Abstract
This comprehensive article delves into the challenges encountered in the production of hollow valve plate sand casting parts made from Austenitic Stainless Steel CF8M. It meticulously analyzes the root causes of crack defects in the sealing surfaces of these castings and proposes effective mitigation strategies. The study emphasizes the significance of heat treatment, chemical composition, metallurgical analysis, and foundry process design in preventing crack formation. By incorporating modifications to the casting process, such as the use of chilling materials and optimization of the gating system, the article demonstrates a substantial reduction in the crack defect rate, enhancing product quality and reducing manufacturing costs.
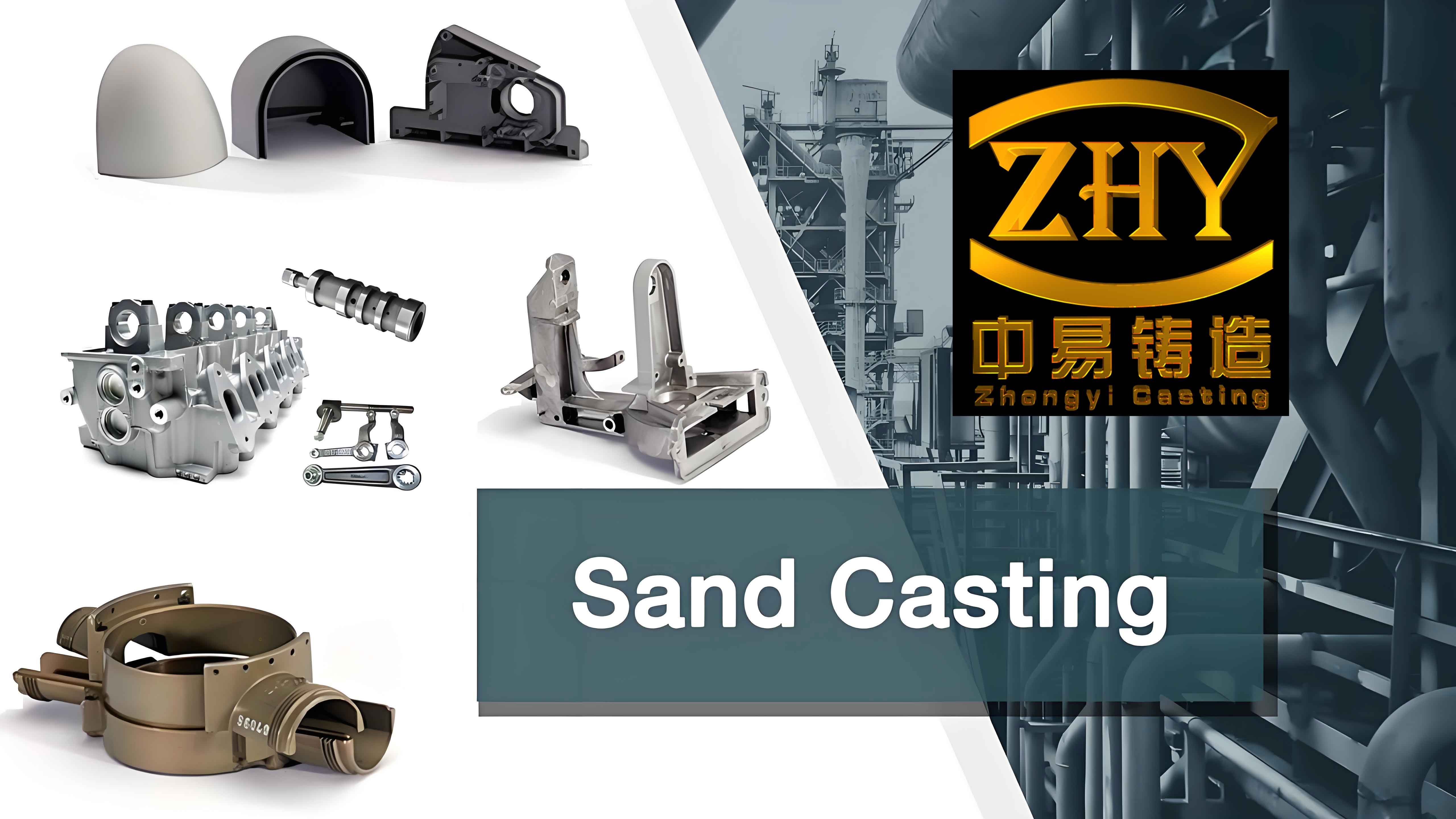
Introduction
Austenitic stainless steel CF8M is widely used in the production of hollow valve plate sand casting parts due to its excellent corrosion resistance and mechanical properties. However, the manufacturing process of these castings is prone to various defects, with crack formation in the sealing surfaces being a particularly challenging issue. These cracks can significantly compromise the sealing performance of the valves, leading to high rejection rates and increased production costs.
This article presents a detailed investigation into the causes of crack defects in CF8M hollow valve plate sand casting parts and outlines the strategies employed to eliminate these defects. By leveraging insights from heat treatment, chemical analysis, metallurgical evaluation, and foundry process design, we aim to provide a comprehensive understanding of the issue and practical solutions for manufacturers.
1. Background and Problem Statement
1.1 Material and Casting Specifications
The hollow valve plate castings under investigation are made from ASTM A351 CF8M Austenitic Stainless Steel. These castings have a maximum wall thickness of 45 mm and a minimum wall thickness of 7 mm, with an overall outline dimension of 400 mm × 65 mm. The casting process involves water glass self-hardening sand molding, coated sand hot-box core making, and manual pouring using a 2T electric furnace. The castings undergo a solid solution treatment before being shipped for further processing and assembly into valves destined for the European market.
1.2 Problem Identification
Starting from late 2014, a significant number of castings were rejected due to crack defects in the sealing surfaces. By April 2015, out of 345 castings processed, 107 were scrapped due to these defects, resulting in a waste rate of approximately 31%. This high rejection rate significantly impacted production efficiency and customer delivery timelines, placing immense pressure on the supplier to find a solution.
2. Quality Problem Analysis
To identify the root causes of the crack defects, a comprehensive analysis was conducted encompassing heat treatment, material composition, metallurgical structure, and foundry process design.
2.1 Heat Treatment Process Evaluation
The solid solution treatment process was closely monitored to ensure it met the specified requirements. The castings were heated to 1080°C and held for 2 hours before being quenched in water. The entire process was found to be in compliance with the established procedure, and post-heat treatment inspections revealed no crack defects. This indicated that the heat treatment process was not the primary cause of the cracking issue.
Table 1: Heat Treatment Process Parameters
Parameter | Value |
---|---|
Heating Temperature | 1080°C |
Holding Time | 2 hours |
Quenching Medium | Water |
2.2 Material Composition and Metallurgical Analysis
Chemical composition analysis was conducted on samples taken from the crack locations, following ASTM E1019-11 and ASTM E1086-14 standards. The results showed that all elements, except for Cr, which was slightly below the standard lower limit, met the CF8M requirements. The low sulfur content ruled out the formation of low-melting-point FeS as a contributing factor to cracking.
Table 2: Chemical Composition Analysis Results
Element | Measured (%) | CF8M Standard (%) |
---|---|---|
C | 0.047 | Max 0.08 |
Si | 0.83 | Max 1.50 |
Mn | 0.93 | Max 1.50 |
3. Further Discussion on Process Improvements
The successful elimination of cracking defects in the austenitic stainless steel hollow valve plate sand castings underscores the importance of comprehensive process analysis and targeted interventions. As demonstrated in the case study, several key factors were identified and addressed effectively.
3.1 Reduction of Wall Thickness Differences
The introduction of chilled materials, specifically chromite sand, significantly reduced the thickness disparity within the casting. By placing the chromite sand layer at approximately twice the maximum wall thickness (45 mm) and covering over 20% of the thickest areas, the localized overheating during solidification was minimized. This, in turn, lessened the thermal stress-induced residual stresses, which were a primary cause of cracking.
3.2 Modification of Gating System
The modification of the gating system focused on equalizing the cooling rates across the casting. By reducing the ingate thickness from 14 mm to 7 mm (matching the adjacent casting wall thickness), the ingate area was no longer a hot spot, ensuring uniform solidification with the rest of the casting. Furthermore, the enlargement of the ingate width and the use of customized risers with strategic positioning minimized the heat transfer from the sprue to the ingate, preventing the ingate from becoming overly hot.
3.3 Closed Gating System Advantages
The adoption of a closed gating system not only facilitated better control over the metal flow but also served as a barrier against slag and impurities entering the casting. This enhanced the overall quality of the casting, further reducing the risk of defects.
4. Verification of Improved Quality
The effectiveness of the proposed measures was validated through rigorous testing and production trials. After implementing the modifications, 10 test castings were produced, and no cracking defects were observed during the opening and initial inspections. Following this success, a larger batch of 50 castings was produced, confirming the consistency and reliability of the improvements. The final statistics revealed a significant drop in the internal scrap rate from 35% to below 3%, highlighting the substantial improvement achieved.
5. Customer Feedback and Cost Savings
The customer feedback received after the implementation of the improvements was positive, with the overall scrap rate during finishing reducing from 31% to 1.53%. This not only improved customer satisfaction but also reduced the financial burden on the supplier, saving approximately USD 280,000 over the implementation period.
6. Conclusion and Recommendations
In conclusion, the study underscores the critical role of process analysis and optimization in addressing casting defects. The following key takeaways are recommended for similar applications:
- Regular inspections, particularly during the opening and initial stages of processing, are crucial for early detection of cracks.
- The use of chilled materials can significantly reduce wall thickness variations and associated thermal stresses.
- Pouring system design should be tailored specifically to sand casting requirements and not merely adapted from precision casting practices.
- Pre-shipment quality control measures, such as rough machining and non-destructive testing, can mitigate risks and reduce batch failures.
By implementing these strategies, manufacturers can improve casting quality, reduce scrap rates, and enhance overall profitability.