Robotics in Sand Casting Manufacturing
- Advancement in Sensor Technology
- The development of more sensitive and accurate sensors will enable better process monitoring and control in sand casting.
- This will further enhance quality and productivity.
- Integration of Artificial Intelligence and Machine Learning
- AI and machine learning algorithms will be used for predictive maintenance of equipment, optimizing process parameters, and defect detection.
- Self-learning systems will adapt to changing production conditions.
- Collaborative Robots (Cobots)
- Cobots will work alongside human workers, providing assistance and enhancing productivity while maintaining a safe working environment.
- Their ease of programming and flexibility will make them more accessible for sand casting manufacturers.
Conclusion
The integration of automation and robotics in sand casting manufacturing offers numerous benefits, but also comes with its set of challenges. However, as technology continues to advance and costs decrease, the adoption of these technologies is expected to increase. Sand casting manufacturers that embrace automation and robotics and effectively manage the associated challenges will be well-positioned to thrive in the competitive global market.
Automation and Robotics Applications | Benefits | Challenges | Success Stories |
---|---|---|---|
Process Automation | Consistent quality, increased productivity | High initial investment, complex integration | Company A |
Material Handling Automation | Minimized errors, enhanced safety | Skills gap, programming/customization | Company B |
Quality Inspection Automation | Reduced scrap, better quality control | – | – |
The above table provides an overview of the applications of automation and robotics in sand casting manufacturing, their benefits, challenges, and some success stories.
Here is a list of recommended steps for sand casting manufacturers considering the implementation of automation and robotics:
- Conduct a detailed assessment of current processes and identify areas where automation can have the most significant impact.
- Develop a clear business case and ROI analysis to justify the investment.
- Partner with experienced system integrators and suppliers.
- Provide comprehensive training for employees to work with the new technology.
- Start with pilot projects to test and refine the implementation before scaling up.
By following these steps and staying updated with the latest technological developments, sand casting manufacturers can unlock the full potential of automation and robotics and drive their businesses forward.