The casting structure and technical requirements of the GEVO16 diesel engine cylinder block, elaborates on the original production process and the existing sand inclusion defect of the casting, analyzes the main causes of its occurrence, and takes corresponding preventive measures: (1) Make rounded corners around the waist round hole core to prevent the existence of weak sand; (2) Make anti-pressure rings around the square window of the V-shaped core and the edge where the upper side cores contact each other to prevent the sand core from being bruised, and make sand collecting pits around the core seats of the V-shaped core, the front and rear end cores, etc., to avoid the broken sand from falling into the mold cavity; (3) Improve the front core print, control the surface quality of the core before the cores setting, and cover the cavity with plastic sheeting to prevent the external broken sand from falling in. The production results show that more than 600 cylinder blocks have been produced, and the scrap rate is less than 0.3%, which has achieved good results.
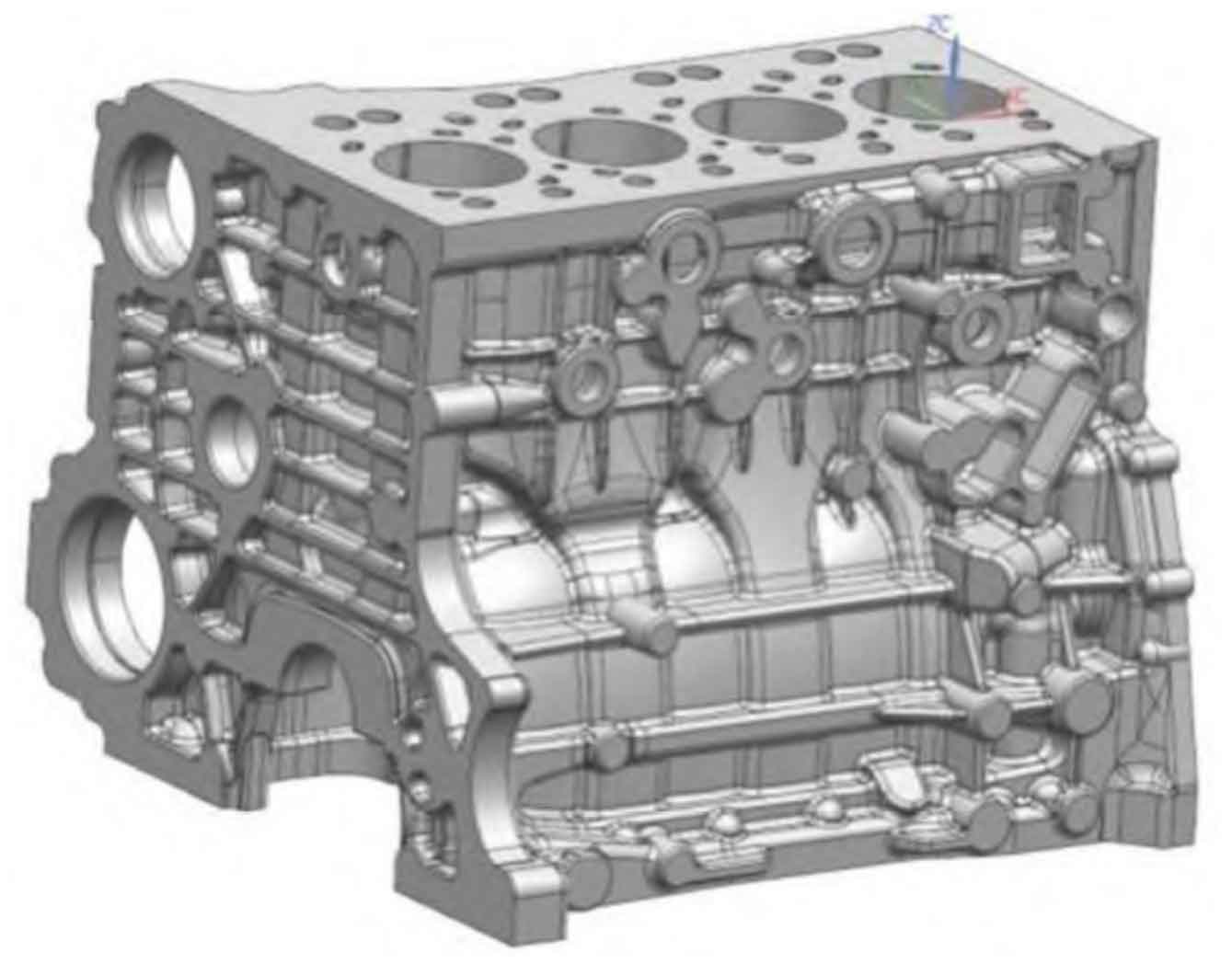
The GEVO16 cylinder block is a key casting for the diesel engine of the mainline HXN5 locomotive. Its main external dimensions are 3,987 mm × 1,458 mm × 1,320 mm, the casting weighs about 7.5 tons, the maximum wall thickness is nearly 200 mm, and the minimum wall thickness is only 14 mm. It has the characteristics of complex internal cavity structure, large difference in wall thickness, and high dimensional accuracy.
The technical requirements are relatively high. The main bearing seat and other parts need to undergo radiographic inspection with relatively high requirements, and the acceptance standard is implemented according to the American X-ray inspection ASTM-E446-2015 and ASTM-E186-2010, requiring to reach level II; the internal gate and cylinder head bolt holes and other parts need to undergo ultrasonic flaw detection.
1. Original Production Process and Existing Defects
1.1 Original Production Process
The furan resin self-hardening sand core assembly molding is adopted, the strength of the molding sand is greater than 0.6 MPa, and the water-based zirconium powder coating is used. A stepped gating system is adopted, and the lower inner gate is introduced from the outside of the camshaft cavity, while the upper inner gate is introduced from the outside and slightly above the horizontal bolt hole.
1.2 Existing Defects
During the trial production and small batch trial production of the GEVO16 diesel engine cylinder block casting samples, it was continuously found that there were sand inclusion defects in the water cavity bosses and other parts of multiple cylinder blocks, which seriously affected the product quality and also affected the production progress for a time.
1.3 Defect Analysis
The sand inclusion defect is a common defect in sand casting, which is a hole-like defect that wraps sand grains or sand blocks inside or on the surface of the casting [5-6]. The existence of this defect will have an adverse impact on the strength and sealing performance of the product, and will also cause impact damage to the tool during the processing in the next step. Therefore, it should be resolved as soon as possible.
When four cylinder blocks were continuously processed, there were sand inclusion defects at the top of the water cavity of the cylinder block, and the positions were relatively fixed. Due to the large size of the cylinder block and the core assembly molding process, there were a large number of sand cores, and the core setting operation was relatively complicated. After combing the entire process and carefully searching for the root cause of the problem, it was found that the main reasons were as follows:
(1) The structure of the GEVO16 cylinder block is complex, and the boss at the bottom of the water cavity is located in the middle of the bottom of the mold cavity, and the structure of the water cavity core also blocks this area, making it difficult to clean up and inspect the residual sand in this area during the sand core assembly.
(2) The sand core segmentation between the camshaft cavity core and the waist round hole core is unreasonable. Although the core setting is relatively easier, there is sharp-corner sand locally, and the crushing phenomenon is easy to occur during the core setting, resulting in broken sand falling into the mold cavity.
(3) During the core setting, the square window area between the upper side core and the V-shaped core, and the edge where the upper side cores contact each other are prone to friction sand, and the broken sand is difficult to remove after falling into the mold cavity.
2.Preventive Measures
To reduce the sand inclusion defect, it is necessary to start from the source, inspection, removal of the sand, and protection of the mold cavity. The following preventive measures are mainly taken:
(1) Improve the sand core segmentation between the camshaft cavity core and the waist round hole core, eliminate the phenomenon of sharp-corner sand, and make rounded corners around the waist round hole core to prevent the existence of weak sand.
(2) Make anti-pressure rings around the square window of the V-shaped core and the edge where the upper side cores contact each other to prevent the sand core from being bruised, and make sand collecting pits around the core seats of the V-shaped core, the front and rear end cores, etc. to collect the friction sand, thereby avoiding the broken sand from falling into the mold cavity.
(3) Improve the front core print to facilitate the inspection of whether there is accidentally fallen broken sand at the bottom of the mold cavity, and at the same time improve the structure of the sand blocking core in the rear bottom box to facilitate the blowing clean of the broken sand.
(4) Control the surface quality of the sand core before the core setting. Before the core setting, pay attention to inspect the surface quality of the sand core, there should be no floating sand, debris, sand cracks, etc., and there should be no coating defects, and the core should be set into the mold cavity cleanly.
(5) During the core setting break and after the core setting is completed until the filling of the sand before the mold closing, the mold cavity should be covered with plastic sheeting to prevent the external broken sand from falling in.
(6) Make a special air duct to remove the broken sand found during the inspection.
3. Production Verification
After taking the above measures, more than 600 cylinder blocks have been produced, among which only 2 have sand inclusion defects, and the scrap rate is less than 0.3%, which has achieved good results.
4. Conclusion
(1) Reasonable sand core segmentation can eliminate the existence of sharp-corner sand, avoid the occurrence of crushing phenomenon, and thus avoid the generation of sand inclusion defects.
(2) The application of anti-pressure rings and sand collecting pits can prevent the friction sand during the core setting and avoid the broken sand from falling into the mold cavity.
(3) Covering the mold cavity with plastic sheeting before the mold closing can prevent the external broken sand from falling into the mold cavity, thereby preventing the generation of sand inclusion defects.
Defect | Description | Impact | Solution |
---|---|---|---|
Sand Inclusion Defect | Holes wrapped with sand grains or sand blocks inside or on the surface of the casting | Affects the strength and sealing performance of the product, and causes damage to the tool during processing | – Improve the sand core segmentation to eliminate sharp-corner sand and make rounded corners to prevent weak sand. – Make anti-pressure rings and sand collecting pits to prevent friction sand and avoid broken sand from falling into the mold cavity. – Improve the front core print and the structure of the sand blocking core for inspection and cleaning. – Control the surface quality of the sand core before setting and cover the mold cavity with plastic sheeting to prevent external broken sand from falling in. – Use a special air duct to remove the broken sand found during inspection. |